技術解説 プラスチック成形のDXに向けての取組み
秋元技術士事務所
秋元英郎
1.はじめに
本稿はプラスチックスエージの2022年8月号に掲載された記事を元に加筆修正したものである。プラスチックスエージ社の廃業に伴い、オンラインでも閲覧できない状態にあるため、新しい記事として執筆した。最初の執筆時点から約2年経っており、その間にK2022, IPF2023が開催されたので、最新の情報に抜けがあることをご了解いただきたい。
DX(デジタルトランスフォーメーション)とは、デジタルの力を借りて、仕事のやり方を大きく変えることである。DXのステップは「アナログデータをデジタル化する」、「データを蓄積する」、「蓄積されたデータを解析して、最適で革新的な仕事のやり方に変える」ステップが含まれる。
DXと勘違いされやすい言葉にデジタル化(デジタリゼーション)がある。これは前述したようにDXの最初のステップである。今成形現場ではこのデジタリゼーションが進んでいる。DXを実現するためには成形に関わる全ての工程でデジタル化が必要になる。
本稿では最初にプラスチック成形におけるDXとはどのような事かについて述べる。その後にデジタル化の流れについて欧米の例も含めながら取り組みを紹介する。
2.プラスチック産業におけるDXの方向性
2018年に経済産業省が発表したDXに関するガイドライン(現在はサイトから削除されている)では「企業がビジネス環境の激しい変化に対応し、データとデジタル技術を活用して、顧客や社会のニーズを基に、製品やサービス、ビジネスモデルを変革するとともに、業務そのものや、組織、プロセス、企業文化・風土を変革し、競争上の優位性を確立すること。」と書かれている。プラスチック産業におけるDXは製品企画、製品設計、金型設計、成形、流通等のすべての工程がデジタルの力でシミュレーションされ、更には「最適化」されることを示す。
本章では、T-ゼロ生産方式とデジタルツインの関係に関する紹介とシミュレーションを利用して更に最適化に取り組んでいる例を紹介する。
2-1 T-ゼロ生産方式
T-ゼロとはゼロ回目の試作(トライ)のことを意味し、そこから転じて試作を行わずにいきなり生産を始める生産方式である。そのためには、この製品設計、金型設計、成形材料、成形条件で生産すれば絶対に問題が無いことがあらかじめわかっている必要がある。もちろん、過去に生産実績が無い新規製品でである。
T-ゼロ生産方式の実現のために有力と考えられているのが、仮想空間(デジタルの世界)で製品設計・金型設計・生産・検査の一連の流れを実行し、不具合があれば仮想空間の中で修正する方法である。図1は射出成形の完全三次元シミュレーションソフト「Moldex3D」の開発元であるCoreTech Systemが販売代理店向けに作成した説明資料1)から、同社から特別に許可を得て掲載するものである。図中の左側が仮想空間で行う部分である。
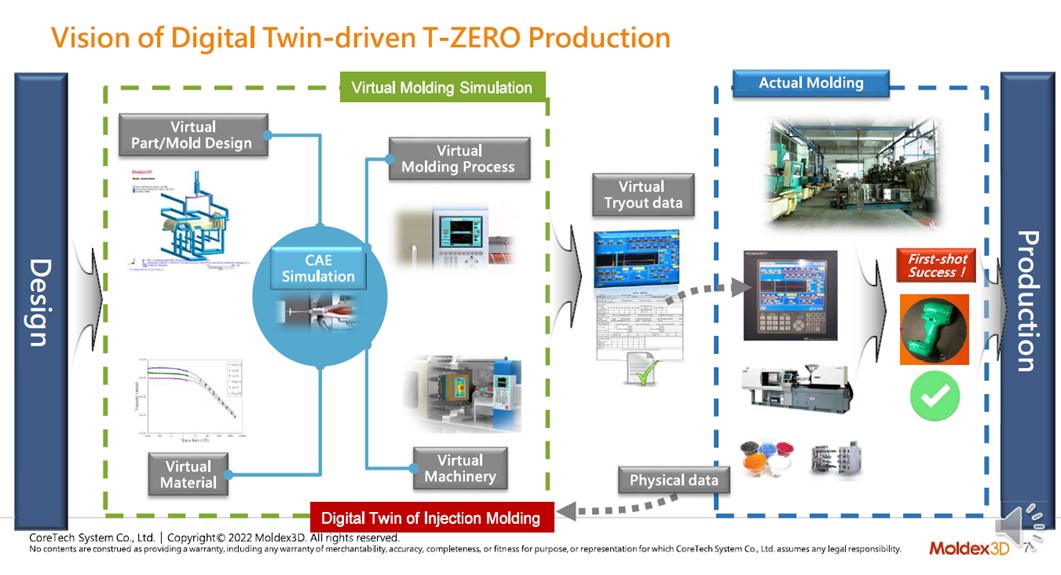
図1 試作ゼロ生産方式の考え方
仮想空間で仮想生産を行うためには最終的な成形品のデジタルデータ、冷却配管等を含む金型のデジタルデータ、材料のデジタルデータ、成形機のデジタルデータが必要である。この仮想空間で行う生産が実際の生産の状況を予見するためには、シミュレーションに用いるデジタルデータの精度が十分に高い必要がある。ゴミのようなデータからは使えない結果しか得られない。これらの中で、特に射出成形機の特性は重要である。機種による違いのみならず、使用状況による装置の状態変化も考慮する必要がある。
