射出発泡成形の技術動向
秋元英郎
秋元技術士事務所
1 はじめに
プラスチックは他の素材に比べて軽い素材(密度が小さい)であるが、軽いプラスチックを更に軽くして用いる手法の一つが発泡プラスチックである。
本稿では発泡プラスチックの製造プロセスの一つである射出発泡成形について最新の動向(発泡剤供給方法・高倍率化・表面品質向上)を交えながら解説する。
2 発泡成形とは
発泡成形とは,発泡性プラスチックを成形して多孔質成形品を得る成形方法であり、上記の「融かす」・「形にする(流す)」・「固める」の工程に加え「気泡が発生する」・「気泡が成長する」・「気泡の成長が停止する」という工程が加わる.発泡性を付与するために発泡剤が用いられる。
プラスチックに発泡性を付与するために用いられるのが発泡剤である.発泡剤には気体状あるいは揮発性液体状の物理発泡剤、熱分解や中和反応によって気体を遊離させる特徴を持つ化学発泡剤がある。
3 射出発泡成形とは
用語として「射出発泡成形」と「発泡射出成形」の両方が使われている.前者は発泡屋が使うことば、後者は射出成形屋が使うことばであり、実質的に同じである。本稿では前者を用いる。 射出発泡成形とは射出成形のプロセスにおいて発泡性を持った溶融したプラスチックを金型内に射出充填することによって気泡構造を持った成形体を得る成形技術である.使用する発泡剤の種類によって射出成形機を発泡成形用にモディファイすることが必要になる。
3.1 使用する発泡剤と成形装置
成形用の原料プラスチックに発泡性を付与する方法には大きく分けて2つの方法がある。1つは,発泡剤を含んだプラスチックを原料として用いる方法、1つは成形機の中でプラスチックと発泡剤を混ぜる方法である。発泡剤を含んだプラスチックには物理発泡剤が含浸された場合と化学発泡剤やマイクロカプセルが混合された場合がある。これらのケースでは通常の射出成形機がそのまま使用できる。成形機の中で溶融プラスチックと発泡剤を混ぜる方法は特に不活性ガスを発泡剤として用いるときに使用され、射出成形機に発泡剤を注入するための機構を持った専用の射出成形機が必要になる。
参考文献1によると耐圧容器中で30℃以下かつ6.5MPa以下の条件でプラスチックペレットに二酸化炭素を含浸(0.2~2.9%)含浸させ、容器から取出したペレットを速やかに既存の射出成形機に投入して成形することで発泡成形品が得られることが記載されている1)。二酸化炭素の含浸にはおよそ1日要し、溶解量は重量増加分の測定から求める。ポリカーボネートやポリプロピレンを用いて成形した例では気泡径が30~200μmで比重低減率が15~18%の発泡成形品が得られている。二酸化炭素は非晶領域のみに溶解するので半結晶性(例えばポリプロピレン)あるいは非結晶性(例えばポリカーボネート)のプラスチックに適用可能な方法である。
