最新の金属と樹脂の接合・接着技術
安田ポリマーリサーチ
1.はじめに
最近、地球環境問題・資源問題等から従来型の内燃機関車から電気自動車への電動化が急加速している。電動化の際、新たに導入される部品には、代表的なものとして動力源である二次電池(電気二重層キャパシター)、モーター、インバータおよびPCU (Power Control Unit)等である。その他の部品としては写真1のPTC (Positive Temperature Coefficient)ヒーターも必要になる。
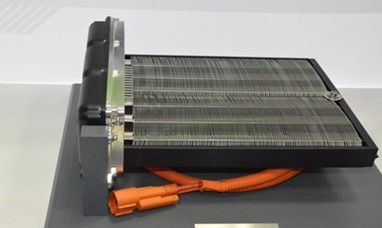
写真1 PTCヒーター(ボルグワーナー)
内燃機関車ではエンジン冷却水の熱で暖房を行うが、EVはその熱源がないためPTCヒーターが必要になる。熱源となるエンジンが存在しないEVにヒーターを搭載するため、動力源の電池を消耗するため、これらの作動で航続距離が短くなる。また、インバータから発生するノイズ対策のため、写真2の高周波ノイズ用吸音材を設置する必要がある。
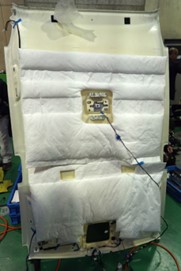
写真2 高周波ノイズ用吸音材
また、最近話題となっている自動運転を行うためには、新たな電子部品を搭載することが必要となる。これら全ては自動車の総重量を増加させる要因となる。従って、電動化、自動運転を推進すると、今まで以上に軽量化の要請は高まってくる。
対策には、低比重であるプラスチック、軽金属の採用の増加、超高強度鋼板の積極的な採用などが挙げられる。最近、異種材料の接合によるマルチマテリアル化による軽量化がその対策の一つとして注目されている。
接合はプラスチック部品を別個に成形し、組み立てる際に使用される。その手段には、種々あるが、最近重要になっている金属とプラスチックの接合を中心に紹介する。最近、自動車では、軽量化のための一つの手段として金属のプラスチック化が進捗している。そのため、金属とプラスチックが共存して使用される機会が増加しており、プラスチックと金属の接合は重要性を増している。
2.樹脂と金属の接合(接着剤レス)技術開発状況
表1、2、3に樹脂と金属の接合(接着剤レス)技術開発状況を示す。
表1 樹脂と金属の接合(接着剤レス)技術開発状況-その1 化学処理-
表2 樹脂と金属の接合(接着剤レス)技術開発状況-その2 レーザー処理等-
表3 樹脂と金属の接合(接着剤レス)技術開発状況-その3 レーザー処理等-
3.樹脂と金属の接合(接着剤レス)技術の各論
3-1 NMT(Nano Molding Technology)(大成プラス)
① NMTの特徴
・金属と樹脂の射出成形による一体成形技術
金属への表面処理によりナノレベルのディンプルを金属表面に形成する。これら微細なディンプルに射出成形し、硬質樹脂を入れ込むことで、金属と樹脂を一体化する画期的な技術である。製品の筐体やボディーなど金属外装部品の軽量化 を実現する新製品の開発が可能になる。
・接合可能な金属と樹脂
アルミニウム・マグネシウム・銅・ステンレス・チタン・鉄・アルミニウムめっき鋼板・黄銅が接合する。アルミニウムでは、1,000系〜7,000系などの合金に適応する。
射出成形により接合可能な樹脂は、PPS、PBT及びPA6・PA66、PPAとなる。特にPPSでは、強固な接合(せん断強度=40MPa以上)が実現する。
・環境負荷の軽減を実現
NMTはすべての工程がシンプルとなり、工程の短縮化が図れる。さらにマグネシウム合金成形技術のように表面の化成処理などが不要のため、コスト削減にも貢献する。
