特許文献から見た、射出成形CAE による ウェルドライン生成現象の予測と対策技術
東川芳晃
(編集者注:東川様は2020年2月26日にお亡くなりになりました。ご冥福をお祈りいたします。)
1. はじめに
樹脂射出成形品の品質向上は射出成形品開発にとって重要な課題です。現在では、CAE 技術を用いて製品・金型設計段階で、事前に予測し対策されています。とりわけ、 “ウェルドライン生成現象の予測と対策”は、CAE による予測精度も高いことから、各企業で過去数多くの技術が検討され、特許出願されています。
本稿は、本技術に関して調査した結果を、マテリアルライフ学会誌2015 年2 月号に投稿・掲載された報文「CAE を用いた樹脂射出成形品の品質向上 -ウェルドライン生成現象の予測と対策- 」(ページ2~12 に掲載)を、プラスチックス・ジャパン・ドットコムの読者向けに書き直したものです。
2.射出成形と成形不良現象
現在、自動車、家電・電子機器、精密機械等の工業部品は射出成形で生産されているものが多い。射出成形品の品質・性能は製品デザインと材料と成形の3つの要素が複雑に関係している。
樹脂射出成形品の品質向上には、使用材料、製品デザインを考慮した金型設計や成形条件を最適化する必要がある。中でも、成形時の不良現象対策は、製品の強度や耐久性を考える上で不可欠の課題である。
射出成形は複雑形状部品を一工程で精度よく大量生産できる成形法であり、成形工程としては、溶融、移送、冷却、固化のプロセスをたどる。この複雑な成形プロセスにおける賦形履歴は、成形品の品質・性能に大きく影響を及ぼす。
ところで、射出成形の成形不良現象の一つに、ウェルドラインがある。 ウェルドラインは、ほとんどの射出成形品で生成するが、プラスチック射出成形CAE4 )5 )(Computer AidedEngineering:計算機支援工学)により、事前に予測して対策可能な不良現象の一つである。
ウェルドライン(ウェルド)は、溶融樹脂が金型キャビティ内に充填中に、複数の樹脂のメルトフロントが会合した箇所の表面に生成するV 字状の細いスジである。そしてウェルドラインは、射出成形品の外観不良、寸法精度不良のほかに、製品の機械的強度低下を引き起こす。
そのため現在では、プラスチック射出成形CAE技術を用いて、ウェルドライン生成箇所を、製品設計・金型設計段階で事前に予測し、対策検討が行われるのが一般的である。特に製品の強度や長期寿命(耐久性)の観点から、応力集中部付近にはウェルドラインが生成しないように金型設計される。
3.プラスチック射出成形CAE技術
プラスチック射出成形CAE(以下CAE と略す)は、溶融樹脂が金型内に充填され冷却・固化し、金型から取り出された後、成形品が収縮し、そり・変形するまでの挙動をコンピュータでシミュレーションする技術である6)7)。一般的に樹脂流動解析や金型流動解析等の名称で呼ばれている。
本技術は、1970 年代後半から1980 年代に実用化が始まり8)9)、その後のコンピュータ及び周辺機器の著しい技術的進歩と低価格化、ならびに射出成形解析ソフトウェアの技術的進展により、射出成形による工業部品の製造分野で活用され、普及していった。
本技術は、製品の開発期間短縮、品質向上、生産性の向上、製造コスト低減等、製造メーカにとって必須の課題を達成するための基本ツールとして、樹脂射出成形品の製品設計・金型設計及び試作・製造工程において広く用いられている10)11)12)。
4.ウェルドラインとは