発泡剤として化学発泡剤やマイクロカプセルを用いる方法では成形材料であるプラスチックと発泡剤をドライブレンドで成形機に投入することで成形機内部で溶融プラスチックと発泡剤が混合されて発泡成形品が得られる。このプロセスは特殊な設備が不要であり通常の射出成形機がそのまま使用できる(厳密にはシャットオフノズルが有る方が良い)ため、簡単に発泡成形をテストするには向いている。
物理発泡剤を用いる場合には物理発泡剤(例えば窒素,二酸化炭素)の注入設備が必要であるとともに、注入された物理発泡剤が上流(ホッパー側)に逆流しないような特殊なスクリュー構造は必要になる。注入口をバレルに設ける場合は計量によるスクリュー後退が起こるため、計量ストロークに制限ができる。物理発泡剤の添加方法は液体状の物理発泡剤を射出成形機の射出シリンダーのポンプで注入する方法と気体状の物理発泡剤を溶融プラスチックと接触させて表面から溶解させる方法が代表的である。
3.2 射出発泡成形における気泡発生と気泡成長
射出発泡成形では溶融プラスチックに物理発泡剤あるいは化学発泡剤から発生した分子が計量背圧によって溶解した状態で待機する。射出開始まで背圧が維持される機構によって射出シリンダー内では気泡は発生しない。射出を開始して溶融プラスチックにかかる圧力が飽和圧力以下になると気泡が生成する。
射出発泡成形にはショートショット法とフルショット法があり、気泡生成のタイミングに違いがある。
ショートショット法は低圧法と呼ばれることもあり、金型キャビティ容積よりも少ない容量の溶融したプラスチックを射出し気泡の拡大の力を使いながら充填が進む成形方法である。金型内の溶融プラスチックの圧力が飽和圧力よりも低い状態であるため気泡が拡大しながら充填が進行する。図1にショートショット法の充填イメージを示した。
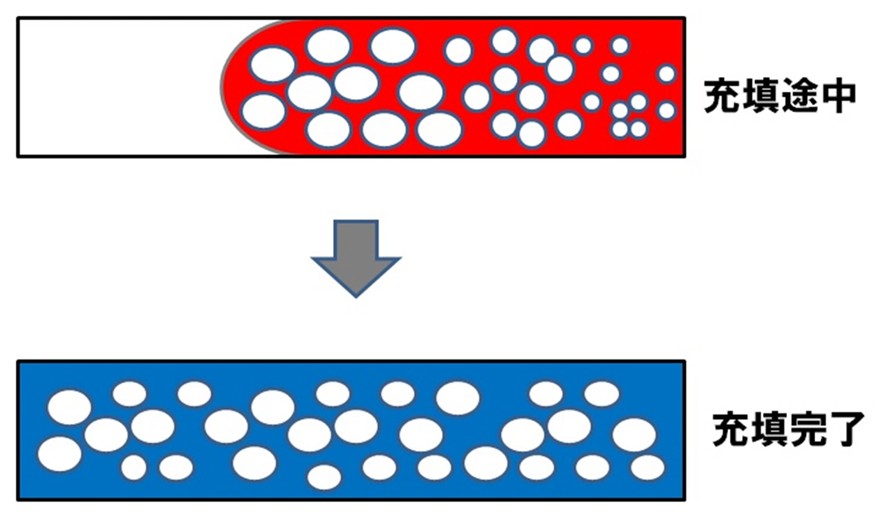
図1 射出発泡成形におけるショートショット法
射出成形機から射出されて金型のキャビティに流れ込んだ溶融プラスチックはゲートを通過した後に圧力解放されて気泡が生じる。気泡の拡大分が金型キャビティ容積に不足する分を補ってキャビティを完全充填させる。ショートショット法で得られる軽量化の効果は製品形状・金型形状に依存するが、おおむね10%程度である。
ショートショット法の代表的な用途としてストラクチュアルフォームが挙げられる。ストラクチュアルフォームは古くから使われている構造部材用発泡成形品である。一般的に射出発泡による成形品は金型に接触した部分に気泡が存在しないソリッドスキン層を形成し、ソリッドスキンに挟まれる形で発泡コア層を形成する。図2には射出発泡成形品の断面のモデル図を示した。