② NMTの信頼性
NMTの最大の魅力は、高い接合強度である。高い接合強度を実現できるからこそ、高い信頼性を生み、次世代に向けた、さまざまな可能性を拡げる。
・ NMT成形品の接合強度データ(使用樹脂:PPS)(表4)
表4 大成プラス㈱のHP記載の接合強度データ
写真3、4に代表的なNMTによる接合例を示す。
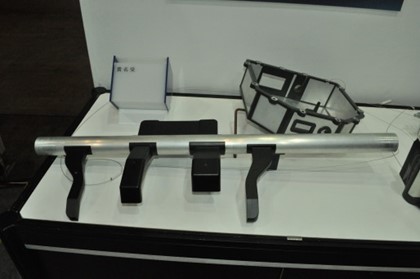
写真3 NMTによる接合例(大成プラス)
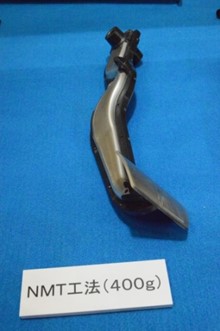
写真4 NMTによるアルミ/PPS接合によるブレーキペダル試作品(大成プラス)
3-2 DLAMP(ダイセルポリマー)
金属の表面にレーザー照射による特殊形状を形成し、これを金型内に配置して熱可塑性樹脂を射出成形(インサート成形)することで接合する技術である。これにより、特殊形状内部に樹脂が入り込みステッチアンカーと呼ぶ樹脂部分を形成するため、金属と樹脂を高い強度で接合する。
この技術は、様々な金属部材に適用可能で、金属に近い線膨張係数を持つ長繊維強化樹脂と組み合わせることで、より高い接合強度と、耐久性に優れた接合が可能となる。
① DLAMPの特徴
- レーザーの処理条件で、様々な金属へ適応可能。 (アルミ、ADC12、SUS、Mg、SPCC)
- 部分処理(片面処理、パターニング)が可能。
- ランニングコストが安価(電気代のみ)。
- 廃液や端材などの廃棄物は発生しない。
② 接合メカニズム
- レーザーで形成した空隙に侵入した樹脂が、ステッチアンカー(縫いこみ構造)を形成し、高い接合強度が得られる。
独自開発の低線膨張樹脂は樹脂の収縮を抑え、環境変化においても強度を維持する。
同社では、次世代の金属代替材料として期待されている長繊維強化樹脂「プラストロン」を展開しているが、この「DLAMP」を組み合わせることで、これまで樹脂単体では困難であった金属部品の樹脂化が可能となる。自動車分野においては、軽量化や燃費改善、二酸化炭素の排出削減に、応用展開を進めていく予定である。
写真5にDLAMPによる接合例を示す。
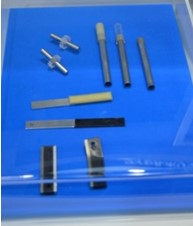
写真5 DLAMPによる接合例
3-3 AMALPHA(アマルファ,メック)
AMALPHA/アマルファは樹脂と金属を直接接合させるための当社独自の金属表面処理技術である。樹脂と金属を界面レベルで接合させ、樹脂・金属一体成形部品を作り上げる。
インサート射出成形・トランスファモールド成形・ヒートプレスなど幅広い成形技術に対応している。
① 樹脂と金属の直接接合
アマルファ処理は化学エッチングにより金属表面にミクロンサイズの微細な凹凸を形成する技術である。この凹凸に樹脂が入り込んで固まることで、アンカー効果による強固な接合が実現する。
- AMALPHAの接合のしくみ
② アマルファが創りだす 新しい機能部品
樹脂と金属が界面レベルで接合することにより、金属と樹脂のそれぞれの特徴を最大限に引き出した今までにない新しい設計・機能の部品を作ることができるようになる。
- 軽量:強度が必要な部分を金属に、それ以外を樹脂にすることで部品を軽量化する。
- 気密性・水密性:樹脂と金属が完全に密着し、ガスや液体を通過しなくなる。
- 部品点数の削減:ネジなどで締結されている部品を一体成形で一つの部品にまとめ、組み立て工数を削減する。