図中の右側は、実際の成形との比較とフィードバックである。仮想空間での試作結果を現実の試作結果と比較して、シミュレーションの精度を高めることで、次のプロジェクトの成功確率が上がっていく。
2-1-1 デジタルツイン
デジタルツインとは現実空間と瓜二つのものをデジタル空間に置くシミュレーション技術の一部と考えられている。世界で最初のデジタルツインの活用はアポロ13号である。デジタルツインは現実の世界を限りなく忠実に再現し、現実の世界と同じスピードで動く。厳密な意味でのデジタルツインは現実との同時性も求められるが、T-ゼロ生産方式で用いるデジタルツインは同時である必要は無く、現実の世界に代わりに作業を先に進めておくことが可能である。
2-1-2 射出成形プロセスで必要なデジタルツイン技術
射出成形に関して、製品品質に影響を与える5つのデジタルツインは材料,製品・金型設計,成形機,成形条件であり、特に材料,金型設計,成形機の特性が重要となる。
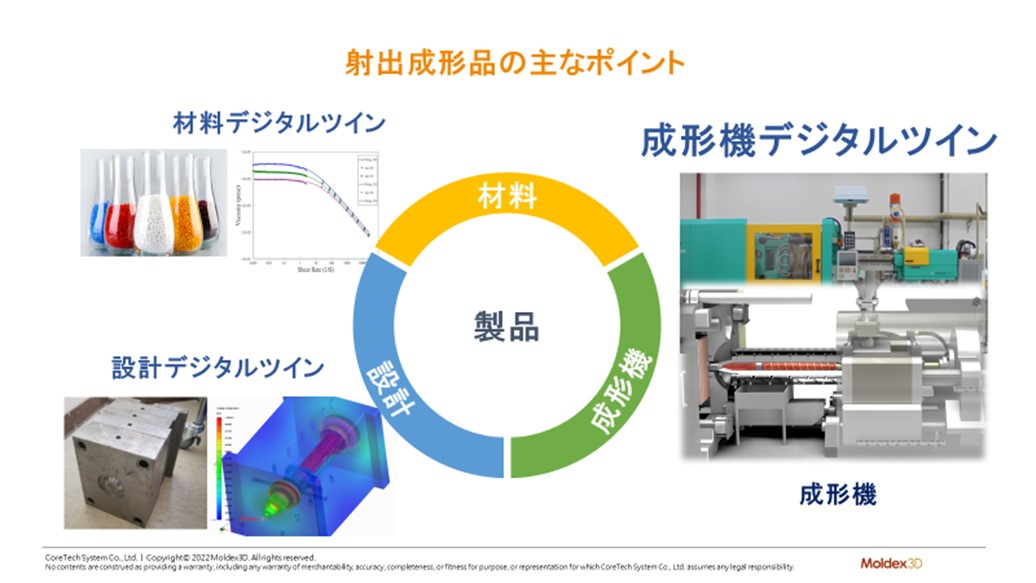
図2 射出成形におけるデジタルツインのポイント2)
材料に関しては、結晶化の考慮や繊維配向、繊維強化材料の流動降伏の考慮が課題である。金型に関しては、三次元配管を含めた冷却の実態やベントの影響の再現が必要である。
成形機のデジタルツインの要素は、スクリュー形状、ノズル形状、型締ユニットの機構と動作、加熱等のヒーター制御、成形機制御のアルゴリズム、成形機の動作の応答性等が考慮される項目である。当然ながら設定値に関してはメーカー毎で定義自体が違うことがある。
成形機の動作の応答性に関しては特に重要である。現在使用されている射出成形機の多くは、射出速度を設定しその速度に応じて圧力が発生する。射出を開始しても瞬時に設定の速度に到達するのではない。図3には射出速度のパターン例を示した。Aは比較的速度の立ち上がりが速いのに対し、Bは立ち上がりが遅く、Cに至っては立ち上がりが遅いばかりでなく後半では設定値よりも速くなっている。その結果として同じタイミングでも充填のようすが異なる。射出成形機デジタルツインでは、このような特性も計算に反映させる必要がある。
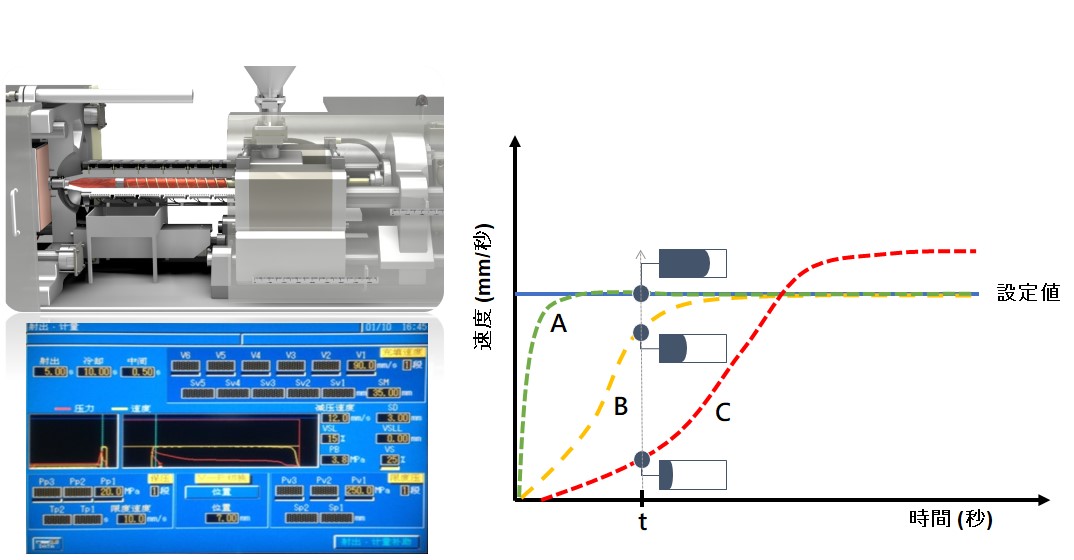
図3 射出速度のレスポンス2)
2-1-3 T-ゼロ生産方式が実現する社会
前述のようにデジタルツイン技術の進歩により、試作を繰り返すこと、金型を修正すること、材料を微調整すること、成形条件を変更すること、成形機を変更すること、製品形状を見直すことが全て仮想空間上で実施できる。これにより、金型修正のために何往復もする金型運搬のエネルギー、試作に必要な材料、試作のために成形機を動かすエネルギー等を大幅に削減することができ、開発期間の短縮にもつながる。まさに環境に優しいものづくりが実現できる。
2-2 プラスチック成形における最適化