JIS K69001994 のプラスチック用語解説によれば、ウェルドラインは、ニットライン、ウェルドマークと呼ばれることもあり、“共に流れているプラスチックの二つ又はそれ以上の流体の融合によって形成される成形プラス
チックの表面のこん(痕)跡”であると定義している13)。
山田14)は不良現象としてのウェルドラインは、通常それに起因する強度低下をも意味するものであることから、「樹脂の合流によって生成し、非合流部との比較において外観あるいは物性にならかの差を生ぜしめる現象」と定義し、ウェルドと略記して議論を進めている。
本稿においては、主として、ウェルドラインを使用するが、特にこだわらず、引用文献に記載の用語をそのまま使用することにする。
山田14)はウェルドラインの生成形態を対向流ウェルド(タイプⅠ)と、並走流ウェルド(タイプⅡ)の2 タイプに分類している。(図1)。また、本間15)は4 タイプに分類し、Ⅰ)両側から流れてきた溶融樹脂がウェルド部で突き当る箇所、(Ⅱ)溶融樹脂がウェルド部で合流した後、他の方向に流れる箇所、Ⅲ)局部的に肉厚の薄い個所がある場合、周辺の厚い部分が先に充填し、最後に薄い部分が充填した箇所、そして、Ⅳ)スプルー、ノズル等で冷えた樹脂がキャビティに入った場合に生成するとしている。
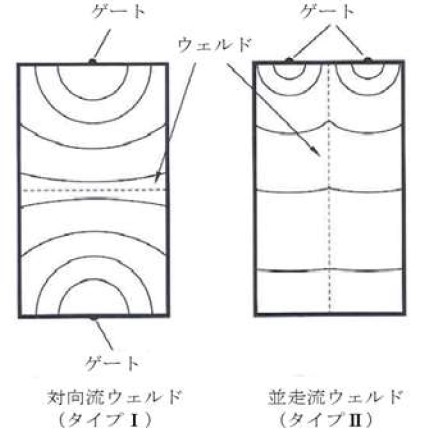
図1 ウェルドの種類14)
実際の射出成形では、ウェルドライン界面での流動圧力差により、一方の樹脂が他方の樹脂層にもぐりこみ、ふくれ現象が起こる。この現象は、特に自動車のバンパーフェイシャで問題となり、2 次ウェルドあるいは2 次ウェルドラインと呼ばれている。
5. ウェルドラインの生成メカニズム
ウェルドラインの生成および消失過程については、横井らが、ガラスインサートの可視化金型を用いた画像計測とウェルドラインの形状測定を行い、下記の研究結果を報告している16)、17)。
①溶融樹脂のフローフロント会合角が、ある値を超えた領域でウェルドラインが消失する会合角(ウェルドライン消失会合角)が存在し(図2)、樹脂の種類ごとに特定の値を示し、120°~150°に分布する。
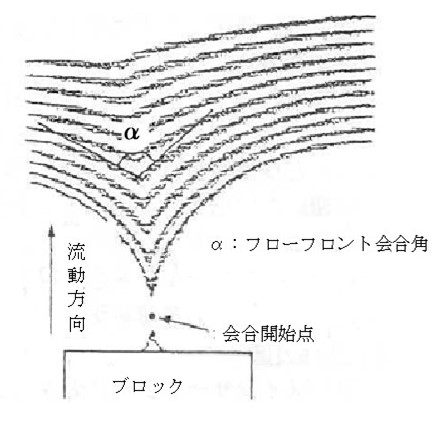
図2 画像処理により得られたフローパターンと会合角16)
そして②ウェルドライン生成機構として、2つのファウンテンフロー会合部曲面の主にキャビティ壁面近傍曲面部分が、キャビティ平面へと接するべく二次元的に展開されることによって、余剰表面積を生成し、これがウェルドラインを形成する、というモデル(図3)を提示している。
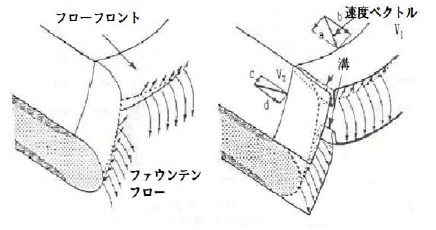
図3 ウェルド部のフローフロント流動挙動の模式図16)
従来から射出成形の樹脂流動解析により、ウェルドライン生成位置の予測は可能であったが、このウェルドライン消失会合角の知見を適用することにより、ウェルドライン消失位置の予測も可能となった。
このウェルドライン会合角、消失会合角の知見は、ウェルド生成の有無判定技術として現在の商用ソフトウェアのいくつかに使用されている。また、各企業から特許出願されているウェルドライン生成現象の予測と対策技術に関しても、この会合角、消失会合角の考え方に基づいたものが多い。
以下、ウェルドラインの生成現象に対するCAEを用いた予測と対策について、各企業から特許出願されている技術を紹介する。尚、ウェルドライン生成現象とCAE 技術以外の抑止技術については、例えば、山田、村田の報文14)に詳しく述べられているので、参考にされたい。