- 高い耐久性をもった接合:接着剤を使わないため、耐久性に優れる。また、樹脂や金属といった母材と同じ接合寿命を得られる。
③ アマルファの特徴
- 強い接合強度:母材破壊レベルの強度で樹脂と金属が接合する。
- 高い封止性:樹脂・金属界面は完全に密着しており、気体・液体を通過させない。
- 高い耐久性:接着剤などの耐久性の低い部材が介在していないため、樹脂もしくは金属の限界まで接合が劣化しない。
- 長いシェルフライフ:マルファ処理をしてから樹脂を接合するまでの時間が長い。
- 多種の樹脂・金属の組み合わせで接合が可能:物理的な接合のため、樹脂・金属の相性に左右されない接合が可能である。
- 処理表面の品質管理が可能: エッチング量、などで処理表面の状態を数値管理することが可能である。
表5にアマルファの樹脂・金属接合マトリクスを示す。
表5 アマルファの樹脂・金属接合マトリクス
◎ : 射出成形で接合 ⇒ 樹脂破壊 ○ : 熱圧着で接合 ⇒ 樹脂破壊 △ : 射出成形または熱圧着で接合 ⇒ 樹脂破壊せず。1MPa以上の接合強度 ― : 評価データなし
このデータにはユーザーでの評価結果も含まれている。
写真6,7にアマルファでの接合例を示す。
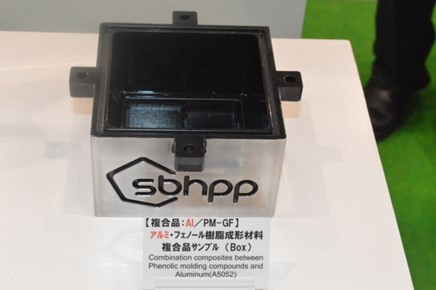
写真6 電磁波シールド付ECUボックス(Al/フェノール樹脂)
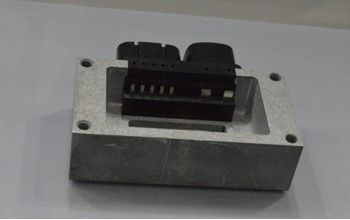
写真7 ECUボックス (Al/PPS)
4.最近の展示会のトピックス
最近の展示会で目に付いた接合関連の話題について紹介する。
4-1 リチウムイオン電池の電極版と封口板の異種材接合(メック)
写真8にリチウムイオン電池の電極・封口板の接合を示す。金属はふたがAl、電極がアルミニウム・銅で樹脂はPPSである。樹脂・金属の直接接合により封口板と電極を一体化し、缶型LiBの薄型化・耐久性向上・部品点数削減・コストダウンを実現させたという。
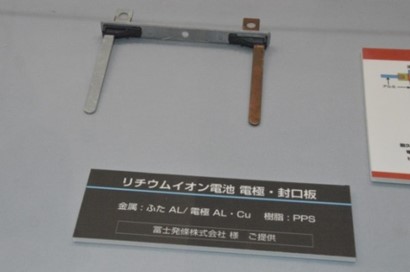
写真8 リチウムイオン電池の電極板と封口板の異種材接合
4-2 異種材接合を使用したブレーキペダル(エフテック)
写真9に異種接合により作成したブレーキペダルを示す。エフテックは、金属(Al)とヒート&クールCFRTP(PA) プレス成形と射出成形による異種接合により、製作している。
接合技術については触れていないが、説明員が以前本検討を大成プレスと行っていたとの発言があり、薬液処理により表面にナノレベルのディンプルを金属表面に形成させる方法がとられた可能性が強い。
このブレーキペダルは、正式には採用されていないが、強度試験で等は良好な結果が得られたと言っていた。
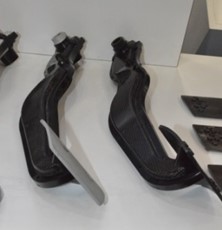
写真9 異種接合により製作したブレーキペダル
4-3 異種材接合によるフロントエンドモジュール (ダイセルエボニック)
写真10にフロントエンドモジュールを示す。脱脂処理した金属(Alなど)に特殊な接着剤の架橋型PAを塗装し、他の樹脂材料(GF強化PA6、PA66、PPA、PPなど)をオーバーモールドして作成する。
製品の特長は以下の通りである。
- 金属/樹脂から成る複合部品にPA系接着剤を使用することにより大幅な強度アップ
- 材料使用量を25%以上低減可能で軽量化。
- 複合部品の反りの低減が可能。