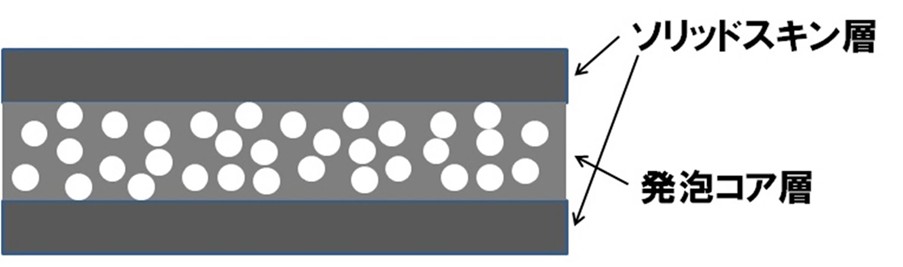
図2 一般的な射出発泡成形品の断面構造
射出発泡成形において、金型内における溶融プラスチックの流動は前述のように気泡の拡大に助けられるため、金型内圧力がそれほど高くならず型締力が小さくて済む。ストラクチュアルフォームの設計上の利点は、ソリッド成形品よりも軽い・大型製品に対応可能・厚肉製品も可能・金型コストが安価・ヒケが目立たない等の点である。ソリッドに比べた製品の利点としては、剛性と重量のバランスが良い・製品のひずみが小さい・断熱性に優れる・遮音性に優れる・電気絶縁性に優れる等が挙げられる。
フルショット法は高圧法と呼ばれることもある。金型キャビティ容積と等しい体積の溶融プラスチックを金型キャビティ内に充填し、固化収縮時に圧力が低下して冷却が遅い部分から気泡を生成させる。固化収縮分を気泡の発生・拡大で補う考え方の発泡成形方法である2,3)。フルショット法のイメージ図を図3に示した。特に厚肉製品(例えば事務机の肘掛)におけるヒケ防止で用いられる手法であり発泡剤の添加量は少量にして表面にスワールマーク(シルバーストリーク)が発生しない条件で成形を行う。フルショット法では金型内圧力が高いために気泡の拡大が制限され、軽量化の効果が小さく3~5%程度である。
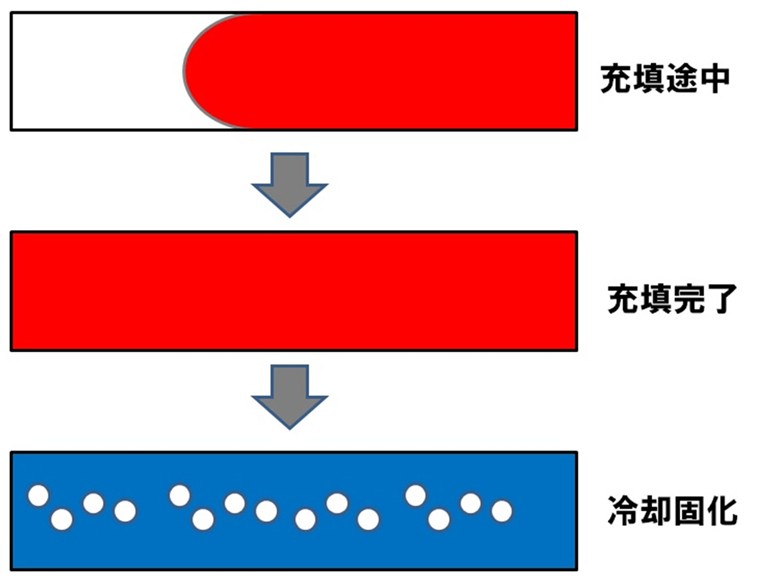
図3 射出発泡成形におけるフルショット法
ショートショット法とフルショット法を分けて説明したが、実際の射出発泡成形においては飽和圧力以上の圧力で充填が進行する部分と飽和圧力以下の圧力で充填が進行する部分が混在する。例えばゲートに近い部分が飽和圧力より高くゲートから離れると飽和圧力より低くなって,気泡のようすに違いが生じることがある。
3.3 射出発泡成形の長所と短所
射出発泡成形品は発泡していない成形品(ソリッド成形品)と同じ形状で比較すると、気泡構造を含む分剛性や強度が低くなる。そのため射出発泡成形に合わせた製品設計が必要になる。
射出発泡成形よって軽量化が可能になるが軽量化の度合いは大きくない。押出発泡成形やビーズ発泡成形のように2倍~30倍といった高発泡倍率は期待できない。高倍率を得るためには後述するコアバック法が有効である。
射出発泡成形では成形品表面にスワールマークと呼ばれる白い筋状の模様が発生することが多い。スワールマークは流動末端で発生し拡大した気泡が破泡し、その痕跡が金型面に押し付けられながら引き伸ばされたことで起こる。発生のメカニズムはシルバーストリークと同じであるが、多数の筋が一斉に発生する点が異なる。
4 射出発泡成形の製品設計
前述のように射出発泡成形品はソリッド成形品と比較すると強度や剛性が低くなる。そのままでは使用用途が限定されるために、それらの欠点を補うための設計が為される。