前節で述べたデジタルツイン技術を用いたT-ゼロ生産方式は、実空間での試作をゼロにすることはできるものの仮想空間での試作は必要である。仮想空間でトライアンドエラーを行うのではなく、人工知能を用いた最適化も必要になってくる。射出成形機の分野では古くからエキスパートシステムという人工知能の前段階的な技術が存在していた。現在では機械学習の技術が進歩してより現実的になってきている。
2-2-1 古典的なエキスパートシステム
今から30年前の1992年に出願された特許文献3)「射出成形機の成形品質向上システム」の請求項1には「射出成形機の成形立ち上げ時に試射の繰返しにより、成形品の成形不具合を解消するための成形条件出しを行う射出成形機の成形品質向上システムにおいて、射出成形時に起こり得る成形品質不良に関する解消方法データを記憶する長期記憶手段と、実際に発生した品質不良に関する解消方法データを前記長期記憶手段から抽出して記憶する短期記憶手段と、成形品の品質状態を入力・記憶する手段と、成形機の成形状態を入力・記憶する手段と、前記品質状態と前記成形状態と前記短期記憶手段に記憶されている解消方法データとに基づいて成形品の品質を向上させる成形条件を決定する評価手段と、を備えたことを特徴とする射出成形機の成形品質向上システム。」と記載されている。
この方法では、高度な技能者が不良現象に対して対処した方策とその結果をデータベース化して、必要に応じて呼び出すことが可能な仕組みになっている。このような取り組みを土台として、「IoTと機械学習4)」を組み合わせた現在の「成形工場のスマート化」につながっている。成形工場のスマート化については後述する。
2-2-2 最適化設計
設計には、概念設計、基本設計、詳細設計、生産設計がある。機械学習による最適化において最初の難関が概念設計の部分であり、設計者やユーザーの感性を含めて欲しい製品の条件が全て数値化されないと基本設計以降に進むことができない。設計コンセプトが定量的に取り扱いできるようになれば、シミュレーション技術を使いながら最適化が可能になる。
金沢大学の北山教授のグループでは、製造工程における最適化の実証として射出成形におけるプロセスパラメーターの最適化に取り組んでいる5)。箱型の成形品の反りを低減してサイクルタイムも経済的な範囲に収める例では、設計変数として充填工程(溶融温度、射出時間)、保圧工程(可変保圧プロファイル2種類)、冷却工程(冷却温度、冷却時間)の8パターン、目的関数としてサイクルタイムの最小化と反りの最小化の2つを設定している。反りとサイクルタイムはトレードオフになるので、シミュレーション結果(この場合はMoldex3Dを用いた計算結果)より得られる「反りの値が許容範囲内に入る最小のサイクルタイムを与える成形条件」が最適条件としている。
図4に金沢大学の北山教授のグループと(株)ソディックによる共同研究の結果の図を引用して示す。図中(a)は反りとサイクルタイムのトレードオフ、(b)は金型温度とサイクルタイムのトレードオフ、(c)は反りと金型温度のトレードオフを示している6)。ただし、金型温度はウェルドラインを消すため行う高速ヒートサイクル成形の金型加熱温度である。
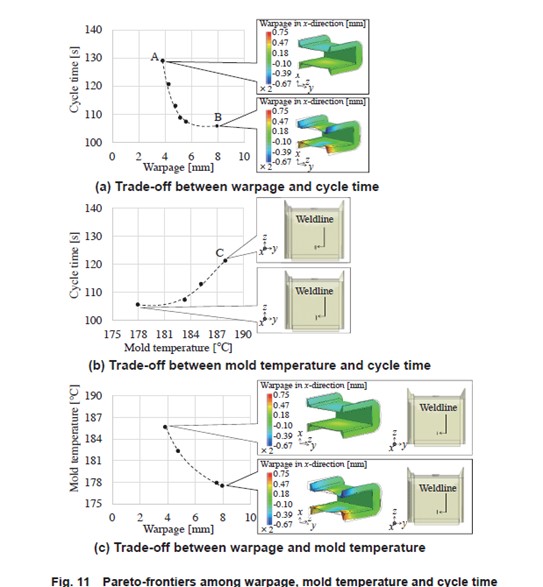
図4 金沢大学北山教授のグループによる反り、サイクルタイム,金型温度間のトレードオフ検証結果
3.デジタル化によるスマートファクトリー
