初学者のための射出成形機の構造・機構入門
酒井忠基
静岡大学客員教授
本技術レポートは、日本工業大学工業技術博物館の工業技術博物館ニュース第98号(2017年11月発行)に寄稿した「プラスチック射出成形技術の歴史」をプラスチックス・ジャパン・ドットコムの読者向けに書き直したものである。
1.はじめに
プラスチックの射出成形は複雑な形状の製品を高速で大量に生産できる優れた製造方法である。射出成形の工程は大きく分けると融かして・流して・固める工程になる。射出成形には、射出成形機と金型が必要になるが、射出成形機の役割は、①成形材料を融かす、②融けた成形材料を流す、③流して固めるための金型を開閉することにある。
したがって、射出成形機は融かして流すための射出ユニットと金型を取り付けて金型を開閉するための型締めユニットから構成される。さらにはそれらのユニットを駆動させるための機構を備えている。
本稿では、射出成形機の進化の歴史を交えながら、装置の構造・機構を解説する。
2.射出ユニット(プランジャー式射出成形機からスクリュ式射出成形機へ)
2-1 プランジャー式射出成形機
シリンダー内を往復して、流体を圧送する円筒形のものである。プランジャー式射出成形機は熱可塑性樹脂をシリンダーの内部で溶融させ、プランジャーを用いて金型の空間に流し込む装置である。
1872年には米国のJ.W,Hyattがセルロイドの加工用にプランジャー式射出成形機を開発しているが、実用的な射出成形機はその後1926年にエッケルト・ツィーグラー(独)や1931年にHPM(米)が開発し、さらにフラツ・ブラウン(独)も1933年に本格的な横型のプランジャー式射出成形機ISOMAを市販している1),2)。
図1はK-Showに出展された初期の手動式射出成形機である。(製造元:未詳) 図2はHyattが開発した初期のプランジャー式射出成形機の構成と一般的なプランジャー式射出成形機を示す。
ドイツで開発された射出成形機ISOMAは戦時下の1943年にポリスチレン製レーダー部品の製造研究のために潜水艦U-ボートで輸入された。現在、この装置は旭化成(川崎)に展示され、成形に使われた金型は積水化学工業(京都)に展示されている。
このISOMA射出成形機と金型は戦後の日本のプラスチック射出成形技術発展の基盤となっており、2014年にどちらも化学遺産として認定・登録された3)。この射出成形機と金型を図3に示す。
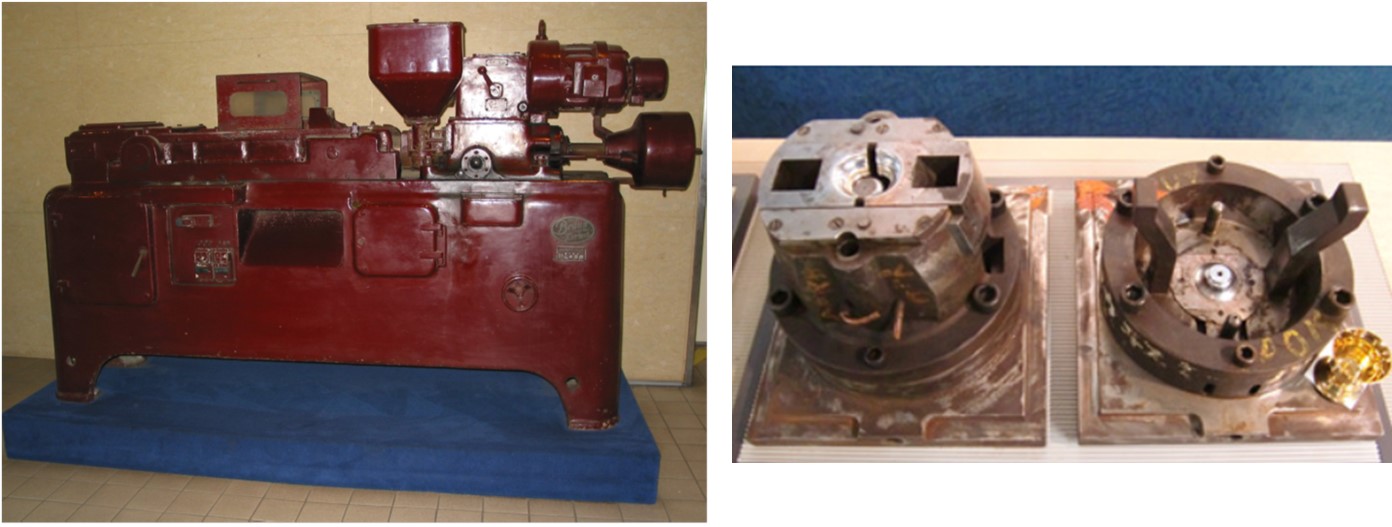
図3 ドイツで実用化されたISOMA射出成形機と金型(認定化学遺産2014年)
日本初の手動のプランジャー式射出成形機は名機製作所が1942年に開発しているが、同社は1947年にはこのISOMA射出成形機をモデルにした全自動電動機械式射出成形機を国産化している。
2-2 スクリュー式射出成形機
一方、1943年になると、ドイツのH.Beckが最初のスクリュ式射出成形機を開発するが、しばらくの間、その実用化は進んでいない4)。
スクリュー式射出成形機は、シリンダーの内部で熱可塑性樹脂を効率的に溶融させるためにスクリュー(ねじ)を用いる装置である。
その後、ドイツではA.G.Goller(アンケルベルク)がエックヘルト-ツィーグラーやライヘンホイザーと協力して最初のスクリュ式射出成形機を実用化した5)。この装置は1957年にハノーバーメッセ,さらに1959年にデュッセルドルフのK-Showに出展されて注目を浴びた。現在、この装置はミュンヘンのドイツ科学博物館で展示されているとのことである。
一方、米国でも1946年にJ.W.Hendryがスクリュ式射出成形機を開発しているとされているが、1952年にはスクリュ式射出成形機がW,Willert(イーガン)によって実用化されている6)。米国のWillertの開発したスクリュ式射出成形機を図4に示す。
2-3 スクリュー式射出成形機の優位性
プランジャー式射出成形機の課題は、プランジャーの作用で溶融樹脂を流すことができる状態にするまでに時間がかかる点にあった。すなわち、溶融させるために必要な熱がシリンダー内面からのみで効率が低く、熱を均一にできない等の問題点が有った。
スクリュ式射出成形機はプランジャー式射出成形機に比べて、生産性が高く、混練や成形工程の制御も優れており、瞬く間に世界の射出成形機がスクリュ式射出成形機に変わったといわれている。
プランジャー式射出成形機とスクリュ式射出成形機との生産性の相違を図5に示す7)。
生産性の向上以外に、当時急速に伸長していた硬質塩化ビニールの成形はスクリュ式射出成形機でないと不可能であったことも影響している。
