製品設計の「キモ」(16)~ プラスチック製品の立ち上げをスムーズに行うには
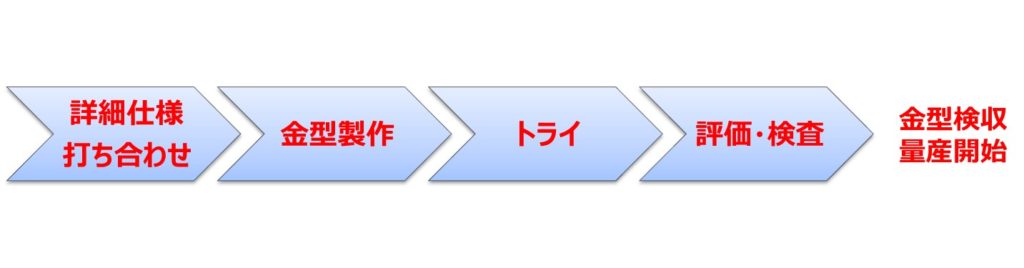
製品設計コンサルタント
田口技術士事務所 田口宏之
1. はじめに
前回はプラスチック製品の成形パートナーの選び方について解説した。
関連情報:製品設計の「キモ」(15)~「プラスチック製品の成形パートナーの選び方」
よい成形パートナーに巡り合えたとしても、品質に対するお互いの認識がずれたまま金型製作まで進めていくと、なかなかうまくいかないものである。今回はどのようなことに注意すれば、量産品をスムーズに立ち上げることができるかについて解説する。
※製品の基本的な形状の設計、材料選定は済んでおり、製品を射出成形メーカーで生産するケースを想定して話を進める。
成形パートナーが決まった後、量産開始に至るまでの流れは図1の通りである。
それぞれのフェーズで考慮すべき事項について解説する。
2. 詳細仕様打ち合わせ
基本的な形状や材料が決まれば、後は金型を作るだけだと考えるかもしれない。しかし、量産開始までにトラブルになりやすいのは、図面に記載されていないような細かな事項であることが多い。
量産開始までをスムーズに、しかも短期間で終わらせるためには、これらの細かな事項について、入念にすり合わせしておくことが不可欠である。表1は事前にすり合わせしておくべき事項の例を示す。
表1 事前にすり合わせしておくべき事項の例
項目 | 例 | |
材料 | 材料 | ABS |
グレード | GR-0500(デンカ) | |
配合剤 | 酸化防止剤AO-50(ADEKA) | |
再生材(端材の利用) | 使用不可 | |
外観 | 外観範囲 | A面:外観面(外観検査基準適用) B面:外観面(一部外観検査基準適用) C面:非外観面(外観検査基準適用外) |
色 | 日塗工N-95(ホワイト) | |
色差 | ΔE≦2 目視で異常なきこと |
|
異物 | きょう雑物測定図表にて検査すること 外観部A面:0.2mm^2以下 外観部B面:0.5mm^2以下 |
|
外観不良 | 下記の成形不具合が目立たないこと。必要に応じて限度見本を取り交わす。 <成形不具合の例> ・ヒケ、白化、スジ、色調ムラ、艶ムラ、バリ、傷、汚れ、ウエルドライン、ナミ、ブツ、反り、変形等 |
|
PL(パーティングライン) | 図面にPL位置を明示すること 段差は0.3mm以内とする |
|
ゲート処理 | ゲート処理は取り交わしサンプルに基づいて実施すること | |
試作数 | <金型検収用> 10個 <製品評価用> 100個 |
|
梱包仕様 | 梱包仕様書に基づいて実施すること | |
生産予定数 | 1万個/年(5年程度) |
材料
「ABS」「PP」といった材料名だけではなく、「デンカ/GR-0500」といったメーカー、グレードまで決めておく。
グレードを明記しない方が、材料を柔軟に変更できるのでよいのではないかと考える人もいるかもしれない。しかし、同じABSでもグレードによって特性は大きく異なる。かつて「○○グレード相当」と記載された製品で、多くの失敗事例を見てきた著者としてはお勧めできない。製品の品質を安定させたいのであれば、グレードまで明記することが必須である。
配合剤の有無や配合量も材料の特性に大きく影響する。可能であればこれも図面や仕様書に明記したい。しかし、材料グレードとは異なり、こちらは開示してくれないケースが多い。
配合自体が成形加工メーカーやコンパウンドメーカーのノウハウとなっていることが多いためだ。非開示の場合は何を配合しているのかだけでも確認を行う。
再生材(端材)利用の可否も決めておく。再生材を利用した方が材料単価は安くなるが、変色や強度低下の原因となる。外観部材の場合は使用しない方がよいだろう。非外観部材の場合は、製品強度などに影響のない範囲で使用しても構わない。その場合は配合割合の上限を決めておく。
外観
外観の良否は見る人によって異なるため、立ち上げや量産時に問題となりやすい。問題の発生頻度を減らすために、外観基準を適用すべき範囲を明確にするとよい(図2)。
色は「ホワイト」「黄色」といった曖昧な指定ではなく、日塗工(日本塗料工業会)やDICなどいつでも入手可能な色見本の色番で指定する。現物サンプルで指定することもあるが、色は経年で変色するため、数年おきに取り替える必要がある。