6.CAEによるウェルドライン生成現象の予測と対策
企業の研究者や技術者に課せられた重要なミッションの一つは、特許出願できる新規技術を開発することであり、開発技術をいち早く特許出願することである。企業で開発・活用されている樹脂成形技術は、特許出願されても、学会発表等されないものが多い。そのため、特許調査は企業の技術開発動向を知る上で有益な手段となる。
本稿では、各種工業分野で活用されているCAEを用いたウェルドライン生成現象の予測と対策について、特許出願された技術の調査結果を以下に紹介する。表 1~表 4 には目的・用途別に4つに分類した結果を示す。
6ー1 ウェルドラインの予測と対策技術1-1)~1-9)
ウェルドラインの予測と対策技術を、Tale1の特許文献1-1から特許文献1-9に示す。例えば、特許文献1-1(特開平7-1529)には、変性PPを用いた実験で、ウェルドラインの強弱と衝突時の樹脂流の角度との間に70%以上の高い確率で相関性があることを見出し、流動解析によって流動ベクトルから合流角を求めて(図4)、合流角が大きいほどウェルドラインが強く表れるとする予測技術が提案されている。
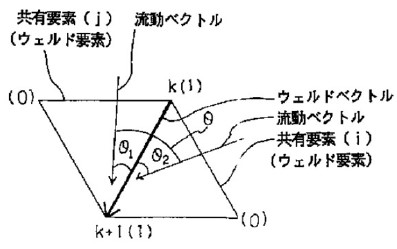
図4 共有要素と合流角(θ)を求める説明図1-1)
また、特許文献1-3(特開平10-128818)には、溶融樹脂の流動解析から算出した流動合流角や流動会合角(図5)の大きさのみでウェルドライン長を予測する方法は、精度が不十分であるとし、発明者らがポリスチレンを用いて実験と流動解析より見出した、樹脂、剪断速度および温度により変化する“べき指数”の値と、ウェルドラインの消失条件との間の相関関係を用いて、ウェルドライン長さを予測する技術が提案されている。
“べき指数”nは、η=C×γn の関係式で表現される。(ここでγは剪断速度、ηは剪断粘度、Cは定数)
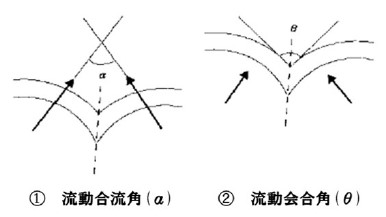
図5 流動合流角および流動会合角の概念図1-3)
表1 CAE によるウェルドラインの予測と対策に関するもの
表をPDFで開く⇒Table 1 CAEによるウエルドラインの予測と対策
6-2 CAEによるウェルドライン部強度の予測と対策技術2-1)~2-5)
ウェルドライン部は、製品の外観不良以外に機械的物性が劣るという欠点を有している。そのため従来から、いろいろなウェルドライン部の強度向上の手法が、検討されている。
成形方法による対策としては、例えば、スコリム(SCORIM:Shear Controlled Orientation in Injection Molding)と称される、ブルネル大学(英国)で1980 年代初期に開発された技術がある。スコリムは、溶融樹脂を金型内に充填したあと、2つのピストンにて金型内の溶融樹脂に交互に剪断力を加えながら、固化しかけた樹脂を移動させ、ウェルドの生成を抑制する技術18)である。
金型技術としては、金型に樹脂溜まりを設置して、ウェルドライン面の圧力差により、一方の流動樹脂を、他方の流動樹脂内部に潜り込ませて、くさび状になるようにしてウェルドライン部の面積を大きくする対策技術19)20)や、金型面内局部加圧装置を設置して、溶融樹脂に振動を加えて穴部周辺のウェルドラインをなくす等の技術20)21)22)が開発されている。