当時の日本では既にプランジャー式射出成形機の生産を始めていたが、スクリュ式射出成形機が発表されると、日本製鋼所は1961年にアンケルベルク(西ドイツ)からこのスクリュ式射出成形機の技術を導入して,日本で初めて射出成形機(トグル式型締力30-350トン)の生産に入った7)。この射出成形機を図6に示す。
さらに、60年代には、東芝機械バッテンフェルト(独),住友重機械工業がネスタール(スイス),三菱重工業がナトコ(米),新潟鉄工スチューべ(独),川口鉄工がチャーチル(英)、石川播磨重工がHPM(米)、池貝鉄工がウィンザー(英)などと相次いで技術提携を行い,急速にスクリュ式の射出成形機が普及した。
一方で、1本のスクリューが熱可塑性樹脂の可塑化と射出用のピストンの両方を担うために、成形が不安定になるという問題も存在した。そのため、可塑化と射出の役割を分けた、スクリュープリプランジャー方式の射出成形機も開発され、実用化されている。
2-4 シンリンダー用高品質材の登場
これらの技術進歩と並行して、射出成形機および押出成形機の耐食耐摩用シリンダとして広く用いられているバイメタル構造のシリンダが1938年にX-アロイ(米)で開発され8)、1961年には日本製鋼所がこの遠心鋳造技術を提携して押出成形機や射出成形機に展開している。
ただし、1980年代頃まで射出成形機のシリンダは内面を窒化処理することが主流であったが、現在はNi合金やWCを分散させた耐食耐摩処理などが広く使われている9)。
3.型締め機構(トグル方式型締めと直圧方式型締め)
射出成形機の型締め機構に関しては、図7に示すように、直圧方式とトグル方式とがあり、それぞれの特徴を有している。
直圧方式では射出成形圧力を直接受けるが、型締め位置の調整は油圧シリンダを移動すれば容易に可能である。一方、トグル方式の型締め装置ではトグルアームを開いた状態で射出成形圧力を受けても大きな油圧力を必要とせずに強い型締め力が発揮できる利点がある。しかし、型締め位置の調整はトグル全体を移動させなければならない。
この両方式のどちらかを採用するかはそれぞれの射出成形機メーカーによって異なっている。射出成形機の型締め機構に関しては、1941年に公開されたエックヘルト&ツィグラー(独)の特許などがある。図8に初期の型締め機構を示す10)。
4.射出と型締めのレイアウト(横型射出成形機と竪型射出成形機)
一般のプラスチック射出成形機では射出成形ユニットと型締めユニットを水平に組み合わせた横型と呼ばれる構造が多く用いられている、図9に示すように、型締め部位を垂直に設置した竪型射出成形機と呼ぶ構造も用途に応じて活用される。
両方式とも、1930年代の熱硬化性プラスチックの射出成形を行った初期の時代から使用されているが、一般には、横型射出成形機構造が主流となってきた11)。
竪型射出成形機構造はロボットなどを用いた自動化が容易であり、ロータリテーブルやシャトルテーブルなどを組み合わせて、金属部品などのインサート成形やICなど電子部品のフープ成形に対して活用されている12)。
現在は、インサート部品を多用するシリコーンゴムの射出成形や炭素繊維強化プラスチックの成形加工などに竪型射出成形機を用いる技術が進展している13)。
また、型締めは竪型(上下に開閉)で射出ユニットは水平(横型)の成形機も存在する。
5. 駆動方式(油圧駆動方式から電動駆動方式へ)
1920年代にプラスチック射出成形機が実用化された頃、バッテンフェルド(独)が早くも電動駆動方式の射出成形機を開発したが、普及せず、その後は油圧方式に変わっている。
1950年代になると油圧駆動のアクチュエータがスクリュ式射出成形機に導入され,生産性が飛躍的に改善された。
1970年代には、マイクロプロセッサによる制御技術が開発され,各種の設定がディジタル化されて,射出成形機の制御性が大幅に改善した。さらに,射出成形圧力の閉ループ制御や温度のPID制御を駆使してより安定した高精度成形が可能になった。
これらの技術進歩の結果、油圧駆動方式射出成形機は型締め力5あるいは10トン規模の超小型射出成形機から型締め力6000トン規模の超大型射出成形機(1977年HPMが3000トン射出成形機、1992年日本製鋼所が6000トン射出成形機を製造、全長30m)に至る各種の射出成形機が製造されるようになった14)。
図10は6000トンの型締め力を有する超大型射出成形機で成形したプラスチック射出成形品の一例である。