また、成形品は色番通りの色を完璧に再現できるわけではない。組立品の場合はほんの少し色が違うだけでも目立ってしまい、クレームになりやすい。色違いの上下限を設定しておくことが望ましい。量産前に色違いのサンプルを入手することは難しいため、色差を用いることが多い。
色差は色差計で簡単に測定することができる。ただし、使用する色差計によってデータに違いが生じやすいことや、同じ色差でも見え方に大きな違いがあることから、目視でのチェックも実施した方がよい。
ホワイト系の製品では異物が問題になりやすい。言われるまで気付かなかった異物も、一度目にすると気になってしまうやっかいな不具合だ。異物を完全になくすことは難しいため、これも判断基準を決める必要がある。基準にはきょう雑物測定図表や実物のサンプルがよく使われる。
PL(パーティングライン)の位置や段差の大きさ、ゲートの位置や処理方法についてもすり合わせをしておく(図5)。PLやゲートの位置は成形加工メーカーとすり合わせした後、図面に明記する。
試作数
検査や評価のための試作数量が多い場合、事前に知らせておかないと、材料や成形機の手配で余分な時間がかかることがある。また、それらの試作品の製作費用をどちらが負担するのかも決めておいた方がよい。
梱包仕様
梱包仕様の検討は後回しになりがちであるが、製品コストにも影響があるので、できるだけ早い時点で梱包仕様書の作成を依頼する。
生産予定数
製品廃番までの大まかな生産予定数を伝える。1万個作る場合と100万個作る場合では、金型に使う材料も変わる。
上記のように仕様を細かく決めることによって、見積りの精度を高めることができる。立ち上げの後工程になって、要求事項が増えたので当初の見積りでは対応できないという話になるのを避けられる。
また、成形加工メーカーとのすり合わせ結果は、口約束にするのではなく、図面か仕様書のどちらかに明記する。
議事録もよく使われるが、最終決定が何なのか分からなくなることが多いので、できれば図面か仕様書に情報を集約した方がよい。図面と仕様書は「契約書」であるという意識を両者で共有してプロジェクトを進めたい。
3. 金型製作・トライ
詳細仕様の打ち合わせを済ませ、図面・仕様書が完成したら、金型製作に着手する。金型完成には通常30~45日必要である。金型ができたらすぐに図面通りの製品が成形できるわけではなく、トライと呼ばれる成形テストを複数回行う。
製品の難易度が高かったり、金型の修正を何度もやらなければならなかったりする場合は、トライを行う期間が長くなる。
このフェーズで依頼者側ができることは少ないが、可能であればトライに立ち会った方がよい。事前に明確に決めることができなかった基準をその場で決めたり、気付かなった不具合などを発見できたりするからである。
立ち会わずに成形加工メーカーから送られてくる「チャンピオン」品だけを見ていては気付かないことも多いものだ。
想定通りの製品に仕上げることができず、費用をかけて金型を修正しなければならないこともある。その場合に問題になるのが、依頼者側と成形加工メーカー(あるいは金型メーカー)のどちらが費用負担をするかということだ。
費用負担の考え方は業界や地域によって異なるようだ。しかし、図面や仕様書を契約書として考え、契約書と異なる要求を依頼者側がする場合は依頼者側の負担、契約書通りに製品が作れない場合は成形加工メーカーの負担とするのが最も合理的であると考える。
4. 評価・検査
トライで成形した試作品について、事前に想定した性能を確保しているかどうかを評価する。また、試作品が図面・仕様書通りに作られているかも検査する。検査では数個程度の試作品が図面寸法内に入っていればOKというわけでなく、量産においても寸法内に入る実力(工程能力)があるかどうかを考えなければならない。
図6の場合、工程能力Cpは1.00~1.33の範囲となる。これは1万個成形したうちの0.63個~26個程度が「不良」となることを示している。この工程能力で十分かどうかの判断を行う。
製品が図面・仕様書通りにできていることが確認できたら金型検収となる。金型費用の支払い方法は契約によって異なるが、国内では金型検収後に行うことが一般的である。射出成形の金型は高価であるため、検収作業は可能な限り速やかに実施することが最低限のマナーであると考える。
4. おわりに
プラスチック製品の立ち上げ時に、すり合わせしておくべき基本的な事項を取り上げた。もちろん取り上げた事項以外にも製品によって様々なポイントがあるだろう。細かい事項まですり合わせができていれば、プラスチック製品の立ち上げは非常にスムーズに進むだろう。