材料面での対策としては、例えばABS/PCアロイ、ABS/PBTアロイ、ABS/PAアロイのウェルド強度は相容化剤を加えることにより飛躍的に向上することが報告されている23)。
CAEを用いたウェルド部強度向上に関する予測・対策技術もいくつか特許出願されており、表 2 の 特許文献2-1 から文献2-5 に紹介する。例えば、特許文献2-1(特開平7-68616)には、ウェルド部の機械的強度を向上させるため、ウェルド部における圧力差により、一方の流動樹脂を他方の流動樹脂内部に潜り込ませた場合のウェルド面の形状を流動解析にて算出し、ウェルド面の変形寸法と強度との関係を把握するための技術が提案されている。ウェルド面の変形寸法は、樹脂流動速度と、ウェルド形成後充填が完了するまでの時間との積より算出している。
また、特許文献2-2(特開平07-205241)には、目的とする製品の流動解析を行い、ウェルドラインの会合角あるいは流速合流角を求め、一方実験から求めたウェルド強度と会合角あるいは流速合流角との相関関係をもとに、ウェルド部の製品の品質(強度など)の合否を判定する技術が提案されている。
ウェルド部の品質が不良の場合は、合格するまで成形条件を変更する。会合角以外の情報(成形条件)も考慮する場合は,次式によりウェルド特性の予測が可能である.W= a1F(ウェルドライン会合角あるいは流速合流角)+a2F(温度)+a3F(圧力)+a4F(流速)。ここで、Wはウェルド部の特性を示す定量値、Fは各因子の関数、aIは係数であり、これらはあらかじめ実験解析とCAE解析により求められるとしている。
また、特許文献2-4(特開2005-169909)には、射出成形品の衝撃強度を予測するにあたり、まず流動解析でウェルド位置を特定し、流動解析のメッシュモデルをそのまま用いて、実験から求めたウェルド部の会合角と物性値の関係(強度の変化の情報)をもとに、ウェルド位置の物性値を補正して精度の高い衝撃解析を行う技術が提案されている。
表2 CAE によるウェルド部強度の予測と対策
表をPDFで開く⇒Table 2 CAEによるウエルド部強度の予測と対策
6-3 CAEによるウェルドライン生成位置の最適化技術3-1)~3-3)
CAE技術を活用した仮想試作による製品・金型設計プロセスは、著しい技術的進歩ではあるが、ランナ、ゲートの配置や寸法、成形品形状、厚厚など、設計パラメータの最適化については、従来の検討と同様、人手による試行錯誤のプロセスに頼らざるを得なかった。
しかしながら、1990年後半に汎用の最適化支援ソフトウェアが上市されると24)、最適化支援ソフトウェアと、射出成形解析のソフトウェアと、汎用モデル作成ソフトウェアを統合することにより、人手ではなく最適化支援ソフトウェアを用いて、最適化計算を自動で実施させる技術が産業界で活用
されるようになった。例えば、所望の位置にウェルドラインが生成するように、設計パラメータを事前に設定した制約条件の範囲で、自動で決定することができるようになった25)26)。
特に、最適化したい目的性能が複数の場合(多目的最適化と呼ばれる)、例えば、成形品のウェルドライン位置と成形に必要な型締力や成形品重量を目標値に収まるように、上記のいくつかの設計パラメータを決定(最適化)する場合には、手作業では困難であり本技術が非常に威力を発揮する。
上記の最適化技術がウェルドライン生成位置や成形品品質の最適化に適用され、特許出願されている。以下3件紹介する(表3) 。
