NPE2024視察レポート
秋元技術士事務所
秋元英郎
1.はじめに
NPEは3年に一度米国で開催されるプラスチックの展示会であり、2012年にそれまでのシカゴからオーランドに移されて開催されている。会場はオレンジ・カウンティ・コンベンション・センター(OCCC)で5月6~10日の5日間にわたり開催された。OCCCは西ホールと南北ホール(メインの入り口は南口)に分かれており、デュッセルドルフメッセ会場には及ばないが、幕張メッセの2倍以上の面積が有る。西ホールは機械が多く、南ホールは材料メインであるが、材料メーカーの出展は多くはなかった。出展者数は約2300社、来場者数は約50,000人(出展者パスでの入場を除く)であり、ゆったりしていた(大混雑という感じではなかった)。NPEの事務局は非常にしたたかで、ブースに位置はこれまでの連続出展回数順に選べるため、一度出展を見送るとブース位置が不利になるとのことである。
本レポートでは、射出成形機メーカーの展示内容を中心に紹介する。
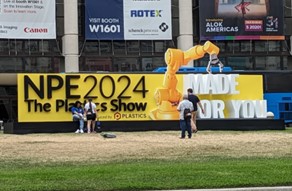
写真1 会場屋外のサイン
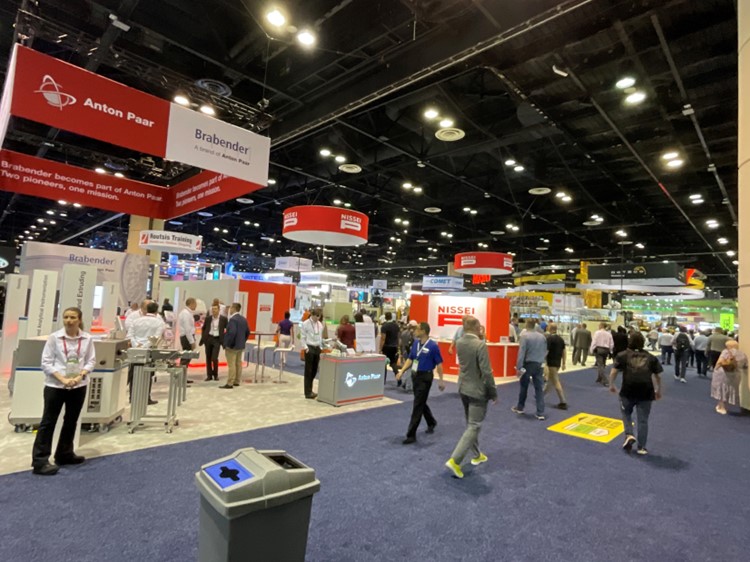
写真2 西ホールのようす
2.射出成形機メーカー
2-1 HUSKY
2-1-1 プリフォーム専用成形システム
PETボトル生産のトータルソリューションメーカーとして、プリフォーム専用の射出成形機「HyPET 6e」で成形実演を行っていた。144キャビティでサイクルタイムが4.5秒であった。装置の特徴としては、射出完了後で冷却前のプリフォームをロボットで取り出し、外部冷却するユニットに渡し、冷却が完了したら真下に落下させる。製品の品質は一定数ごとに寸法を自動測定して管理している。動画はこちらから。
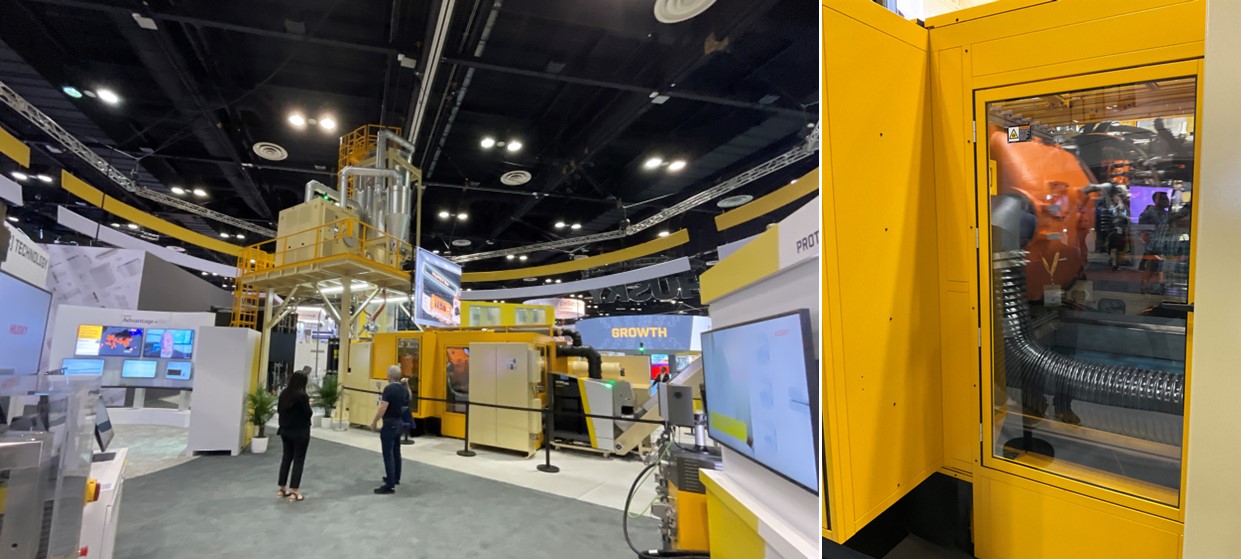
写真3 プリフォーム専用成形機
左:装置外観、右:取り出し装置部分
2-1-2 PET製ボトルキャップ(モノマテリアル)