射出発泡成形品はソリッド成形品に比べると耐衝撃性が低くなるが、それを補うために裏面にリブを配置する方法がとられる。リブの厚みは天面の厚みと同等あるいは天面の厚みよりも厚めに設計するとよい。リブを太くしてもヒケが目立たない点が射出発泡成形の利点であり、リブを太くすることでリブがショートしにくくなるとともに充填圧力が下がるために製品重量も軽くなる。
射出発泡成形品はプラスチックと空気の複合材料であるので気泡が存在する分だけ弾性率が下がる。一方で製品剛性を高めるためにはリブ構造の他にコアバック法によって重量を変えずに製品厚みを増す手法が有効である。
5 コアバック法
射出発泡成形で高発泡倍率の製品を得る手法としてコアバック法が知られている。コアバック法は一度金型の空間(キャビティ)内を溶融プラスチックで満たした後にキャビティ容積を拡大させて発泡させる方法である(図4)。この方法では1.5~6.0倍程度の比較的高い発泡倍率が可能になる。コアバック法は自動車のドアトリム・ドアキャリア・エンジンカバー等の成形に用いられている。コアバックとは言うものの、金型のスライド移動によるキャビティ容積の拡大法(狭義のコアバック)や可動プラテンの移動によるキャビティ容積の拡大法が用いられる。
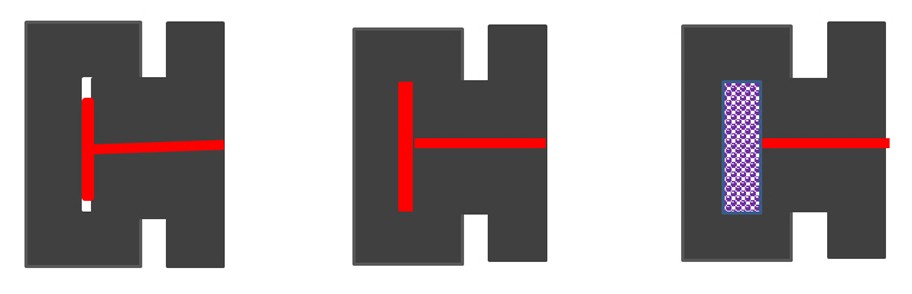
図4 コアバック発泡における金型動作の例
コアバック法はキャビティ容積の拡大動作を開始するタイミングが極めて重要である。金型内に充填された溶融プラスチックは金型に熱を奪われて金型に接触している部分から温度が下がっていく。厚みの中心部分は最も温度が高い。温度が下がり過ぎるとその部分はコアバックしても気泡が生成しないし、温度が高すぎる部分ではコアバックによって気泡が大きくなり過ぎて破泡や気泡の合一が起こる可能性がある。したがって射出充填完了からコアバック開始までの時間が長すぎるとコアバック動作に製品が追従せずに設計通りの製品厚みに仕上がらないし、コアバック開始までの時間が短すぎると板厚中心部が裂ける現象が起こる。中心部が裂けると設計通りの剛性が出なくなる。
コアバック開始のタイミングは、射出される溶融プラスチックの温度・金型の表面温度・成形材料の粘弾性特性・成形材料の結晶化特性等に依存するので製品ごとに最適な条件を探索する必要がある。
6 射出発泡成形品の外観品質向上技術
射出発泡成形品の表面に生じるスワールマークは製品外観を著しく損なうものであり外観部品への適用を妨げてきたが、その対策もいろいろなアプローチから為されてきた。スワールマークが見えない製品を得るには大きく3つのアプローチが為されている。気泡の破裂を防ぐ方法・スワールマークを転写によって消す方法・積層による方法である.