- 複合部品による収縮率の相違による接着力の低下という欠点を補える。
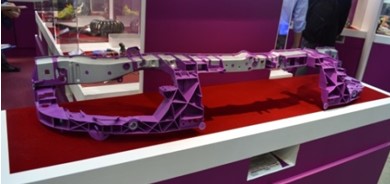
写真10 接合によるフロントエンドモジュール
4-4 プラスチック/金属複合部品(エルリングクリンガー・マルサン)
写真11にプラスチック/金属複合部品を示す。同社の金属とプラスチックの複合部品の“Hydro-Forming Hybrid parts”である。Alや鉄のパイプと熱可塑性樹脂との複合製品で、鉄やAlの溶接部品やAlやMgのダイキャスト製品の代替品として開発中である。
この部品は、金属のパイプを金型にインサートし、熱可塑性樹脂を射出成形して得る。金属と熱可塑性樹脂の接合技術はこの成形法の最も重要なキィポイントであるが、詳細は不明。応用例として、クロスカービーム、フロントキャリアーなどを展示していた。使用する樹脂は(GF強化)PPである。
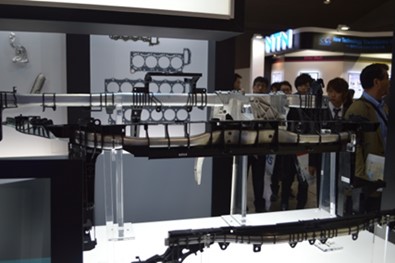
写真11 プラスチック/金属複合部品
4-5 異種材接着エアダクト(東洋紡)
写真12に異種材接着エアダクトを示す。PBTと耐熱性TPCを接着した成形品である。この二つの材料は相溶性が良いため、接着性も良好である。
このダクトの成形法の詳細は不明であるが、成形時に材料の組成を変えていくイクスチェンジブロー成形か両者を別個に成形したか分からぬが、いずれにせよ両者の良接着性を利用して接合した例である。
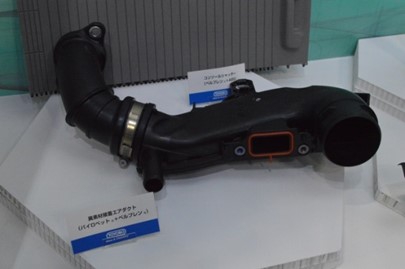
写真12 異種材接着エアダクト
4-6 構造用接着剤を使用した接合
写真13は構造用接着剤が適用された部位の例を示す。日本は、自動車分野における構造用接着剤の適用が欧州に比べてはるかに少ない。
日本での構造用接着剤の使用箇所は多くても10数箇所に対して、欧州は、一桁以上多い箇所に適用されており、大幅に遅れている。今後は構造用接着剤の適用範囲は増えてであろう。
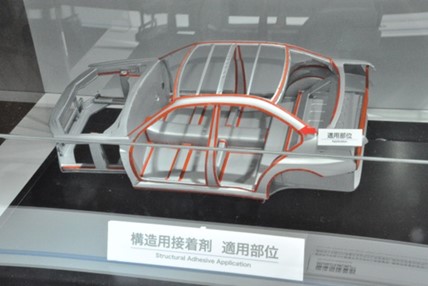
写真13 構造用接着剤適用部位の例
4-7 分子接着・接合技術(朝日ラバー)
写真14に分子接着・接合技術を適用した部材を示す。分子接着とは、接着させる物質の表面を加工して化学反応により貼り合わせるもので、接着剤を使用しない。接着剤による貼り合わせに比べ、経年による接着力の劣化がないこと、耐熱性・耐水性に優れていることといった特長がある。
EPDMとPI、EPDMとシリコーンゴムの接着サンプルであるがその他多くの組合せの接着例が展示された。
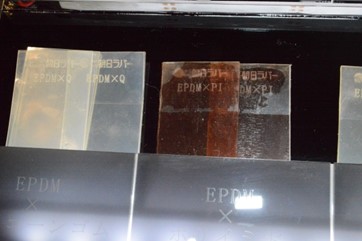
写真14 分子接着・接合技術
4-8 P-TOP工法(日昌製作所)
2015年のオートモーティブワールドで日昌製作所が新しいP-TOP工法を展示していたので以下に概要とその工法による接合を写真15に示す。
P-TOP工法は、表面処理(TRI) した金属を各種樹脂(主にエンプラ)にインサート成形し、製品状態でインサート金属の端部を加熱し、金属内部に温度勾配を発生させる。この工法では、従来金属との接合が困難であったPOMも可能となった。
展示されていたのはPA、PBT、PPSであったが、PPも検討中という。未だ、十分な接合強度は得られていない。新工法として注目される。
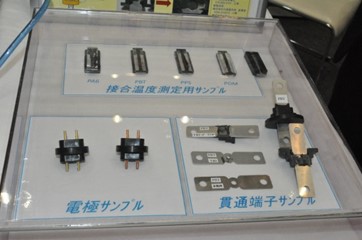
写真15 P-TOP工法による接合(日昌製作所)