発泡成形に用いる発泡剤
秋元英郎
秋元技術士事務所
1.はじめに
本報では発泡成形に用いられる代表的な発泡剤である化学発泡剤、物理発泡剤、超臨界流体、熱膨張性マイクロカプセルについてそれぞれの特徴について解説した。
2.発泡成形とは
プラスチックの発泡成形とは、発泡性プラスチックを成形して多孔質プラスチックを得る技術である。発泡成形ではない一般的なプラスチック成形では、融かす工程、流す工程、固める工程から成り立っていることはよく知られているが、発泡成形ではそれらに加えて、発泡性を付与する工程と、気泡を発生させて成長させる工程、気泡の成長を停止させる工程(通常は固める工程によって気泡の成長が停止する)が追加される。
プラスチックに「発泡性」を付与するために用いられるのが発泡剤であり、発泡剤として何をどの程度の量用い、どのようにして供給するのかが非常に重要になってくる。その選択を間違えると期待した発泡体の構造(気泡の数、気泡の大きさ、気泡の構造)が得られない。
なお、発泡成形における気泡とは気体の塊を液体や固体でくるんだ状態である。気泡同士がつながってしる状態を連続気泡、つながっていない状態を独立気泡という。
工業的に用いられる発泡成形には溶解したガスから気泡を発生させる方法と分散させた発泡剤の熱分解や化学反応によって気泡を発生させる方法がある。
溶解させたガスから気泡を発生させる方法については、栓を抜いたときのビールで説明されることが多い。すなわち、圧力をかけて溶解させたガスを、栓を抜いて圧力解放することで泡を生じさせるものである。
分散させた発泡剤の熱分解によって気泡を発生させる方法は、食品で例示すると重曹やベーキングパウダー(ふくらし粉)を混ぜてケーキを焼くときがそのケースになる。ベーキングパウダーは重曹(炭酸水素ナトリウム)を主成分にして、酒石酸やクエン酸のような助剤が配合された薬剤である。重曹は加熱によって二酸化炭素を発生し、ベーキングパウダーは水が加わることで中和反応が起こって二酸化炭素が発生する。
3.発泡剤の種類と特徴
発泡剤は発泡成形において気泡を形成するためのガスを供給する物質であり、化学発泡剤と物理発泡剤に大別される。また、発泡性マイクロカプセルは物理発泡剤であるが、取り扱いが化学発泡剤に似ている。超臨界流体は物理発泡剤の一つの形態であるが、微細射出発泡成形を理解する上で極めて重要なため、分けて解説する。
4.化学発泡剤
化学発泡剤は有機系発泡剤と無期系発泡剤に分類され、それぞれは更に熱分解型と反応型に分類される。有機系の熱分解型発泡剤では、ADCA(アゾジカーボンアミド)、DPT(N,N’-ジニトロペンタメチレンテトラミン)、OBSH(4,4’-オキシビスベンゼンスルホニルヒドラジド)等が良く用いられる。無機系の熱分解型発泡剤には炭酸水素塩、炭酸塩、炭酸水素塩と有機酸塩の組合せなどがある。射出発泡成形では重曹(炭酸水素ナトリウム)系発泡剤が好んで用いられる。
炭酸水素ナトリウムの分解反応(二酸化炭素発生)において、分解物である水の存在が分解速度に影響することがわかっており、分解温度を下げる傾向にあるため、発泡剤を吸湿させないような注意が必要である1)。
4-1 化学発泡剤の代表的な特性