特許文献3-1(特開2002-192589)には、射出成形品のウェルド位置を所望の位置に容易に設定することを可能にする、射出成形品の設計パラメータ決定方法および装置が提案されている。
特許文献3-2(特開2005-007859)には、バルブゲートを有する樹脂射出成形金型を用いた射出成形において、ウェルド位置制御や型締力低減を目的として、金型設計パラメータと成形プロセスパラネータを同時に最適化する金型の設計方法及び射出成形品の製造方法が提案されている。
特許文献3-3(特開2005-169766)には、射出成形金型仕様の決定過程を効率化すること、評価条件に従い最適化された金型の仕様を求めること、及び、成形体の形状品質と剛性品質の観点に基づいて金型仕様を決定することを目的とする金型最適化装置、金型最適化プログラム、及び、金型最適化制御プログラムに関する技術が提案されている。
最適化処理例のフローチャートを図6に示す。その説明は表3のNo.3-3を参照。
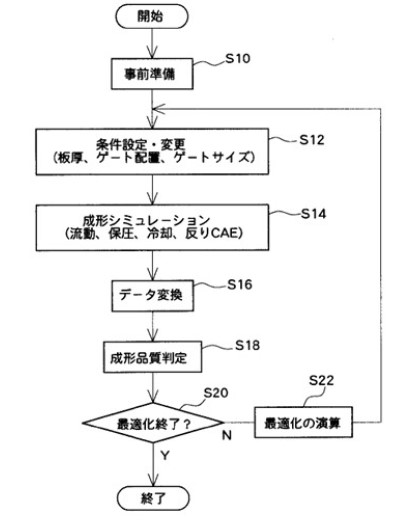
図6 最適化の処理例を示すフローチャート3-3)
表3 CAE によるウェルドライン発生位置の最適化
表をPDFで開く⇒Table 3 CAEによるウエルドライン発生位置の最適化
6-4 CAEによる2次ウェルドの予測と対策技術4-1)~4-6)
ウェルド部の圧力差により、一方の流動樹脂が他方の流動樹脂内部に潜り込む現象は、成形品のウェルド部の強度アップには効果があるが、成形品表面のウェルドライン近傍に微小の凹凸を生じさせる原因となる。
特に表面外観が重要視される、例えば乗用車のバンパーの成形に対しては、この不良現象を予測、対策するための特許が数件出願されている。その予測・対策技術をTable 4の 特許文献4-1から特許文献4-6に紹介する。
例えば、特許文献4-1(特開2000-343575)には、タルク入り樹脂の流動解析を行い、1次ウェルドライン上に複数の仮想粒子を生成し、その仮想粒子の移動経路と移動距離から、流動樹脂の一方が他方の流動樹脂内へ侵入した潜り込み距離を求め、実験値との相関式を用いてその潜り込み距離から成形品の表面に生じる凹凸の生成位置や高さ(または深さ)を予測する技術が提案されている。実施例には自動車用バンパーを用いている。
また、特許文献4-5(特開2008-207440)には、シェルメッシュの流動解析を実施し、ウェルドラインの周辺での樹脂の流れ方向に沿った移動量の経時的変化と、樹脂の流動層厚みの経時的変化を推定し、両者の経時的変化に基づいて、2次ウェルド界面形状を推定して、成形品の品質を予測する技術が提案されている。 この品質予測方法は、予め試作試験等により評価関数を求めておき、この評価関数とウェルド界面形状とにより成形品表面の品質を予測する方法である。
評価関数は、成形品の表面に現れる面ひずみは、ウェルド界面の厚さ方向中央部での曲率が大きい程(先端が尖っている程)良好でありまた、ウェルド界面が途中で折り返す場合に、ウェルド界面が途中で折り返さない場合に比べて良好である値をとるとしている(図7)。
理由としては図8において、(A)はウェルド界面600の近傍604とそれ以外の部分でタルク配向が大きく異なり、604は樹脂が固化する際の厚さ方向の収縮量が小さいため、結果として成形品の表面に大きな面ひずみ606が形成される。一方(B)は、ウェルド界面610の近傍614とそれ以外の部分でタルク配向がそれほど異ならず、樹脂が固化する際の厚さ方向の収縮量もそれほど異ならないから、結果として成形品の表面には小さな面ひずみ616が形成される。