6.1 気泡を破裂させない方法
流動末端で気泡を破裂させない方法としては、材料からのアプローチと金型技術を含む成形加工法からのアプローチがある。
材料からのアプローチとしては、気泡壁の強度を高めることで破泡を防ぐ方法で高分子量成分の添加や長鎖分岐構造の導入による発泡に適した材料が市場投入されている。成形技術からのアプローチとしては、金型内を圧縮空気で加圧して破泡を防ぐガスカウンタープレッシャー法が検討されている。写真1の写真は2019年の名古屋プラスチック工業展に出店されたサンプルであり物理発泡成形とガスカウンタープレッシャーの併用効果が明らかに見られる。

写真1 ガスカウンタープレッシャーによるスワールマーク対策の例
左からソリッド,物理発泡,物理発泡+ガスカウンタープレッシャー名古屋プラスチック工業展2019 株式会社日本製鋼所ブース
6.2 スワールマークを転写させる方法
流動末端で破泡して生成した筋を金型転写することによって消す方法であり、金型技術からのアプローチと材料からのアプローチがある。金型からのアプローチとしては金型加熱冷却(ヒート&クール)や断熱金型の利用がある。材料からのアプローチとしては結晶化遅延の手法がある。
ヒート&クール法は成形サイクルの中で金型加熱と金型冷却を繰り返す方法であり、成形材料の荷重たわみ温度以上に加熱した状態で充填を行うと高度に金型転写される。射出発泡成形と組み合わせることで成形品表面のスワールマークを消すことが可能になる。ただし転写のために型内圧力を高めにする必要があり、気泡による空隙率が下がるため軽量化効果が小さくなる。
断熱金型は金型キャビティ面に熱伝導率が低い材料を配置することで溶融プラスチックが接触したときの急激な冷却を避けて転写のための時間を確保する方法であり、ヒート&クールと同様な効果が得られる。断熱金型も射出発泡成形と併用ができる。とくにテクスチャーを施したセラミックスを金型キャビティ内面に配置しておくとスワールマークが目立たずにテクスチャーが転写される。写真2の写真は2022年にドイツのデュッセルドルフで開催されたK2022に出品されたものである。
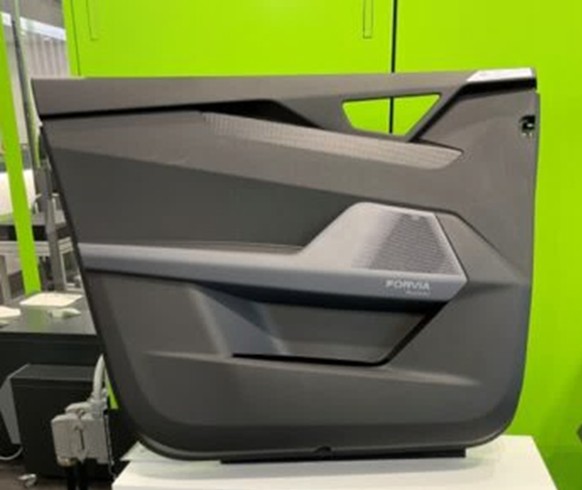
写真2 物理発泡と断熱金型を組み合わせた射出発泡成形品
K2022 ENGELブースの展示品