熱分解型化学発泡剤の性能を決定するのは、分解温度,ガス発生量,粒子径である。
分解温度
化学発泡剤が熱分解する温度のことである。特に有機系化学発泡剤は分解速度が速いため、成形温度とのマッチングが悪いと良好な発泡体が得られない。分解温度の測定は顕微鏡で観察しながら一定速度で温度上昇し、目視で分解が確認されたときの温度とすることが多い。
ガス発生量
化学発泡剤が分解する際に発生するガスの体積である。このガスが気泡内のガスになるため、発泡倍率に影響する。熱分解させて発生させたガスを水上置換で集めて体積を測定する。
粒子径
化学発泡剤は通常は粉末であり、粒子径が小さいほど単位重量当たりの粒子数が多くなる。粒子数が多いほど発生気泡数が多くなる可能性がある。
分解温度と成形温度とのマッチング
発泡成形において、成形温度が高いと樹脂粘度は低く、成形温度が低いと樹脂粘度は高い。発泡成形には最適な樹脂粘度の範囲がある。その粘度範囲にあるときに発泡剤が分解するように発泡剤を選択する。樹脂粘度が低いときに発泡剤が分解すると、気泡壁が破れて粗大気泡を生じ、製品表面からのガス抜けも起こる。樹脂粘度が高いときに発泡剤が分解すると、気泡の拡大が阻害され、発泡倍率が十分に上がらない。
4-2 代表的な化学発泡剤の種類と特徴
表1、表2には代表的な化学発泡剤の特徴を、図1にそれらの熱分解特性を示した。図中に示した矢印は標準タイプの熱分解挙動である。
表1 代表的な化学発泡剤の構造
表2 代表的な熱分解型化学発泡剤の性状と性能
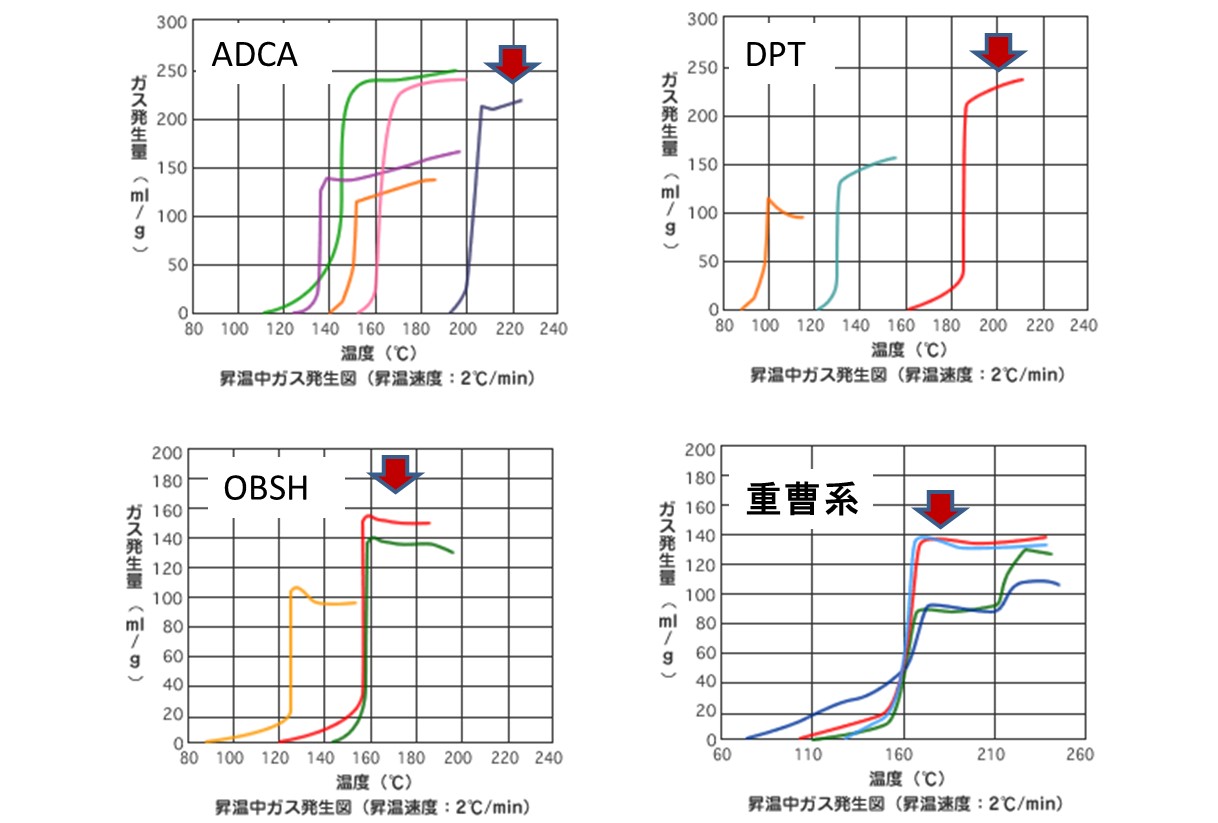
図1. 代表的な化学発泡剤の熱分解挙動
(永和化成工業㈱のホームページより引用 ただし矢印は標準品を示すために著者が加筆した)
ADCA系: http://www.eiwa-chem.co.jp/product/vinyfor.html
DPT系: http://www.eiwa-chem.co.jp/product/cellular.html
OBSH系: http://www.eiwa-chem.co.jp/product/neocellborn.html
重曹系: http://www.eiwa-chem.co.jp/product/cellborn.html
化学発泡剤はクエン酸塩や酸化亜鉛と併用することで気泡径を小さくすることが可能である。例えば、有機系であるOBSHにクエン酸塩と酸化亜鉛を併用する例が特許文献に示されている2)。無機系化学発泡剤と高級脂肪酸塩の併用も気泡の結合・合一を防いで気泡を微細化する効果があり、特許文献では重曹,クエン酸塩,タルク(発泡核剤)にステアリン酸リチウムを併用する配合処方が示されている3)。
重曹系、重曹+クエン酸塩系発泡剤は、無味無臭で分解残渣が無毒であるため、食品包装用途向けの押出発泡製品や自動車の内装材用途の射出発泡製品に多く使用されている。分解温度が140~160℃付近であるため、ポリプロピレンの成形温度より50~70℃低く、ちょうど使いやすい。発泡剤そのものは粉末であるが、ポリエチレン等のプラスチックに20~40%程度の濃度で混ぜたマスターバッチとして使用されることも多い。
5.物理発泡剤