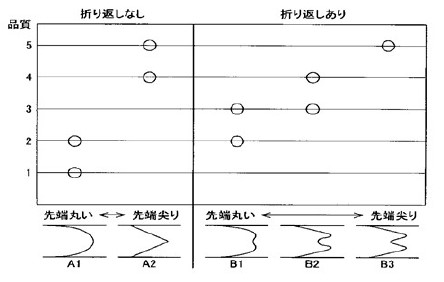
図7 ウェルド界面の形状と成形品の関係4-5)
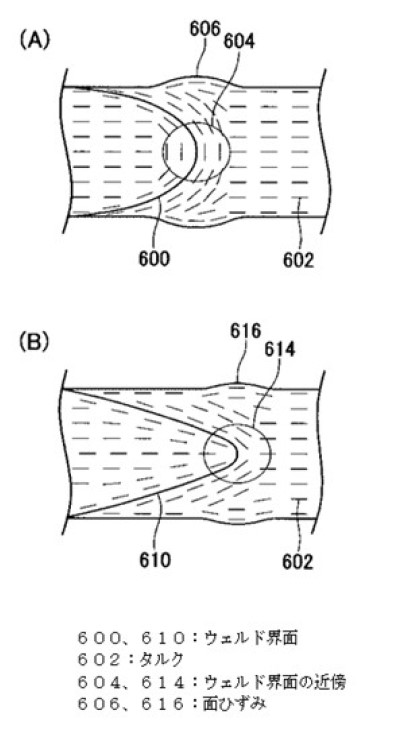
図8 樹脂のタルク 配向とウェルドライン近傍の面ひずみの関係4-5)
表4 CAE による2 次ウェルドの予測と対策
表をPDFで開く⇒Table 4 CAEによる2次ウエルドの予測と対策
7. まとめ
本稿では、射出成形CAE によるウェルドラインの不良現象の予測と対策に関する技術動向について、産業界から特許出願されている技術の調査結果を紹介した。
技術内容を、目的・用途別に4つに分類した。要約すると下記の通りである。これら技術の中には、実験値との相関関係に基づき、予測精度の向上を図ったものが数多くみられた。
1)ウェルドラインの予測技術としては、流動合流角、固化層厚み、べき指数、マーカ粒子の属性、仮想粒子の移動軌跡、繊維配向解析でウェルドライン生成位置を予測する技術が提案されており、またウェルドライン対策としては、乱流生成用補助バルブゲートの設置、バルブゲート付き金型バルブ開閉時間最適化、開口部コーナ近傍にウェルドを生成させる技術が提案されていた。
2)CAEによるウェルドライン部強度の予測と対策技術としては、ウェルド面変形寸法の予測技術、実験から求めたウェルド強度と会合角あるいは流速合流角との相関関係に基づいたウェルド強度の予測技術、強化部材インサートによるウェルド部の補強対策技術、ウェルド部強度を補正した衝撃解析技術、ウェルド部強度を考慮した構造解析技術が提案されていた。
3)CAEによるウェルドライン生成位置の最適化技術としては、最適化支援ソフトウェアと射出成形解析のソフトウェアと汎用モデル作成ソフトウェアを組み合わせて、ウェルド位置最適化、ウェルド位置制御と型締力低減、および、製品品質(形状と剛性)の最適化技術が提案されていた。
4)CAEによる2次ウェルドの予測と対策技術については、2次ウェルドによる成形品表面の凹凸位置予測、2次ウェルドによる成形品表面品質の予測、2次ウェルドの生成抑制技術、2次ウェルドラインの位置予測、2次ウェルドライン界面形状推定と成形品品質の予測、2次ウェルドラインの突出高さと外観品質予測の各技術が提案されていた。
5)最後に、現在商用で使用されている射出成形解析ソフトウェアを表5 に示す。
表5 商用の射出成形解析ソフトウエア
<関連記事⇒完全三次元流動解析ソフトMoldex3Dのことなら㈱セイロジャパンへ>
引用文献
1)~3)割愛
4)E.C.Bernhardt Ed :“CAE for Injection Molding”, Hanser Publishert,N.Y.132-190 (1983)
5)Louis T. Manzione 編,天野修訳:“射出成形用CAE”,工業調査会(1989)
6)小山清人:成形加工, 成形加工,6[9],591(1994)
7)佐藤勲:成形加工, 成形加工,6[9],597(1994)
8)ColinAustin:プラスチックス,33[12],33(1982)
9)桝井捷平,東川芳晃,左海登志雄,菊地利注,臼井信裕:住友化学, 1984-Ⅱ,77-81(1984)
10)中野亮,澤田聡,松村淳一:成形加工,5[11],726(1993)
11)小西邦明,三瓶喜正,小林亜男:成形加工,5[11],731(1993)