参考出品として、PET樹脂製のボトルキャップが展示されていた。ボトル本体とキャップを単一素材にする目論見である。現在非炭酸飲料用のキャップは実用レベルに到達し、炭酸飲料用キャップについても2025年には目標の特性が出せる見込みとのこと。炭酸飲料用にはより高い寸法精度でガス抜けを防ぐ必要があり、PPやPEのような比較的柔軟な素材に比べて難易度は高くなる。ブロー成形と射出成形は最適な分子量領域が異なるので、一括してボトル用原料として再生可能なのか、今後見守っていく必要がある。
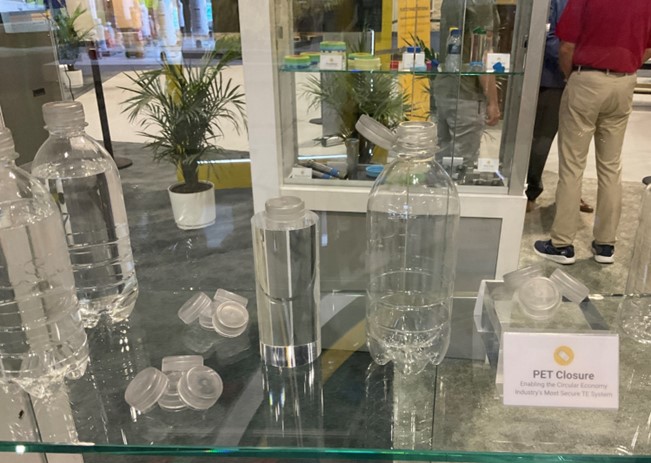
写真4 PET樹脂製ボトルキャップ
2-2 Milacron
2-2-1 使用済みプラスチックのサンドイッチ成形
環境対応技術として、使用済みプラスチック(PCR)をサンドイッチした塗料容器(20L)を成形していた。デモンストレーションとしてわかりやすくするためにPCRに着色していたようで、断面も見ることができた。PCRは最大50%まで添加していたとのことである。また、インモールドラベルも行っていた。
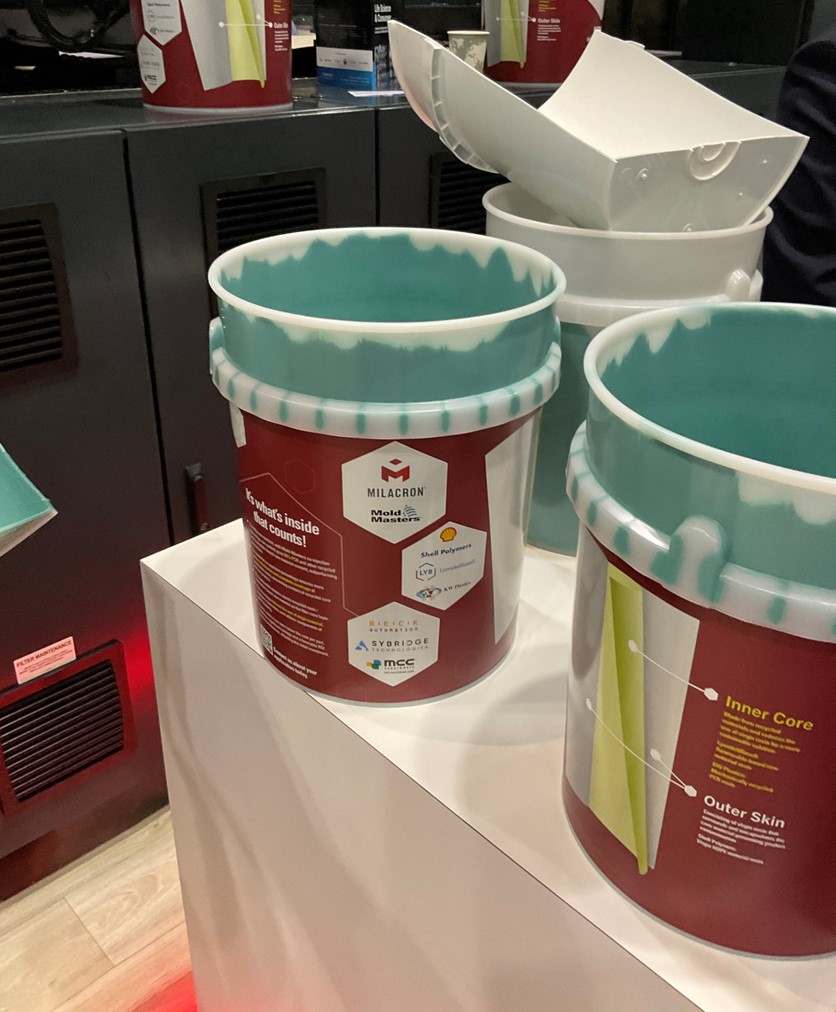
写真5 成形デモを行っていた容器
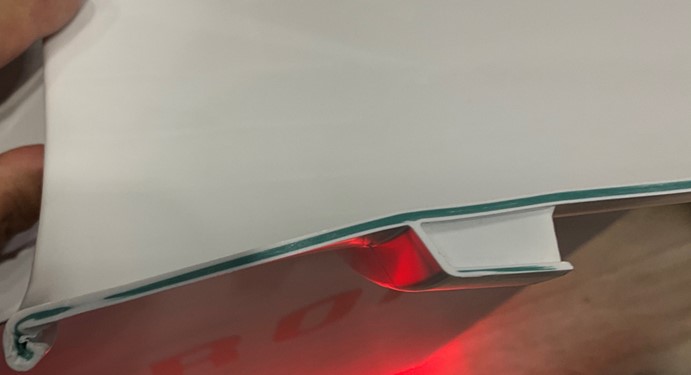
写真6 断面(青い部分が使用済みプラスチック)
2-2-2 フィルム加飾
クルツの加飾フィルムを用いたフィルムインサート成形を行っていた。工程は加飾フィルムのロールからシートを金型に下ろし赤外線ヒーターで加熱、開いた金型から真空引きして可動型の金型キャビティによって予備賦形し、金型を閉じて樹脂を射出して積層する。成形後にはフィルムは四角形に打ち抜かれてロボットで取り出し、連続的にトリミングが行われる(写真7)。なお、同じ成形品はクルツのブースにも展示されていた。
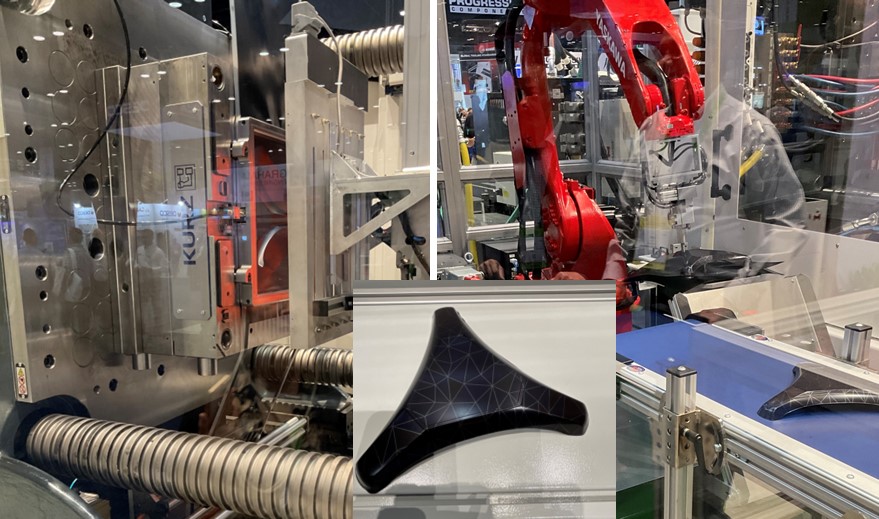
写真7 フィルムインサート成形のようす
左:赤外線ヒーターによる予備加熱、中央:最終成形品(トリミング後)、右:トリミング工程
2-3 KraussMaffei
アップサイクルのデモ、使用済みプラスチックを原料とした成形、3Dプリンティング等の実演およびサンプル展示があった。
2-3-1 アップサイクル