第2章で紹介したDXの話はプラスチック成形の将来像であるが、デジタル化によりスマート工場化する取り組みは国内外の展示会で積極的に紹介されている。すべてを網羅はできないが、企業ごとにいくつか紹介する。
3-1 射出成形機と周辺のIoTおよび生産管理技術
3-1-1 (株)日本製鋼所の「J-Wiseソリューション」
プラスチック射出成形用IoTツールであり、射出成形機のデータ収集システム「NET100」、成形データを常時監視システム「AIモールディングナビゲータ」から構成される。「NET100」は24時間監視により不良時にアラームを出す(見える化)、経年劣化するパーツにセンサーを取り付けて情報を得て交換タイミングを知らせる(維持保全)等を行う。「AIモールディングナビゲータ」は成形品の画像データや成形データを常時監視して、不良発生を未然に防いで24時間無人生産の支援を行う。
3-1-2 住友重機械工業(株)の生産管理システム「i-connect」
生産現場のさまざまな機器をネットワークで接続するものであり、成形機と周辺機器の運転データをまとめて一元管理し、過去の稼働データを呼び出して改善につなげることを可能にしている。また、モバイル端末に対応しており、端末から運転日報をペーパーレスで作成することも可能にしている。
3-1-3 (株)ソディックの「V connect」・「eV-LINE MR30」・「ICF-Vスケジューラー」
「V connect」は射出成形機を接続して稼働状況や各種履歴を管理し、蓄積した成形データをモニターして抽出ができるシステムであり、最大20台の成形機が接続可能である。自動生産システム「eV-LINE MR30」は電源ON→金型と樹脂をセット→シリンダーと金型を昇温→パージおよび廃材処理→生産開始→生産→生産終了→次工程へ ・・・→すべての生産終了後の終了作業(降温)→電源OFFをすべて自動で行うシステムである。「ICF-Vスケジューラー」は最適な生産スケジュールを組んで、自動生産を行うシステムである。
3-1-4 芝浦機械(株)の「iPAQET code system」
成形機、金型、材料、取出機にそれぞれ固有の二次元バーコートをつけておき、その組み合わせから自動で条件を設定するものである。これを使うと、材料の色ごとに別々なコードを与えておけば、色ごとに決まった条件が立ち上がる。また、同社のIoTソリューションを使うことで、「iPAQET」による遠隔コントロールや、製品に印字された二次元バーコードによる製品管理が可能になる。
3-1-5 ENGELの「INJECT 4.0」
「iQ process observer」成形の4つの工程を監視してデータを集めショット内で条件修正する。「iQ melt control」は材料の可塑化条件を最適化する。「iQ weight control」は製品重量の変動を自動的に補正して一定範囲に制御する。「iQ clamp control」は型締力を(必要最低限の値に)自動的に調整する。自動的に効率的な温度制御を提供する「iQ flow control」は材料の粘度を一定に保つために自動的に晴れる温度を制御する。
3-2 メーカーが異なる装置が混在する場合の対応
前述のように工場内の射出成形機と周辺機器をネットワーク化する取り組みは射出成形機メーカーが中心となって進められている。この問題点は異なる機械メーカーの装置が混在するとうまく機能しないことである。