物理発泡は、高圧下でプラスチックにガスや超臨界流体を溶解させ、圧力低下あるいは加熱によって溶解度を低下させることによって気泡を生成させる発泡方法である(溶解度は圧力が高いほど、温度が低いほど高くなる)。
液化ガスとして代表的なものにフロンと炭化水素がある。これらはプラスチックに対する溶解度が非常に高いため、押出発泡で高発泡倍率を得る目的で使用されている。また、フロンは熱伝導率が低く、気泡壁を透過しにくいため、断熱材用途で多く使用されている。
これらの物理発泡剤はオゾン層破壊、地球温暖化、可燃性・毒性の問題もあり、無害な窒素,二酸化炭素への代替が検討されているが、プラスチックに対する溶解度が低いため、高倍率の発泡体を得るためのもう一工夫が求められる。窒素の溶解度は更に小さい。図2にポリスチレンに対する主要な物理発泡剤の飽和溶解度曲線4)を示した。
物理発泡剤は供給する圧力が高い方が、溶解量が多くなる。図3にベント式射出成形機のベント口から加圧した二酸化炭素を供給して溶解させたときの二酸化炭素供給圧力と溶解した二酸化炭素の量の関係を示した。供給圧力と溶解量はほぼ比例し、ヘンリーの法則が成立している5)。
図4には図3と同じ特許文献に記載されている図であり、二酸化炭素の溶解量の圧力依存性がプラスチックの種類によって異なり、大きく2つのグループに分かれることを示している5)。
溶融したプラスチックにガスが溶解する際には、ポリマー分子が引き合う力に逆らって引き離す必要がある。そのため、ポリマー同士が引き合う力が強い極性ポリマーでは溶解度は小さく、引き合う力が小さいポリオレフィンは溶解度が大きくなる傾向にある。
6.超臨界流体
液体は分子間の距離が近く、分子の運動速度が小さい。気体は分子間の距離が離れていて、分子の運動速度が大きい。
液体の温度を上昇させていくと分子運動が盛んになり、気体の圧力を上昇させると分子間距離が近くなる。高温高圧の条件にすると、分子間距離が近く、分子運動が速い状態にたどり着き、もはや液体と気体の区別がつかなくなる。
この液体と気体の両方の性質を併せ持った状態を超臨界状態と呼び、その物体を超臨界流体と呼ぶ(図5)。また、このような状態が得られる温度,圧力をそれぞれ臨界温度(Tc),臨界圧力(Pc)と呼び、図6に示すように臨界温度・臨界温度以上の領域が超臨界流体である。ただし、液体と超臨界流体との間あるいは気体と超臨界流体の間には相変化は無く、連続的に変化する。
発泡成形の発泡剤として用いられる超臨界流体は窒素と二酸化炭素であり臨界温度,臨界圧力は窒素:Tc=126 K(-147.0 ℃),Pc=3.39 MPa,二酸化炭素:Tc=304.2 K(31.1℃),Pc=7.37 MPa である。図3のグラフでは、二酸化炭素の臨界圧力(7.38 MPa)を挟んで溶解性に大きな変化は無く、溶解度は圧力に比例していることから、超臨界流体になると急激に溶解性が高くなるということはない。
発泡剤である窒素や二酸化炭素が溶融したプラスチック溶解した後は、例え圧力・温度ともに上記臨界圧力、臨界温度以上になっても、溶解した発泡剤は超臨界状態とはいわない。プラスチックに溶解した二酸化炭素や窒素の分子は、気体並みの速さで分子運動するわけではない。