「医療用PP容器の射出成形→粉砕→液状着色剤で青く着色→金属部品のインサート成形」を連続的に行う成形デモを見せていた。
写真8はPP製医療チューブ(32個)を成形しているようすである。成形機は非常にコンパクト化されており、射出用サーボモーターはスクリューを押すのではなく引く方向にレイアウトされている。なお、型締側がダブルトグルのレイアウトであった。
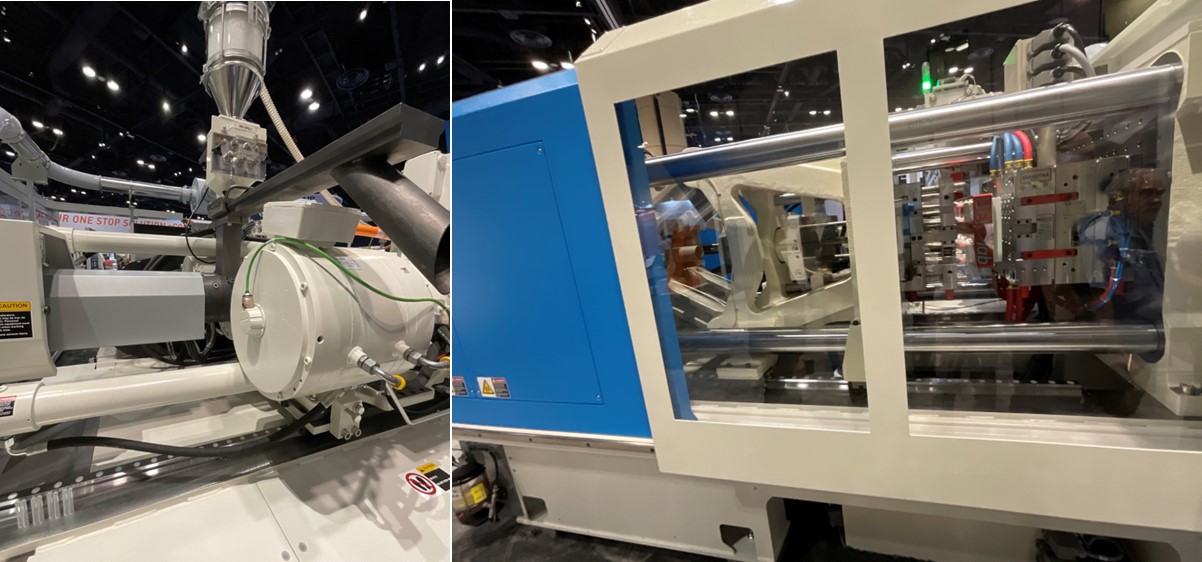
写真8 医療用PP容器の成形
左:コンパクトな射出用サーボモーターの配置、右:型締側
写真9は着色工程のようすである。流れてくるペレットを一定量貯めて色相測定を行い、3種類の液状色材の混合比率の調整を行っていた。色材は3種類が混合されて1本の注入口から注入される。
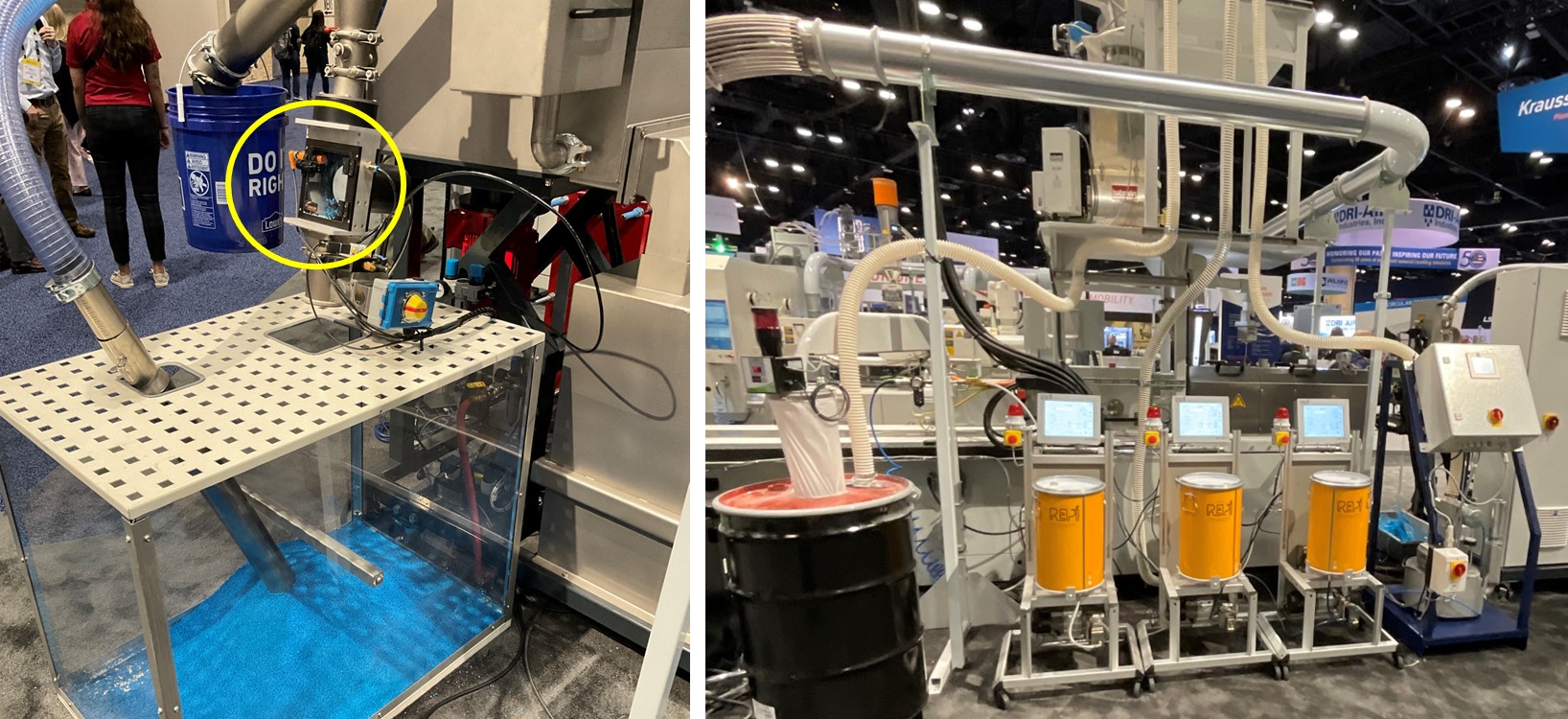
写真9 アップサイクルにおける着色工程
左:コンパウンドの色相測定(○で囲った部分)、右:3色の液体色材を混合して注入
できあがった青色ペレットは次工程へ空気輸送され、金属をインサートして栓抜きを成形していた。栓抜きの柄が青色PPで、金属の部分に二次元バーコードが印字されていた。
2-3-2 使用済みプラスチックの直接成形
分別しにくい使用済みプラスチックにフィラーや改質剤、着色剤を混合して成形まで行う工程を実演していた。使用している成形システム(直接コンパウンド射出成形 DCIM)である。成形機は原料のミキサー、混錬が可能なスクリュー、射出用プランジャー、型締めユニットから構成されていた。写真10にDCIM成形機の外観を示した。射出ユニットの上には6種類の原料をフィードできるフィーダー群とミキサーが配置されており、その下には斜めに配置された混錬部と水平に配置された射出プランジャーが配置されている。型締ユニットは省スペースの2プラテンであり、システム全体としての設置面積が小さくなるように設計されている。混合のようすは内部をカメラで観察できるようになっていた(写真11)。
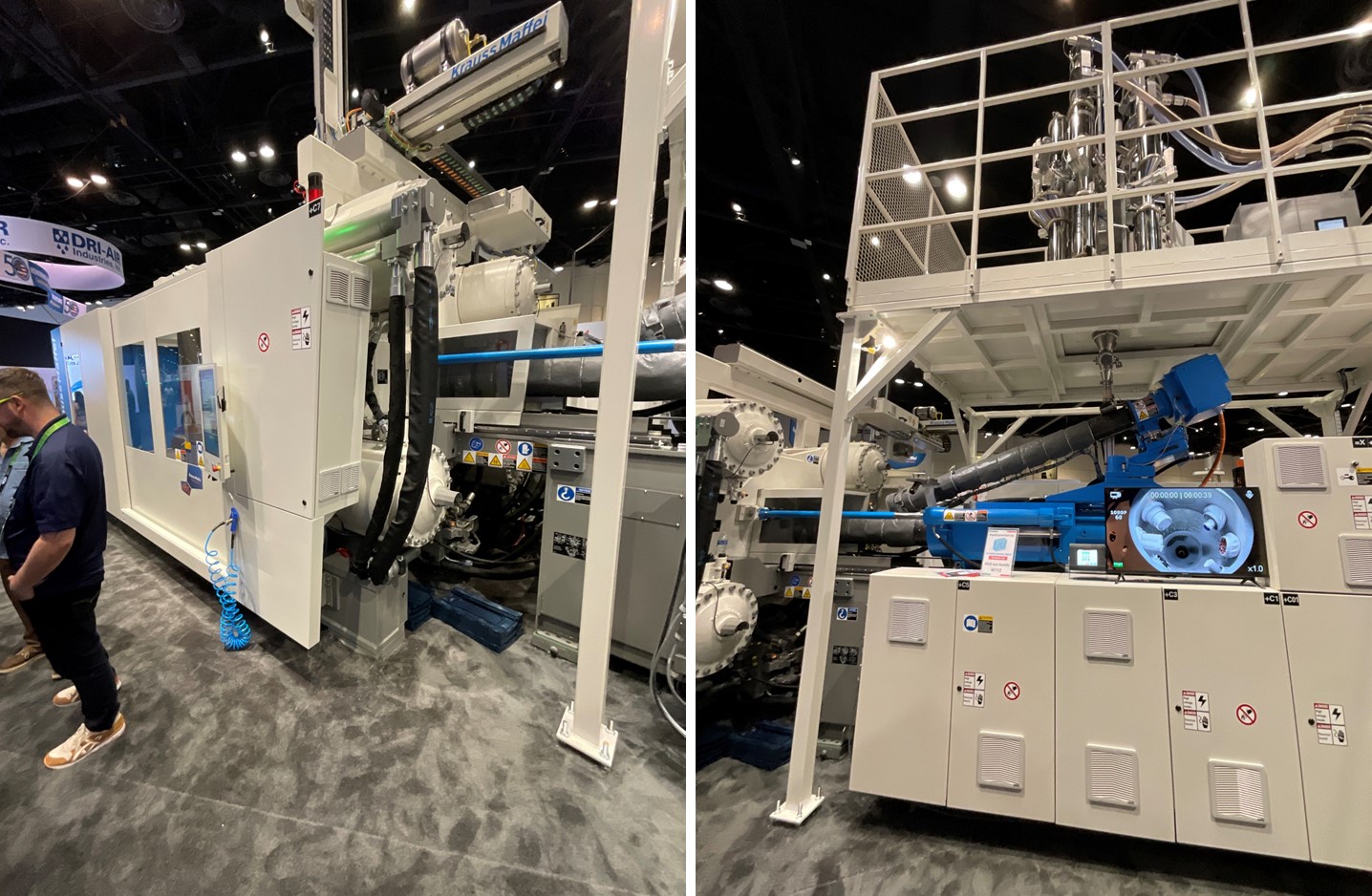
写真10 直接コンパウンド射出成形システムの装置