一方、油圧式射出成形機では,作動油の粘度が温度に依存することや制御弁の動作特性の安定性、さらに省エネルギーへの対応不足が課題となり、そこで、我が国では電動式射出成形機が再び注目されるようになった15)。このため、1980年代になると、射出成形機の駆動方式として電動駆動システムが再び登場してきた。図11には油圧駆動方式と電動駆動方式射出成形機の構成を比較して示す。
1983年最初に電動射出成形機を開発したのは日精樹脂工業であった。図12にこの射出成形機の構成を示す16)。この装置は一台のサーボモータで射出、可塑化、型開閉のサイクルを行う機構のため、成形サイクル時間が長く、生産性がよくなかった。
その後、1985年のNPE(米)にはファナック(日)とミラクロン(米)が電動式射出成形機を展示して注目された。この頃になると、射出成形メーカー他社も競ってこの方式の射出成形機を実用化している。
現在の電動駆動方式射出成形機ではハイサイクル成形に対応するため,型開閉,製品突出し,射出,可塑化を独立した4つのサーボモータで駆動する機構が一般的であり、高精度化および成形能力の高度化に対応するためにクローズドループの射出圧力制御を導入している15),17)。
電動駆動方式射出成形機の特徴のひとつは省エネルギー対応である。図13に両方式射出成形機の省エネルギー化・省資源化への対応を比較したものである18)。電動駆動方式の方が省エネルギー化、冷却水量の低減化が達成されていることが分かる。
電動駆動方式の射出成形機の有する省エネ効果および制御性能向上などが注目を集め、僅かの期間に電動駆動方式が日本の射出成形機の主流を占めるようになった。この状態を図14に示した。
電動駆動方式射出成形機は主に中小型規模の装置に用いられているが、分野によっては型締め力3000トン超の大型射出成形機にも適用されるようになった。(宇部興産機械、日本製鋼所など) 機械全長20mに及ぶ大型電動駆動方式射出成形機の外観を図15に示す19)。
さらに、現在はその両方式の利点を組み合わせた油圧・電動兼用のハイブリッド駆動方式も出現するようになっている20)。(日精樹脂工業、ミラクロンなど)
参考文献
1) US-Patent 2057945, DE 624069, Franz-Braun (1936) 射出成形機
2) Modern Plastics, January p82 (2000)
3) 田島、化学と工業, 67(7), p596 (2014) 射出成形の源流
4) DE-Patent 858310C, BASF(1943)screw injection machine
5) A.G.Goller, Kunststoffe, 49(10), p531 (1959) screw-injection molding machine
6) US-Patent 2734226, Egan (1956) Willert screw injection molding machine.
7) 酒井、日本製鋼所技報, 54(8), p20 (1998) プラスチック成形加工技術の歴史
8) US Patent 2111278A, Eaton (1937) bimetallic cylinder
9) H. Ohyabu, K. Chikara, T. Chimura, T. Sakai, Int. Plas. Eng. Techn., 3, p25 (1997)
10)1) US Patent 2233354, Eckhert&Zigler (独) (1941) トグル式型締め機構
11) US Patent 2318031A, Hydraulic Device (1943) 竪型
12) 酒井、高分子, 39(6), p420 (1990) 複合成形
13) T. Sakai, Adv. Polym. Techn., 12(1), p61 (1993)
14) 酒井、日本製鋼所技報, 54(8), p20 (1998)
15) 稲葉、精密工学会誌, 66(10), p1528 (2000) 電動射出成形機
16) US Patent 4540359, 日精樹脂工業 (1985) 電動射出成形機
17) US Patent 5,804,224, ファナック (1998) 電動射出成形機
18) T.Sakai, Int. Polym. Proc. 16 (1) p3 (2001)
19) 第4回新機械技術振興賞受賞 三菱重工プラスチックテクノロジー (2006)
20) M.Knights, Plastics Technology, 5(1) (2006), Hydraulic. Electric, Hybrid