12)吉田稔,比枝敏明,宗正和美:成形加工,5[11],737(1993)
13)JIS K69001994
14)山田浩二,村田泰彦:成形加工,20[10],715(2008)
15)本間精一:プラスチックス, 55 [7],92.(2004)
16)横井秀俊,村田泰彦,織山俊雄,戸田清澄:成形加工‘89,245-248(1989)
17)横井秀俊,村田泰彦,岡克典,渡辺広三:成形加工,9[4],290(1997)
18)A.Y.ZHANG,E.JISHENG,P.S.ALLAN,M.J.BEVIS:Journal of Materials Scienc,37,15,3189-3198(2002)
19)ポリプラスチック株式会社:特開平5-285990(1993)
20)本田技研工業株式会社:特開平7-227888(1995)
21)住友重機械プラスチックマシナリー株式会社:特開平5-228969(1993)
22)宇高靖,小倉信宏,吉田秀樹:成形加工, 5[11],712(1993)
23)阪野元, 高橋和則,青木寛充,藤原隆祥:成形加工,8[9],599(1996),阪野元,青木寛充,山口秀樹,高川泰延:成形加工,9[6],404(1997),阪野元,藤原隆祥,小倉清,矢野正人:成形加工,9[6],412(1997)
24) CAOフロンティア’99資料:Engineous Japan Inc.(1999.11.30)
25)東川芳晃, 広田知生, 永岡真一:住友化学, 2004-Ⅱ,15-25(2004)
26)スーパーコンピューティング技術産業応用協議会編:“産業界におけるコンピュータ・シミュレーション”,アドバンスソフト出版事業部(2010)p.156-178
引用特許文献(表1 ~表4)
1-1)トヨタ自動車株式会社:特開平7-1529(1995)
1-2)カルソニック株式会社:特開平09-019953(1997)
1-3)電気化学工業株式会社:特開平10-128818(1998)
1-4)株式会社豊田中央研究所:特開平11-077782(1999)
1-5)株式会社日立製作所:特開平11-192643(1999)
1-6)キャノン株式会社:特開2001-277308(2001)
1-7)東レ株式会社:特開2002-200662(2002)
1-8)東レ株式会社:特開2002-321265(2002)
1-9)豊田合成株式会社:特開2003-154550(2003)
2-1)三井石油化学工業株式会社:特開平7-68616(1995)
2-2)宇部興産株式会社:特開平07-205241(1995)
2-3)東洋紡績株式会社:特開2000-343575(2000)
2-4)富士通テン株式会社:特開2005-169909(2005)
2-5)三菱電機株式会社:特開2010-69653(2010)
3-1)東レ株式会社:特開2002-192589(2002)
3-2)住友化学株式会社:特開2005-007859(2005)
3-3)トヨタ自動車株式会社:特開2005-169766(2005)
4-1)日産自動車株式会社:特開2000-343575(2000)
4-2)トヨタ自動車株式会社:特開2005-074786(2005)
4-3)トヨタ自動車株式会社:特開2005-144860(2005)
4-4)東レエンジニアリング株式会社:特開2008-001088(2008)
4-5)トヨタ自動車株式会社:特開2008-207440(2008)
4-6)マツダ株式会社:特開2011-201108(2011)