左:2プラテンの型締ユニット、右:混錬部分と射出プランジャー
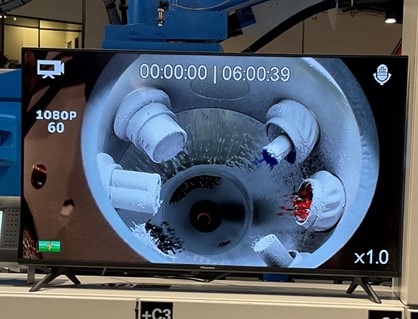
写真11 原料混合のようす(リアルタイムで観察)
2-3-3 3Dプリンティング
CLEMSON Universityとの共同プロジェクトとして試作された、炭素繊維入りフィラメントから造形した自動車部品が展示されていた(写真12)。
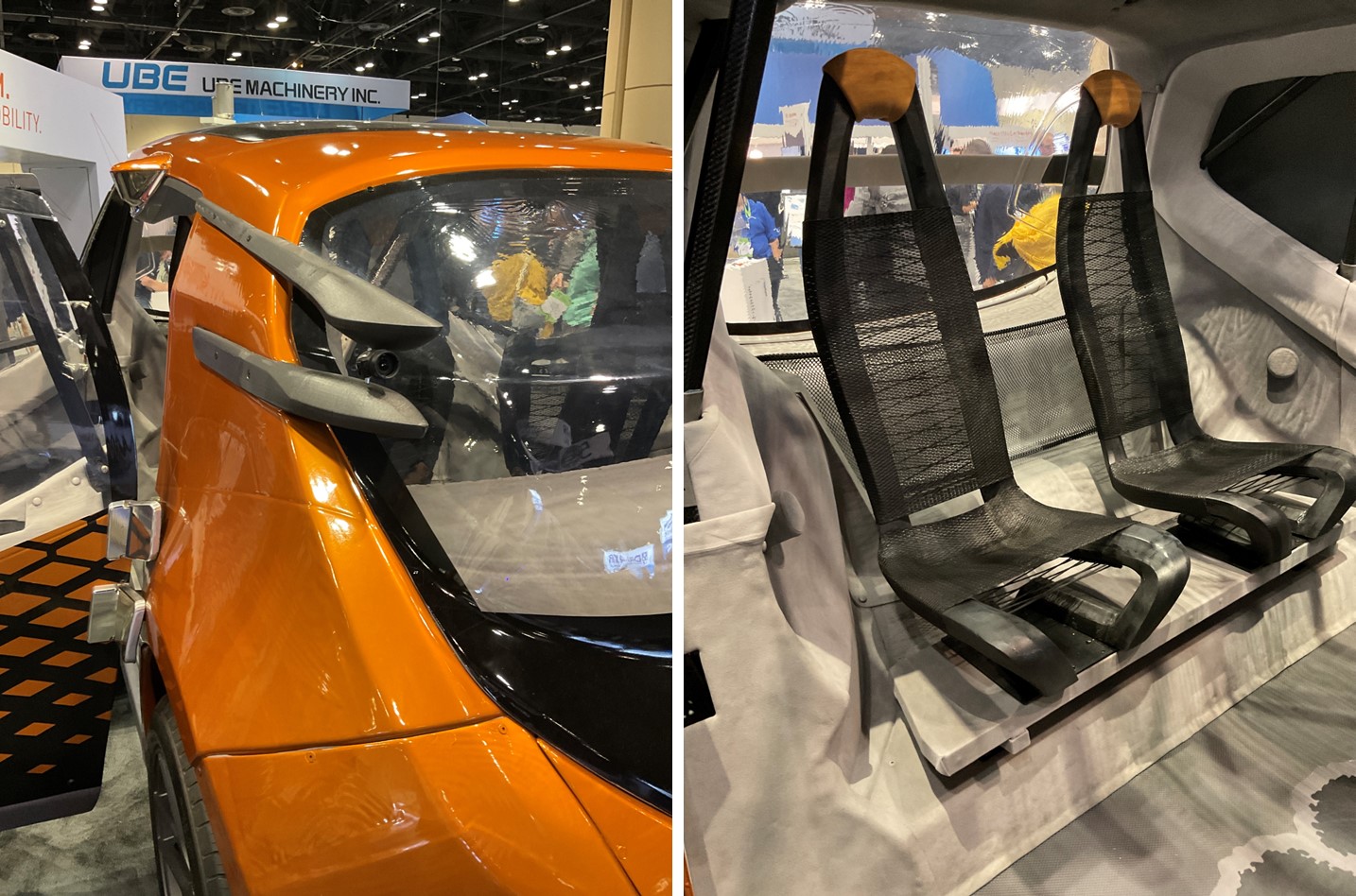
写真12 炭素繊維入りフィラメントの3Dプリンティング
2-4 ENGEL
フィルムインサートと金型内塗装の組み合わせ技術の実演、2型を入れ替えながらの成形実演、使用済みプラスチックからの直接成形の実演等が見られたので詳しく報告する。その他にインモールドラベル成形、液状シリコーンの成形、二色成形等の実演もあった。
2-4-1 フィルムインサート成形と金型内塗装の組み合わせ
可動型が2キャビありスライドする構造になっており、二段階で成形を行う。一段目は加飾フィルムをインサートしてPP(白)を射出し、二段目では可動型をスライドさせて加飾フィルムの上から2液のウレタン(透明)を射出(注入)する工程である。ウレタンの装置はcannonであり、従来はKraussMaffeiの金型内塗装で使用されていたが、ENGELとも取引を始めたとのことである(写真13)。成形品は写真14に示す。
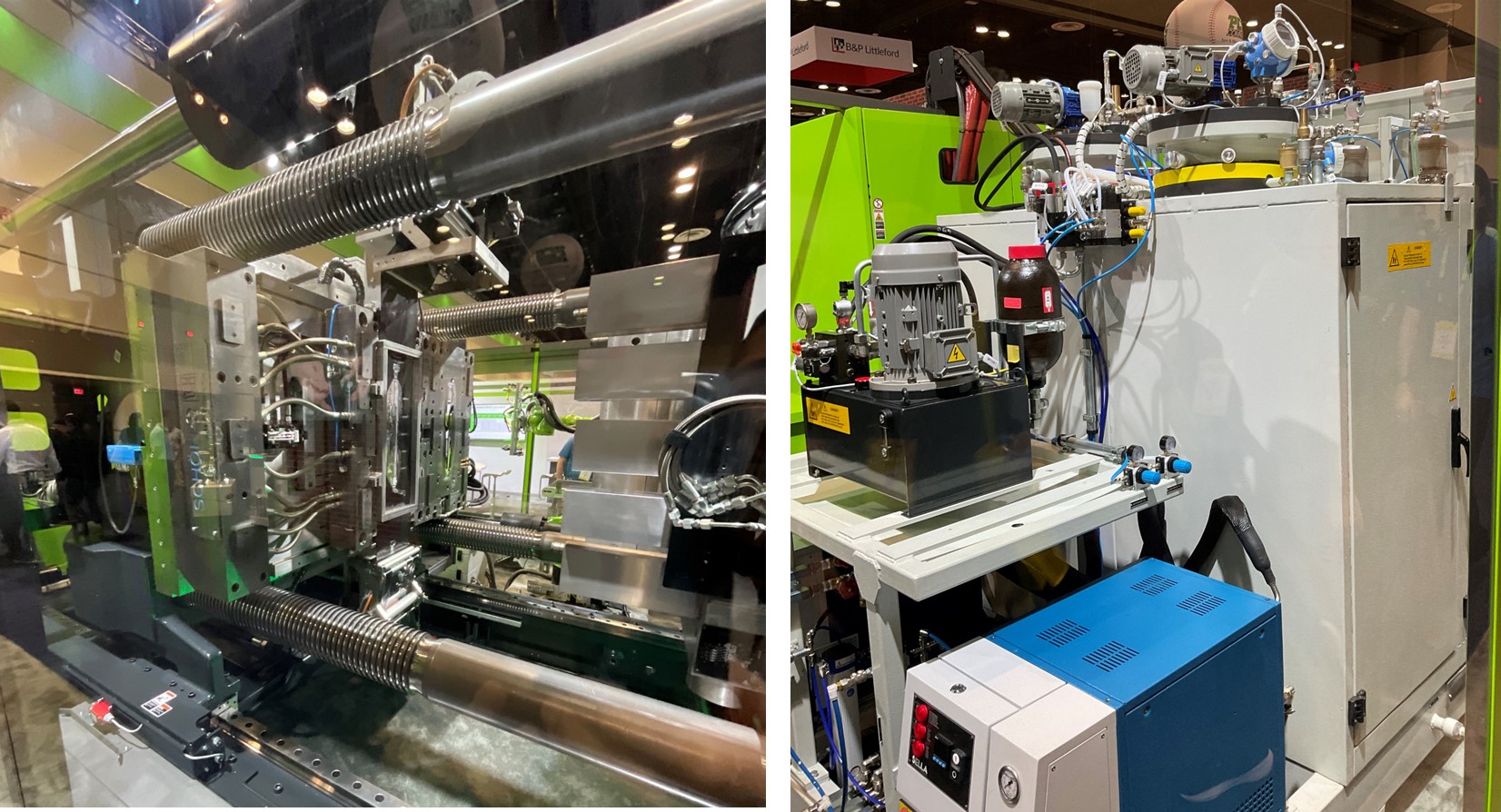
写真13 フィルムインサートと金型内塗装の組み合わせ成形の装置
左:金型が開いた状態、右:ウレタン注入装置
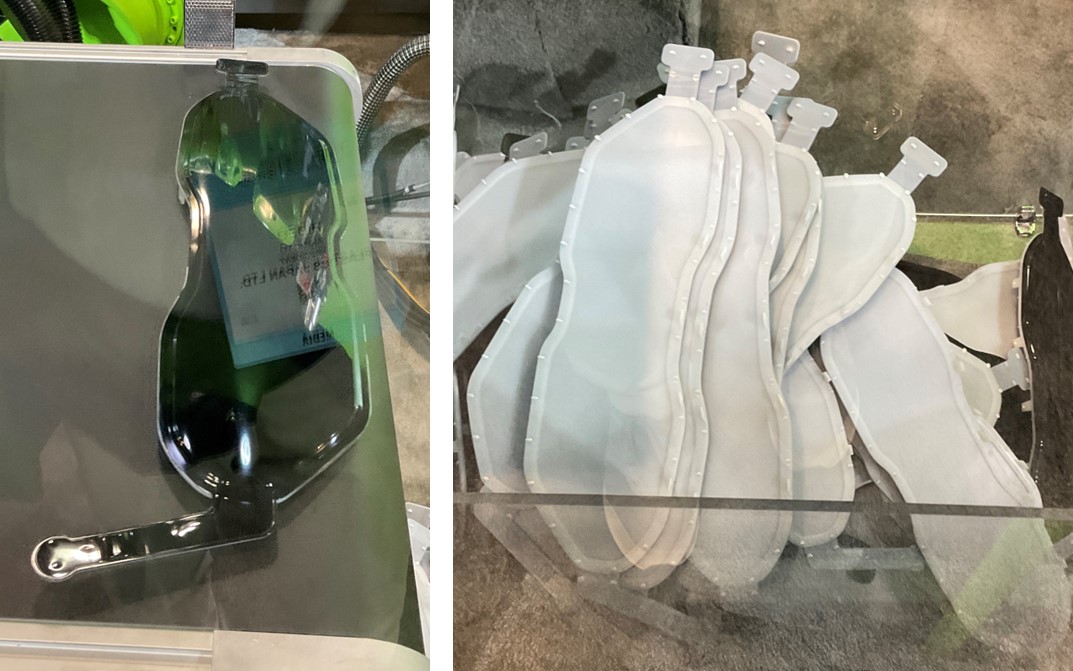
写真14 フィルムインサートと金型内塗装の組み合わせ成形品
左:透明ウレタン側、右:白色P側
2-4-2 2型を入れ替えながらの成形
素早い金型交換は生産性向上に有効である。ここではストーブリのコネクタで簡単に金型取付ができる状態の2型を7分ごとに入れ替えた実演を行っていた。待機中の金型(写真15)にも温調器に接続して型温調整しているため型交換が済むとすぐに良品が得られる。この実演では金型は台車に載せて人が押して移動させていたが、この部分も自動化可能である。写真16はそれぞれの金型を用いた成形品である。なお、成形機はタイバーレスである。