材料からのアプローチとしては結晶化を遅延させる手法がポリアミドとポリプロピレンで行われている。ポリアミドに結晶化遅延剤を添加することで温度が下がっても転写可能な時間を確保している。実際に自動車のエンジンカバー(無塗装)に採用されている。ポリプロピレンではメタロセン触媒を用いたコポリマーが結晶化遅延効果を持っており、物理発泡成形を行っても外観品質が高く自動車の部品に採用された例がある。
6.3 被覆する方法
射出発泡成形と同時にフィルムインサート成形を行うことでスワールマークが見えず、製品表面のヒケも見えないという組み合わせ技術も行われている。写真3の写真はK2019(2019年)のENGELブースで成形実演されていたサンプルである。
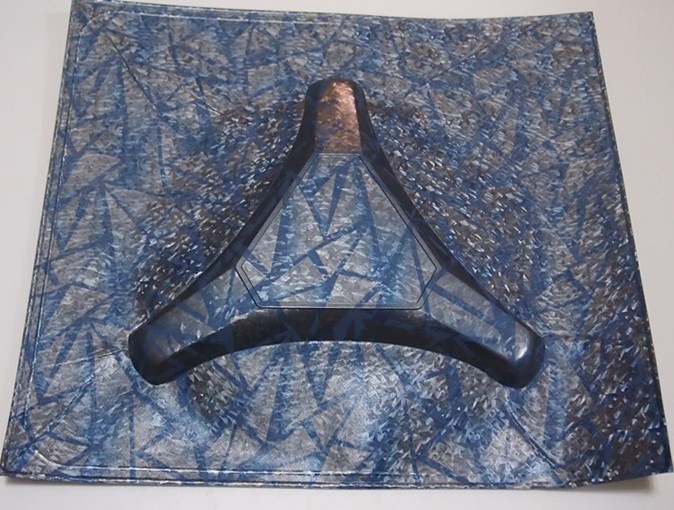
写真3 物理発泡成形とフィルムインサート成形の組み合わせ
K2019 ENGELブース
7 物理発泡技術の進展
物理発泡技術としては超臨界流体(窒素,二酸化炭素)を用いる微細発泡成形が用いられてきた。ショートショット法の用途が多かったが、近年では気泡径が均一で5倍以上の発泡倍率が得られるようになったことで、従来はプレス発泡成形で生産されていたスポーツシューズのミッドソールが射出発泡成形で生産されるようになってきた。閉じた金型に発泡した溶融樹脂を流す際に均一に気泡が拡大するように金型に多数設けられたベント穴から排気・減圧しながら賦形するようである。写真4の写真はIPF Japan 2023で成形実演されていたミッドソールの金型と製品(Woojin Plaimブース)である。射出発泡成形によるミッドソール成形は台湾の製靴産業で実際に行われている。
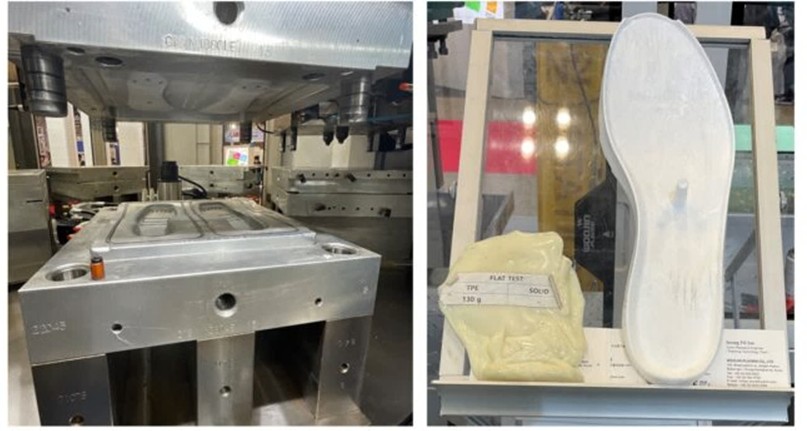
写真4 倍以上の高倍率発泡体成形プロセスの金型(左)と成形品(右)
IPF2023 Woojin Plaimブース
8 おわりに
射出発泡成形の技術動向を展示会情報も交えながら紹介したが、この誌面では紹介しきれない新しい技術も紹介されている。成形実演を実際に見る機会に足を運んでいただきたい。とくに3年に一度開催されるKショーでは毎回新技術が披露されている。
参考文献
1) 特開2006-328319
2) 特開平6-100722
3) 特開2004-300260