3-2-1 ユーロマップ
欧州のプラスチックおよびゴム業界の主要メーカーから成る統括組織であり、活動内容の中に技術的な推奨規格を策定して普及させる活動がある。その前に「OPC-UA」に触れる必要がある。「OPC-UA」とはファクトリーオートメーション分野やその他業界の各機器間でプラットフォームに依存せずに安全にデータ交換を行うための標準規格である。「OPC-UA」に準拠して射出成形機を接続する規格である「EUROMAP 77」と周辺機器を接続するための企画である「EUROMAP 83」がリリースされている。
3-2-2 日本国内での動き
日本国内でもユーロマップに合わせる動きはあるが、これから製造される装置に限定される。現実的な課題としては、すでに保有して稼働している成形機や周辺機器から適切にデータを取り出すことにある。ここでは、古い機械からデータを取り出すための取り組みを紹介する。
(株)アスカコネクトの「MyCFM」は既設の射出成形機のタイバーに歪みセンサーを取り付けて、成形機の型締力データを収集して解析するシステムである。型締力を追跡するだけでも異常の前触れを察知することは可能とのことである。
プラスチック成形工場向けではないが、(株)日進製作所の「サガネ係長のIoT」という不思議なネーミングのアプリケーションがある。命名したのは事業パートナーである三菱商事テクノス(株)であろう。このアプリケーションは、古い設備や特殊な設備からデータを取得することにかけて世界一であるLitmus Automation社のソフトウエア”Litmus Edge”を活用して金属加工装置を接続し、装置の不稼働要因を突き止め、改善につなげるものである。
近畿経済産業局・ムラテック情報システム㈱・(一社)西日本プラスチック製品工業協会が中心となって行ったIoT推進事業は、射出成形機メーカー・周辺機器メーカー・生産管理システムメーカーが横断的に協力しあって開発したもので、グローバル基準の規格EUROMAP63に準拠した成形機のデータフォーマットの共通化、そのデータを統合するシステムである「ミドルウェア」の開発及びシステムの無償提供による、IoT導入拡大を図る事業に取り組み、「ミドルウェア」が平成29年3月末に完成した7)。この事業で開発した「ミドルウェア」を利用すれば、各社射出成形機から共通したデータを自動で収集することが可能となり、様々な上位システムで活用できるようになる。
4.おわりに
AIが本格的に使われるようになり、この分野は日進月歩である。この記事は最新の情報を収集する際の基礎情報をして活用していただきたい。
参考文献
1) 2022年度Moldex3D販売店向け資料
2) Moldex3D ウェビナー資料「成形機デジタルツイン – 成形機特性分析とケーススタディ」(株式会社セイロジャパンによる翻訳版)
3) 特許公報 特開平5-286005(1992年出願 東芝機械株式会社)
4) 坂東大輔,「IoT開発がしっかりわかる教科書」,株式会社技術評論社,(2022)
5)北山哲士,「工学系のための最適設計法」,共立出版,(2021)
6)北山哲士;石附亮人;高野昌宏;久保義和;合葉修司,設計工学,55(9),559-568(2020)
7)近畿経済産業局プレスリリース(平成28年6月15日)