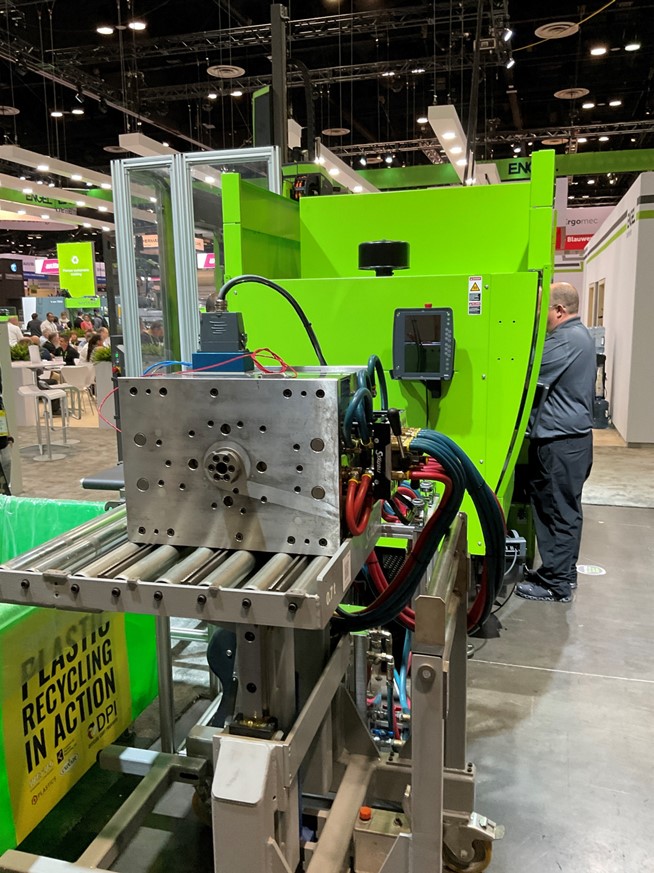
写真15 台車の上で型温調整しながら待機する金型
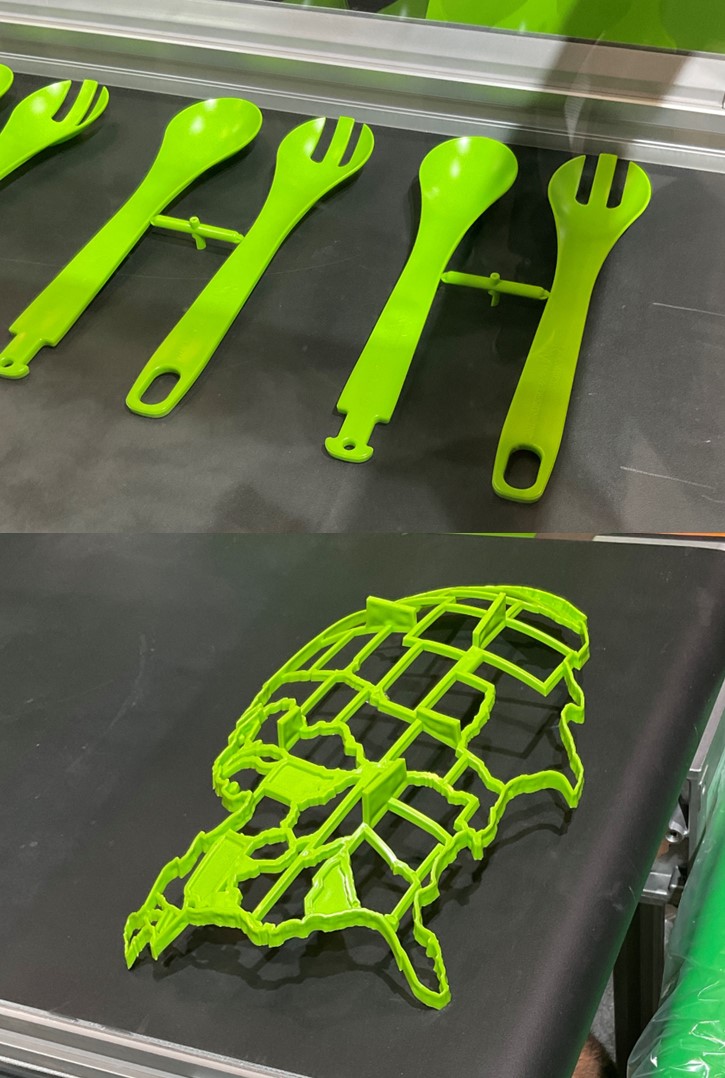
写真16 7分ごとに金型交換して成形したサンプル
2-4-3 使用済みプラスチックからの直接成形
使用済みのHDPE粉砕混合物を用いてボトルトレー(写真17)の成形を実演していた。成形機は新製品であり、全電動でスリムな寸法になっている。
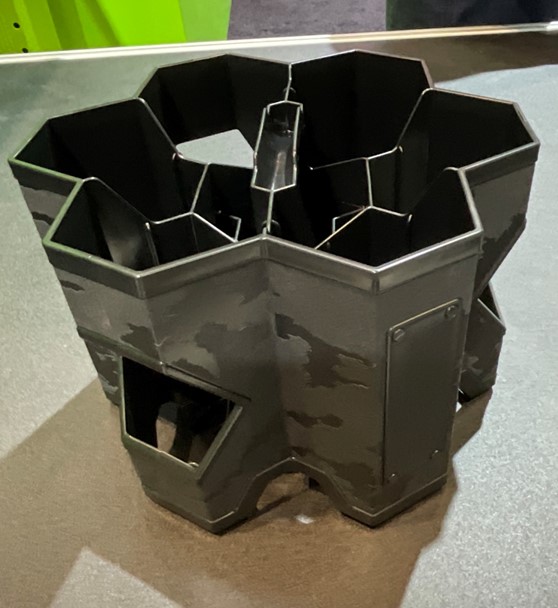
写真17 使用済みHDPEから成形されたボトルトレー
2-5 Arburg
K2022と同じツールボックスのデモを行っていたが、早朝から長蛇の列ができていた。おそらく出展者パスで早めに入場して並んでいたのであろう。その他にお得意のCUBE金型を使った2材成形、医療用のインモールドラベル成形、シリコーンの成形等を行っていた。
2-5-1 ツールボックス(フィルムインサート、ホットスタンプ)
ツールボックス本体(緑)の底と蓋をセット取りする成形で、底と蓋の4隅に真空成形されたシートをインサートする。シートをマガジンにセットする工程は人手によって行われていたが、金型へのセットは取出機が行っていた。フィルムのセットと成形品の取り出しが連続動作になっていた(写真18)。材料はPC/ABSであった。取り出し後にホットスタンプで会社のロゴを印字していた(写真19)。
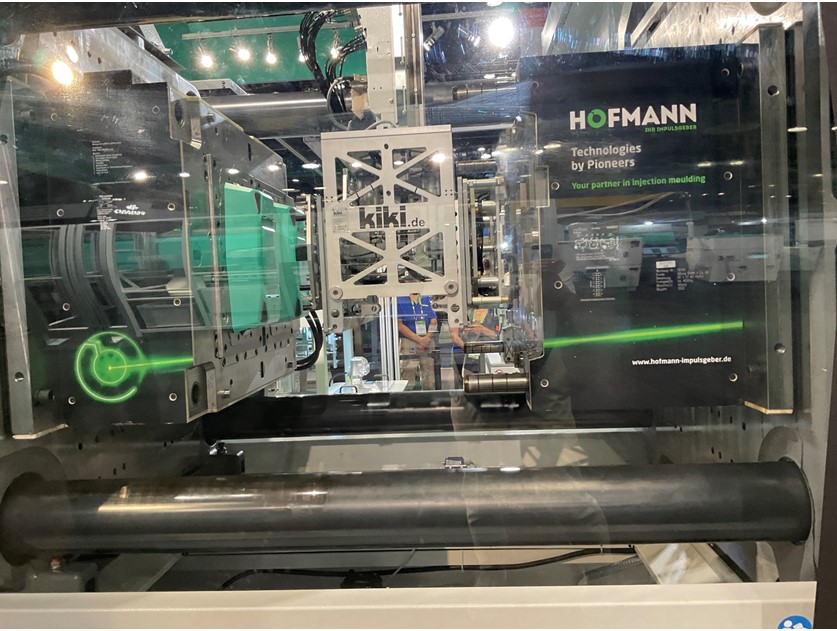
写真18 フィルムのインサートと取り出しの工程
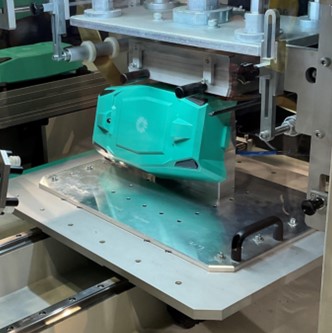
写真19 ホットスタンプ工程
2-5-2 CUBE成形
CUBE金型はFOBOHA社が得意とする技術であり、固定金型と可動金型の間にさいころ形状(CUBE)で実効4面を持つ金型である。固定型とCUBEでつくるキャビティと可動型とCUBEでつくるキャビティで同時に射出でき、残った2面のうち1面(反操作側)から取り出しができる。取り出しに要する時間が成形サイクルに影響を及ぼさない。