超臨界流体を発泡剤として用いる利点の一つは注入量が正確に制御できる点にある。超臨界流体を用いるもうひとつの利点は、圧力が高いことにより大量の発泡剤を溶融樹脂に溶解させることができることである。
超臨界流体は微細発泡を得るための発泡剤としてよく知られている。超臨界二酸化炭素等を高圧下でプラスチックの相に導入・飽和溶解し、常圧に減圧することで無数の微細気泡を材料全体に発生させることができる。参考文献6の例では気泡径はおよそ2μm以下になる6)。
7.熱膨張性マイクロカプセル
熱膨張性マイクロカプセルは炭化水素をガスバリア性プラスチックのカプセルでくるんだものであり、温度が高くなるとカプセルが軟化するとともに炭化水素が気化して気泡を生じる(図7)。カプセルは保管時にガスが抜けないようにポリアクリロニトリル等が用いられる。熱膨張性マイクロカプセルは、カプセルが破裂しない限り成形品の表面にシルバーストリーク,スワールマークが発生せず、良外観が得られるという特長がある。
マイクロカプセルタイプの発泡剤の特性評価には一般的にTMA(熱機械分析)を用いた昇温による体積変化のグラフが用いられる(図8)。温度上昇とともに体積は膨張するが、ある温度を境に収縮する。これは、高温域でカプセルが破れるためである。

図8 膨張性マイクロカプセルの膨張特性
積水化学ホームページ( http://www.sekisui.co.jp/cs/product/type/advancell/em/index.html )より引用
マイクロカプセルの膨張特性は中の揮発成分の種類とカプセルの物性に依存しており、グレードによって膨張開始温度、膨張ピーク温度が異なるバリエーションがある。とくにカプセル材の粘弾性挙動が発泡剤としての特徴を決定している。
カプセル材の架橋度を最適化することで発泡倍率と製品外観を両立させることができる7)。すなわち、架橋が十分でないとカプセルが容易に破裂し、架橋が過剰だと十分に膨らまない。
熱分解性マイクロカプセルの例としては、積水化学工業(株)のアドバンセルEMシリーズ、AkzoNovelのExpancell DU, WU, MB, SL, FGシリーズ(日本国内では日本フィライト(株)が販売)、松本油脂製薬(株)のマツモトマイクロスフェアー F, FNシリーズ、(株)クレハのクレハマイクロスフェアーが商品として販売されている。
参考文献
1) Yamada Shuto, Koga Nobuyuki, Thermochem Acta, 431 (1-2), 38-43 (2005)
2) 松野耕二,大村直久,特開2000-264993 (2000)
3) 都築佳彦,大村直久,樋口諭,特開2004-323726 (2004)
4)滝嶌,“発泡成形”,情報機構,103 (2008)
5) 山木宏,WO01/096084 (2001)
6) Sung W. Cha, Nam P. Suh, Daniel F. Baldwin, Chul B. Park, US Patent 5158986 (1992)
7) Kawaguchi Yasuhiro, Ito Daichi, Kosaka Yoshiyuki, Okudo Masazumi, Nakachi Takeshi, Polym. Eng. Sci, 50 (4), 835-842 (2010)