写真20は操作側から写したもので、この実演では操作側を向いた面では何もしない(空気冷却のみ)が、成形によってはこの面から部品のインサートも可能である。写真21は成形品である。材料は白、青ともにPPである。
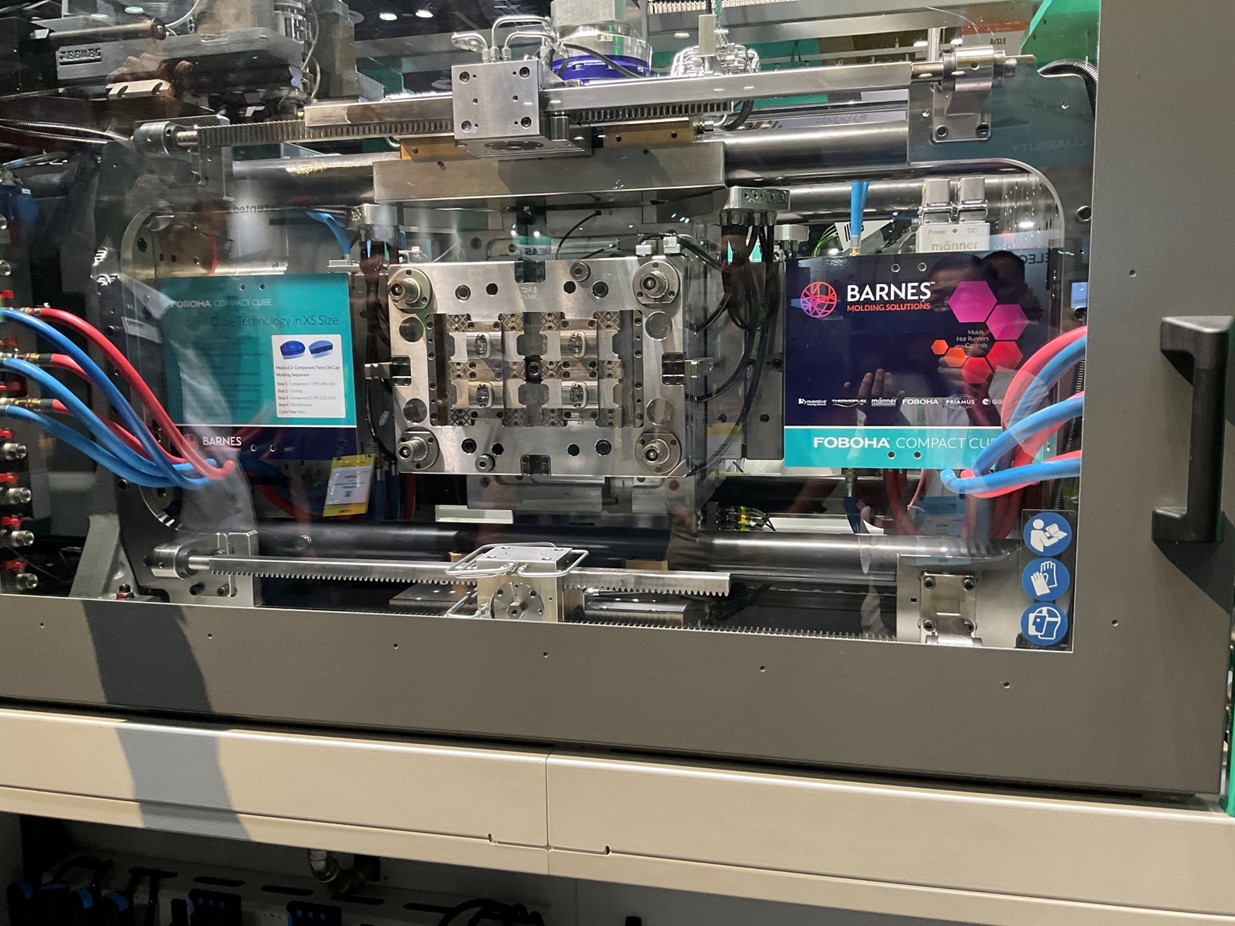
写真20 CUBE成形中の金型(操作側から)
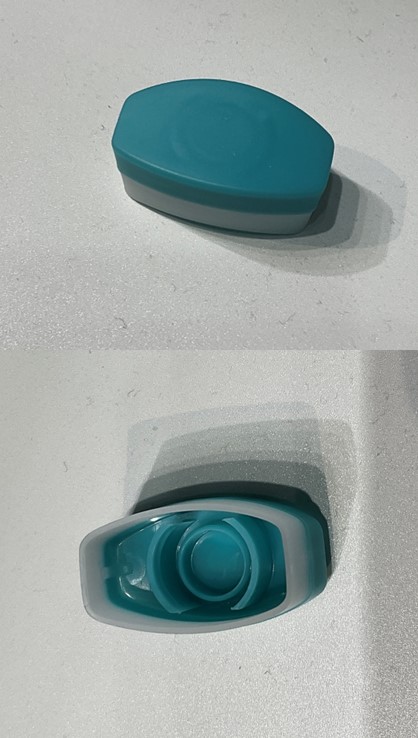
写真21 CUBE成形による2材成形品(Medical closer)
2-5-3 医療用インモールドラベル成形
医療用(検査用)の試験官に目盛を印刷したラベルを金型内で貼る成形であり、日用品用途に比べると寸法精度の要求が非常に厳しい。そのため、フィルムをセットするマガジンに置かれている位置をセンサーで測定してからロボットで取る。成形後にもラベルの位置を測定して検査していた。
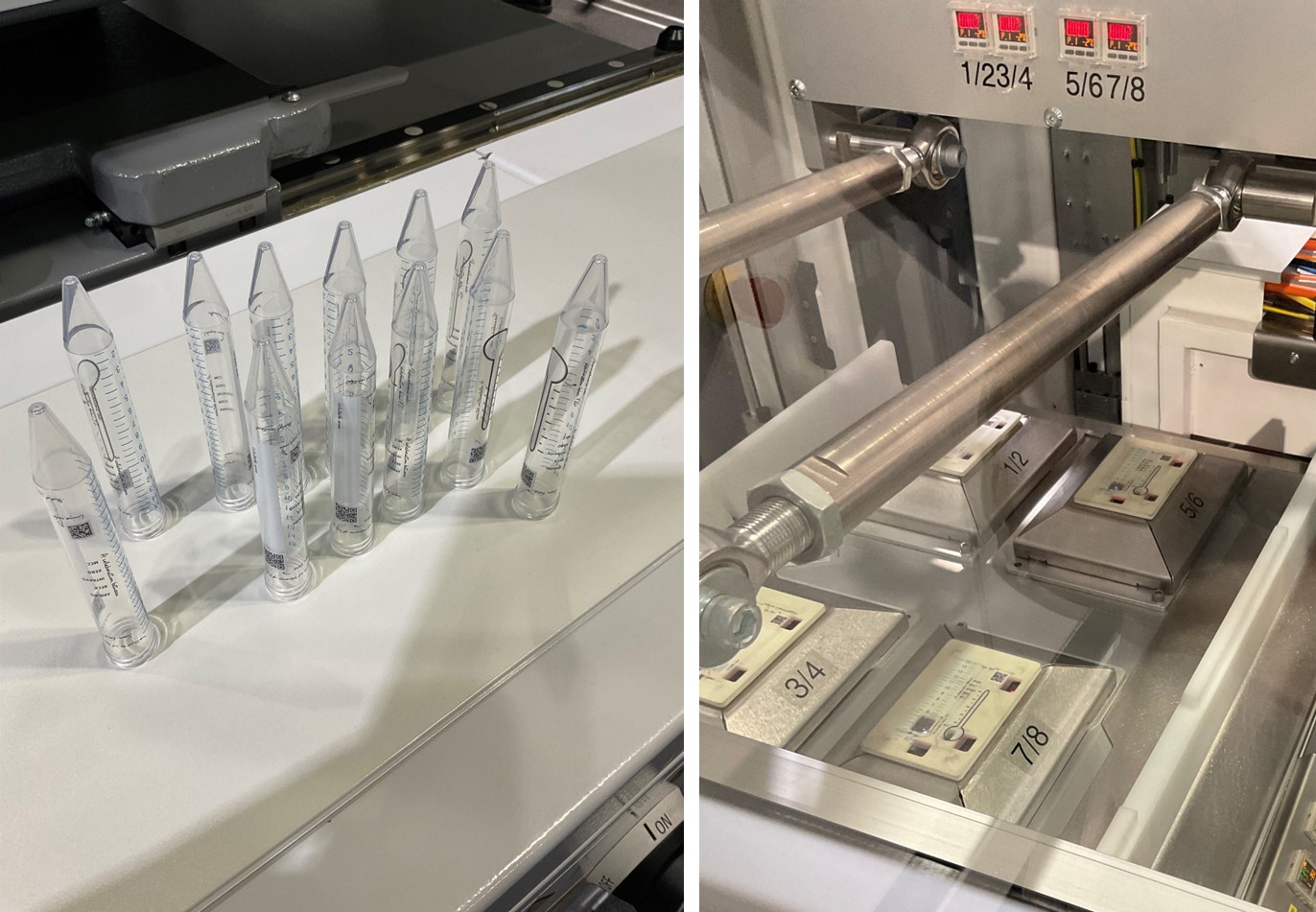
写真22 医療用チューブ(左)と目盛が印刷されたラベル(右)
2-5-4 シリコーン成形(サングラス)
2液の液状シリコーン(LSR)のレンズとPAのフレームからなる2材成形であり、金型温度が異なるLSRとPAの組み合わせは珍しい。一般によく実演される組み合わせはLSRとPBTである。
写真23はシリコーンの供給システムと金型のようすである。シリコーンの成形部分とPAの成形部分を離して別々に温調しているようだ。キスラーブースで成形実演していた「ツル(緑)」とアッセンブリーしてサングラスが完成(写真24)し、これをもらうための列ができていた。
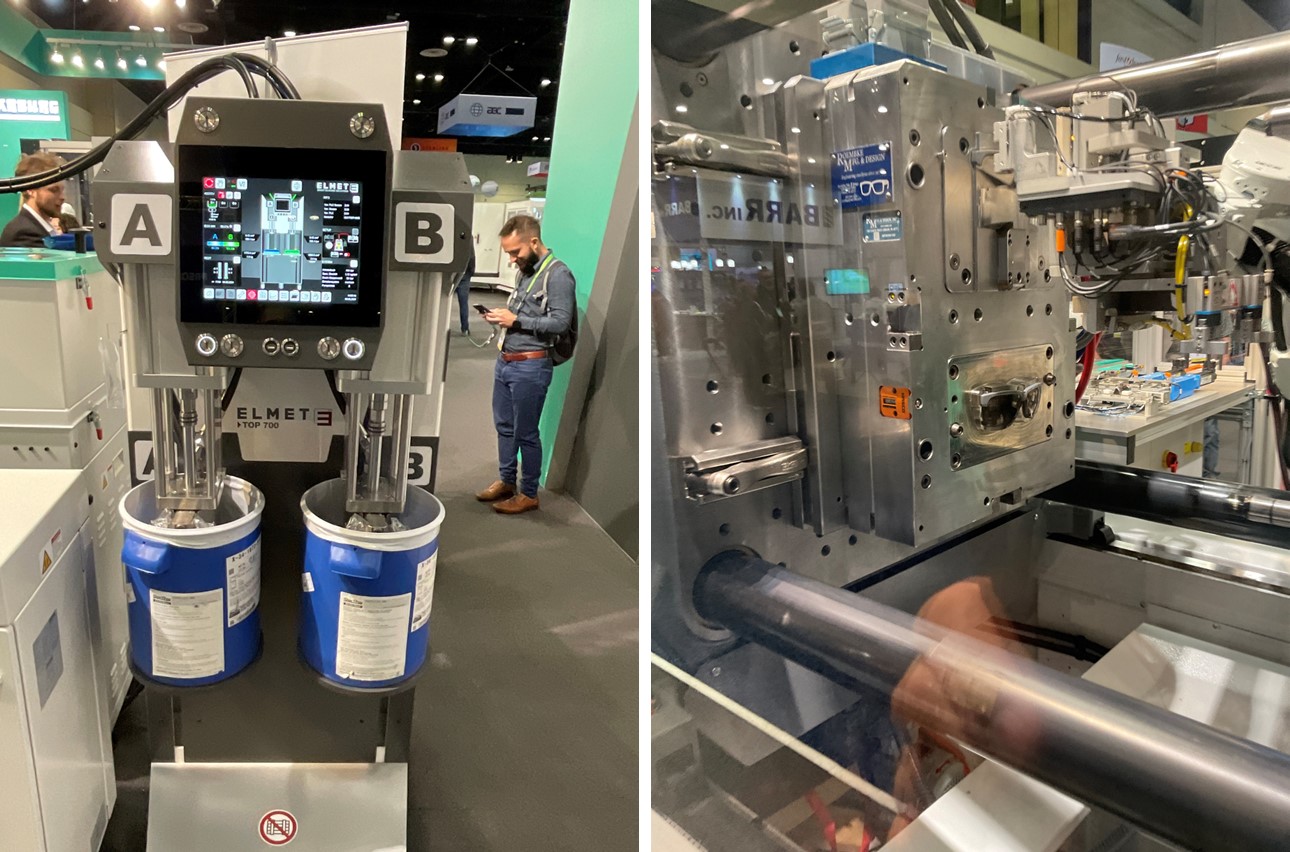
写真23 LSRとPAの2材成形(サングラス)
左:LSR供給システム、右:金型が開いている状態
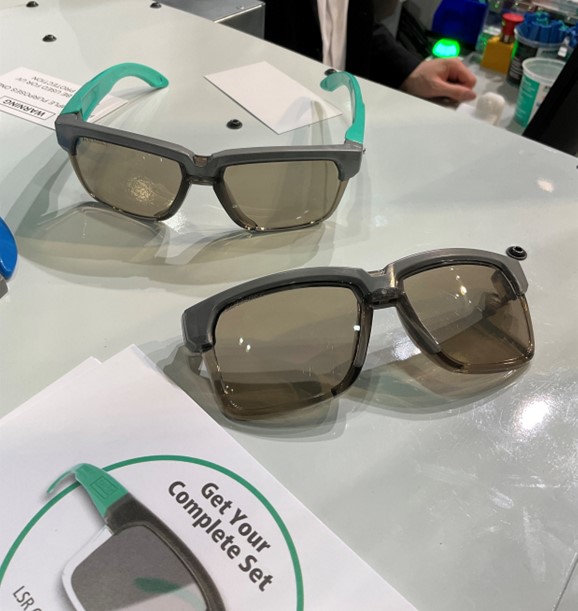
写真24 サングラス
2-6 Wittmann
超臨界窒素を用いた発泡成形を含む3材成形、液状シリコーンの成形、再生材を使用した成形における自動条件最適化等を実演していた。
2-6-1 発泡成形
成形していたのはホット飲料用のカップ(2材)と蓋である。写真25左は成形機の操作側であり、斜めの射出ユニットが非発泡のPP(自然色)、水平の射出ユニットが物理発泡成形「CELLMOULD」で茶色の発泡PPを成形、反操作側横から蓋(赤)を成形する。蓋は取り出し後にロボットがはめ込んでいた。写真25右は金型が開いた状態を反操作側から撮影したものである。
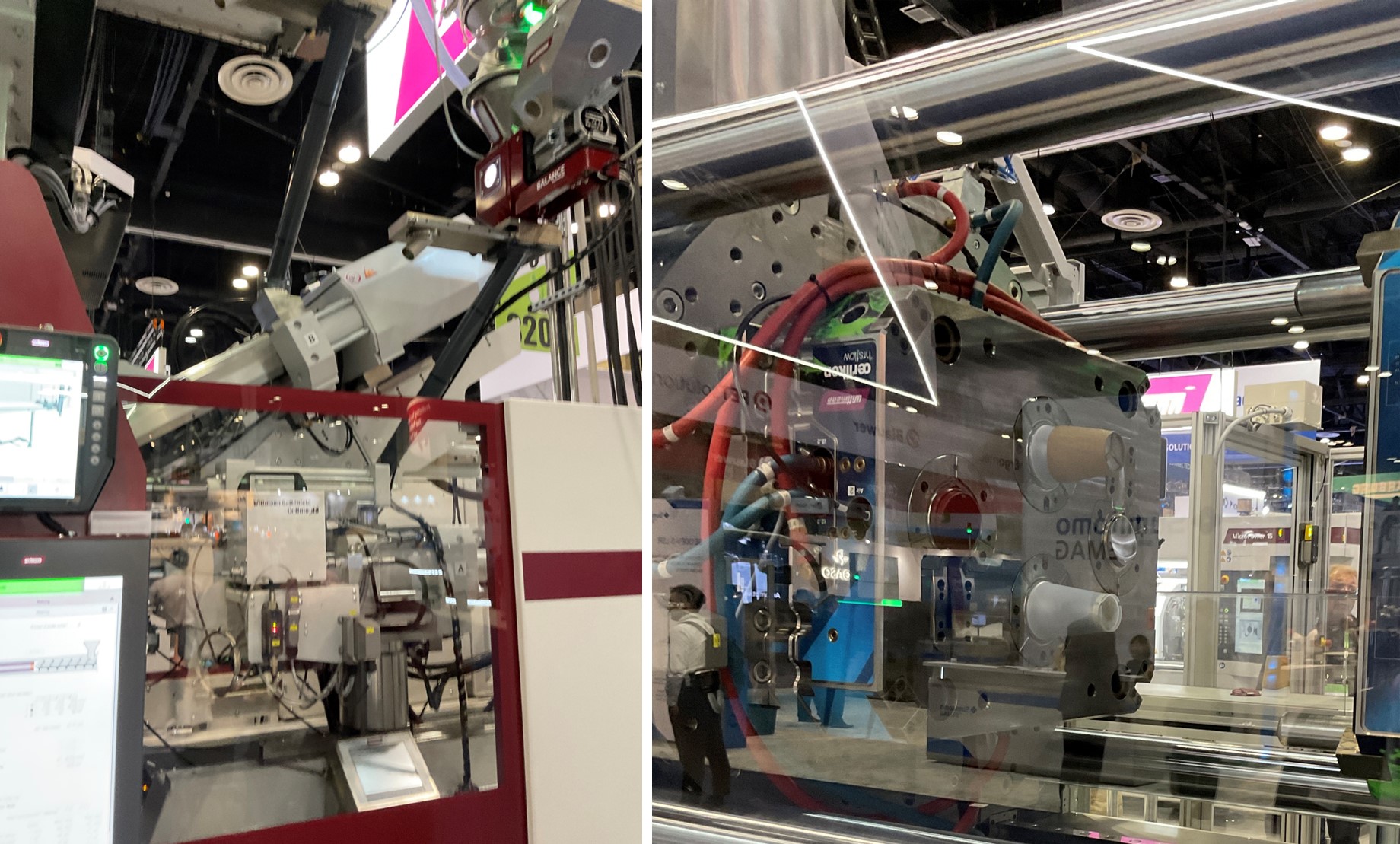
写真25 物理発泡成形を組み入れた成形実演
左:操作側、右:金型が開いた状態(反操作側)
2-6-2 成形条件自動制御
再生PPを混ぜた材料でサンルーフベゼル(セット取り)を実演していた(写真26)。ここでは成形を安定させるために成形機の圧力波形等をリアルタイムにモニタリングして成形条件を調整していた。
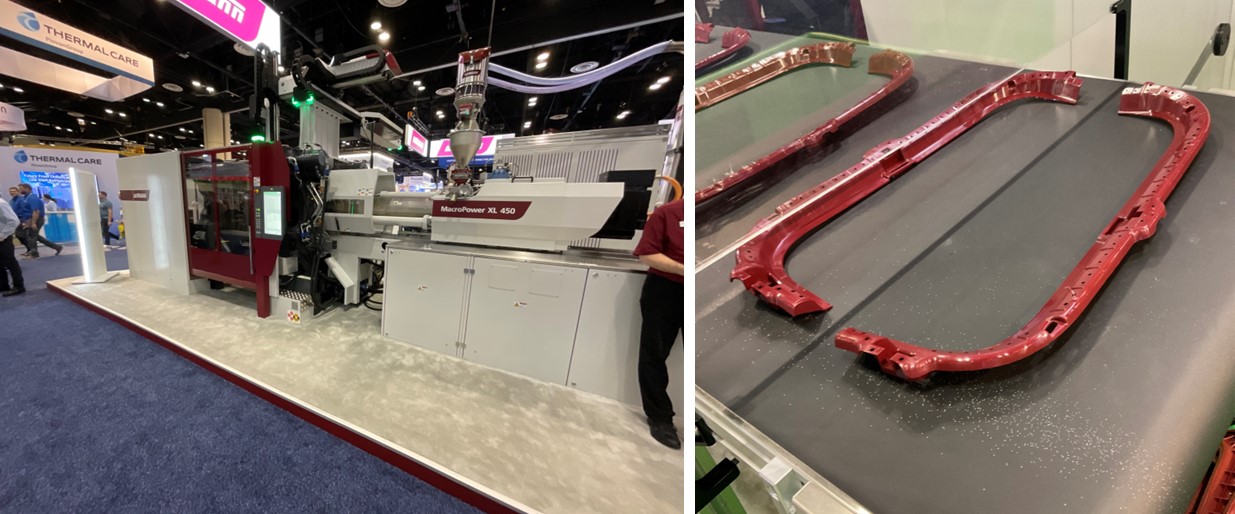
写真26 成形条件自動調整で成形されたサンルーフベゼル
2-7 Sumitomo Demag
飲料キャップ専用成形機の実演、医療用超高速成形機の実演、LSRの成形実演等を行っていた。
2-7-1 キャップ専用成形機
全電動のPAC-Eシリーズで、射出ユニットは日本で、型締ユニットはドイツで開発された。生産性を向上させるために型開きと突き出し動作を完全に同期させ、突き出した製品(キャップ)が真下に落下する。そのことで型開量を必要最小限にできる(型開時間の短縮)。また、ボールねじの冷却は、新規に開発したねじにオイルを吹き付ける方式を採用している。
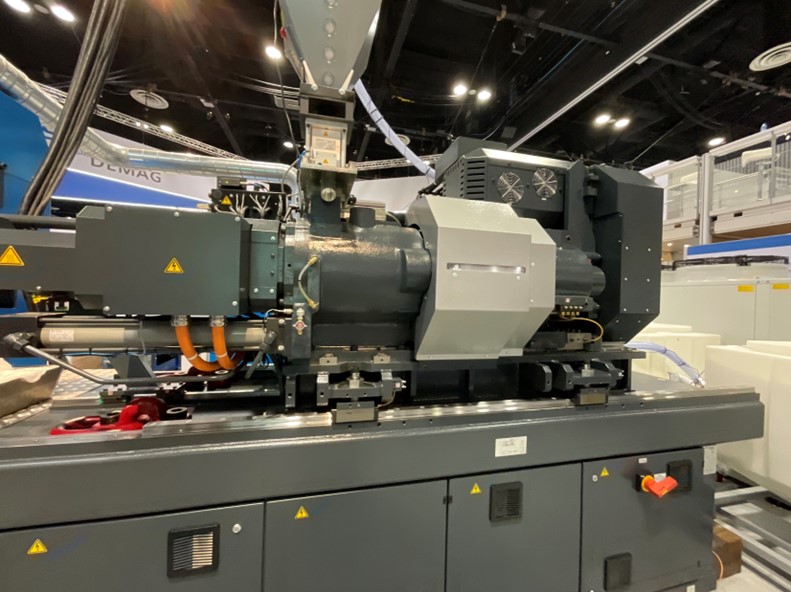
写真27 キャップ用全電動成形機
2-7-2 医療用高速成形機
高速射出を可能にするために射出開始の立ち上がり(速やかに設定速度に到達)、立下り(急減速)を可能にし、射出速度1000mm/sを実現しているメディカル専用成形機の実演を行っていた。可塑化も特殊な方法を採用しているとのこと。成形していたのは64キャビのピペットチップである。
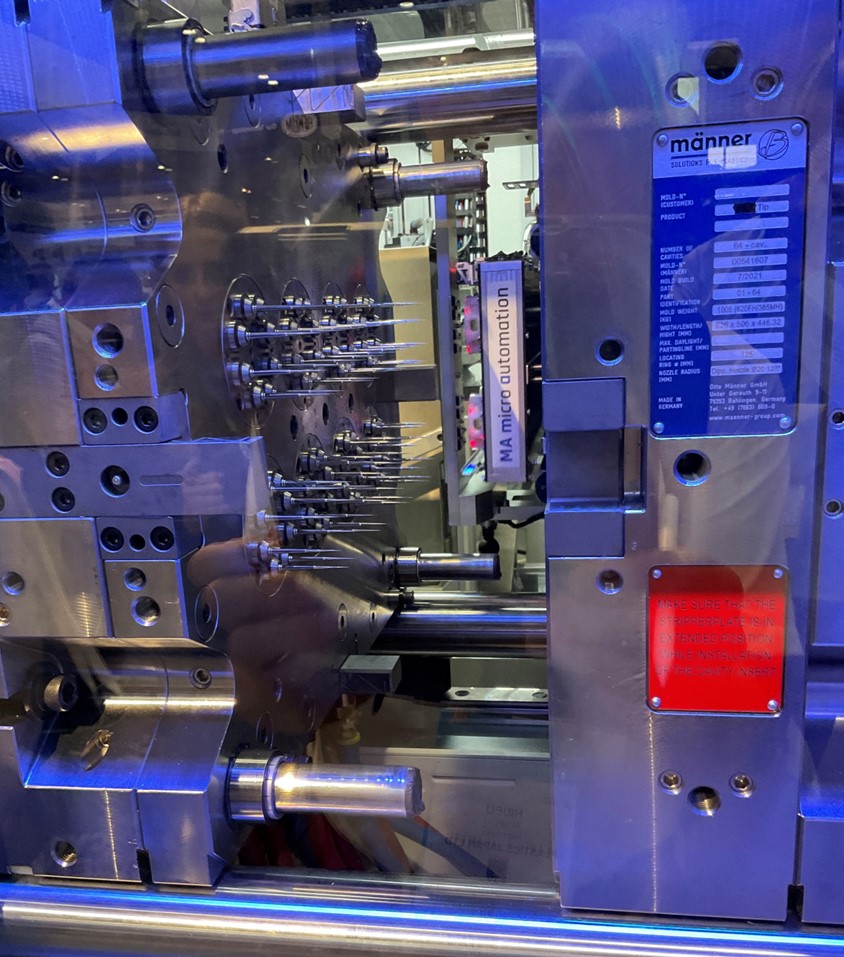
写真28 医療用高速成形機
2-7-3 LSR成形
LSRの成形は、信越のシリコーンとNEXUSのシリコーン供給装置を使い(写真29右)、MR Moldの金型で成形していた(写真29左)。成形時には金型をバキュームし、取出機でゲートカットしていた(写真29中央)。成形品はメディカル用途のReseal Valveである(写真30)。
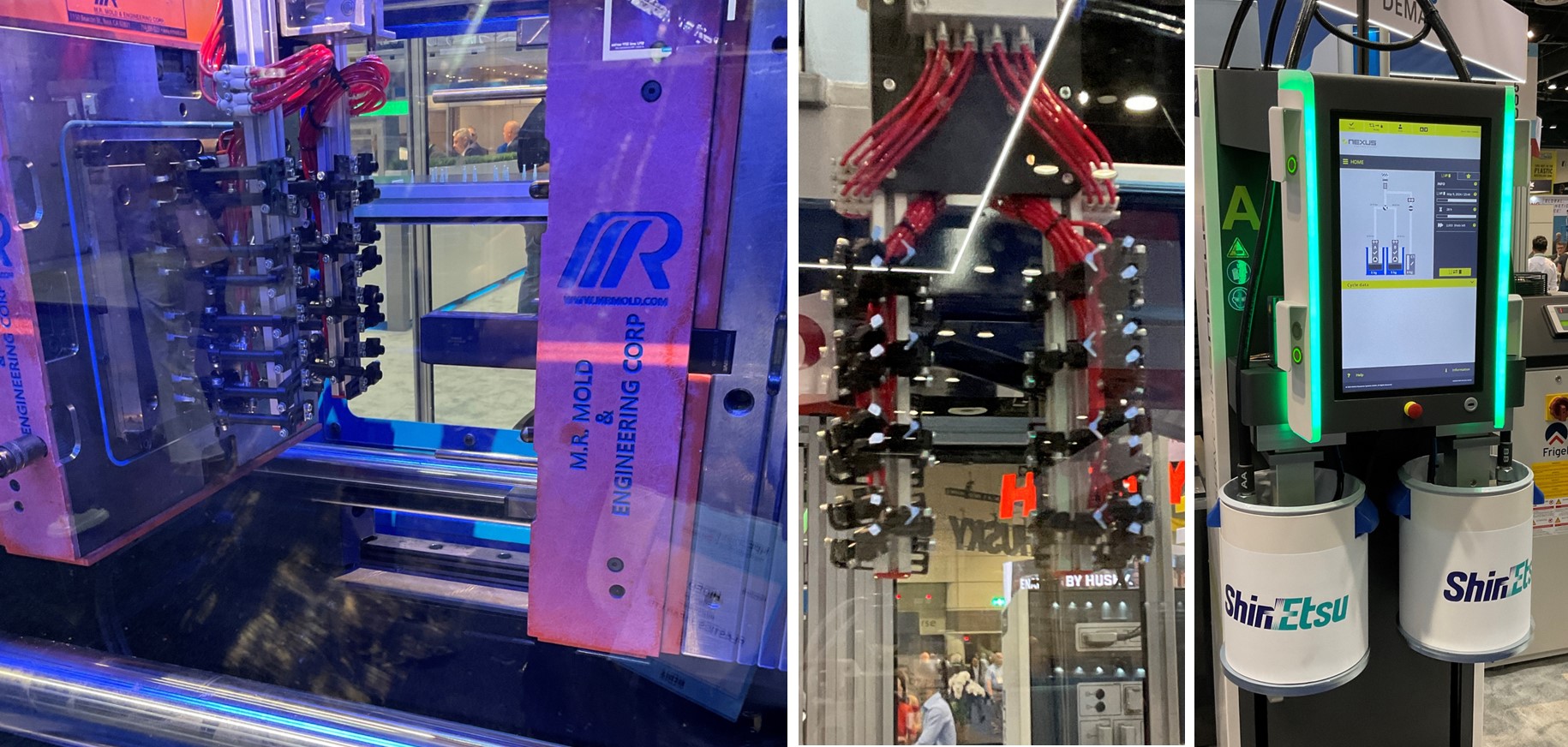
写真29 LSR成形 左:金型、中央:取出機、右:シリコーン供給装置
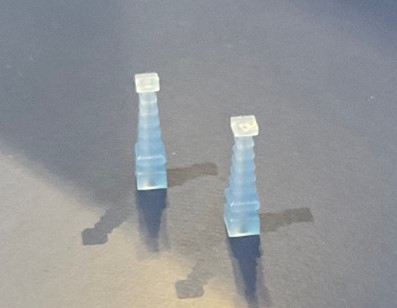
写真30 シリコーン成形品
2-8 Shibaura
圧縮窒素ガスを用いた物理発泡成形(コアバック)、インモールドラベル成形、二色成形等を成形実演していた。
2-8-1 物理発泡成形
マクセルから技術ライセンスを受けた物理発泡成形で、IPF2023と同じ実演である。IPFでは圧縮空気を使用していたが、今回のパネルには「Nitrogen gas assist」と書かれていた。また、AI Auto Correction機能で成形条件を安定させていた。
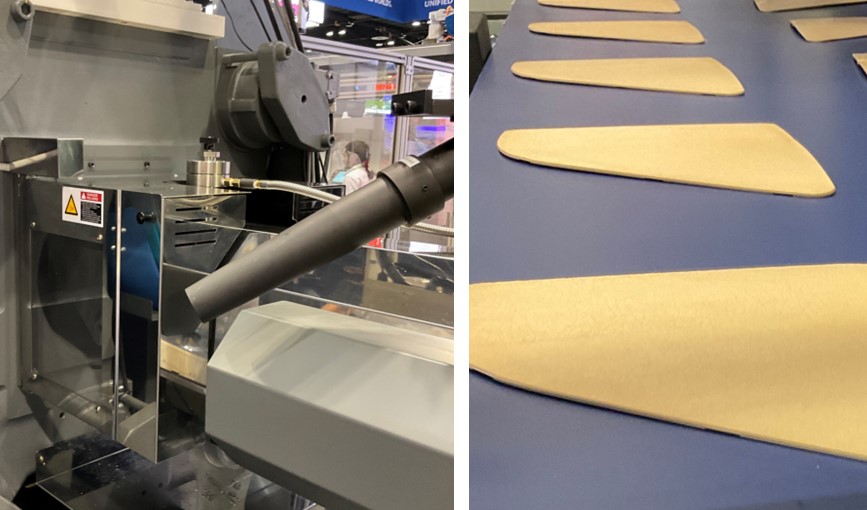
写真31 物理発泡+コアバックの実演
左:物理発泡剤の注入口、左:成形品
2-8-2 インモールドラベル成形
大型バケツのインモールドラベル成形を行っていた。同じ金型で取っ手も成形(外付けの射出ユニット)し、金型外でロボットにより取り付けていた。製品は1個取りであった。
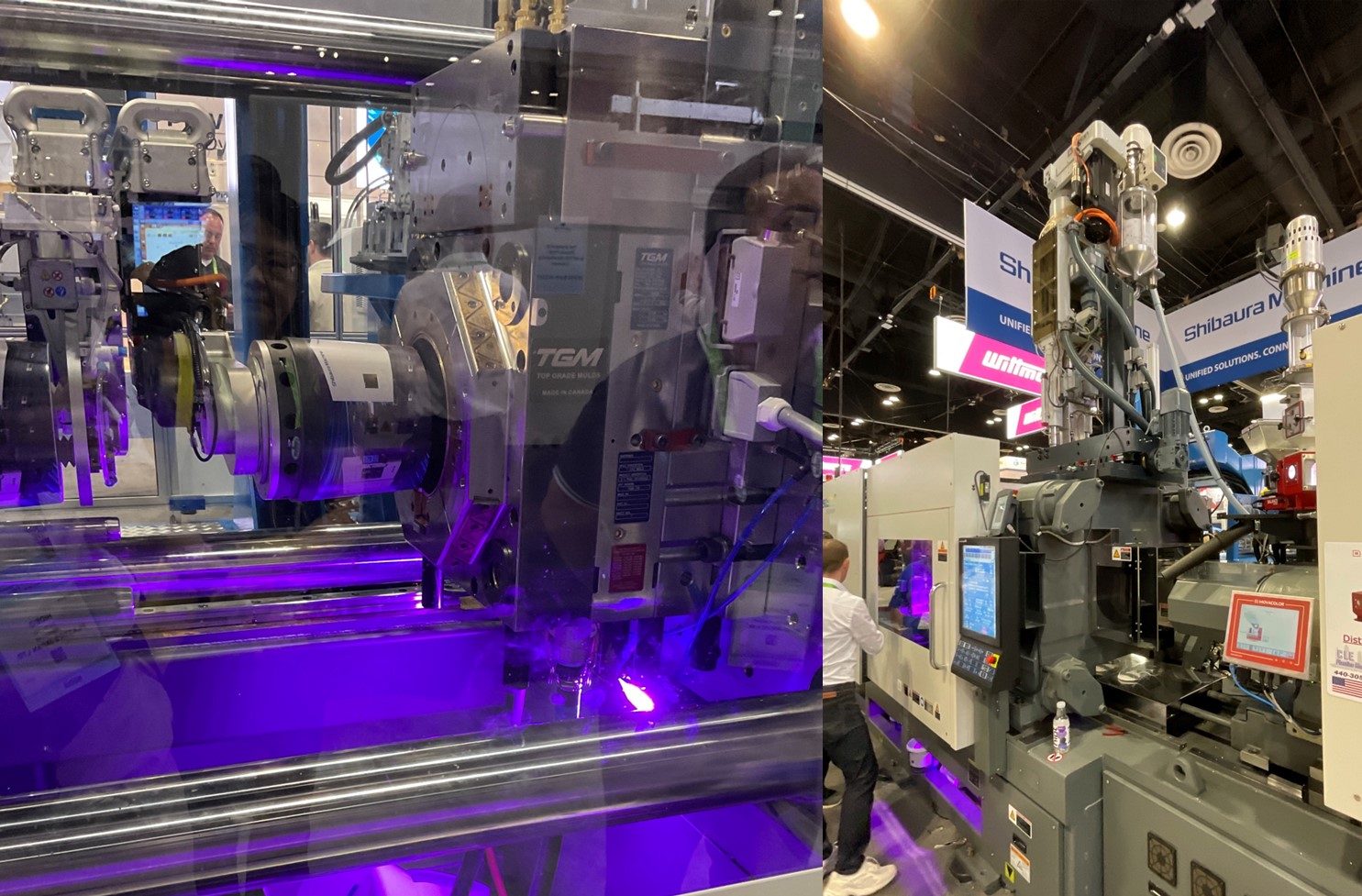
写真32 インモールドラベル成形
左:金型部分、右:縦に配置したサブ射出ユニット
2-9 UBE
2-9-1 2プラテン成形機
2プラテンの省スペース成形機をドライ運転(成形せずにプラテンを動かすのみ)で展示していた。説明パネル(写真33)には応用例として長繊維強化材料の成形(例として自動車のバックドア)、コアバック発泡(4本のタイバーを平行を保って移動させる)、MuCell成形が書かれていた。
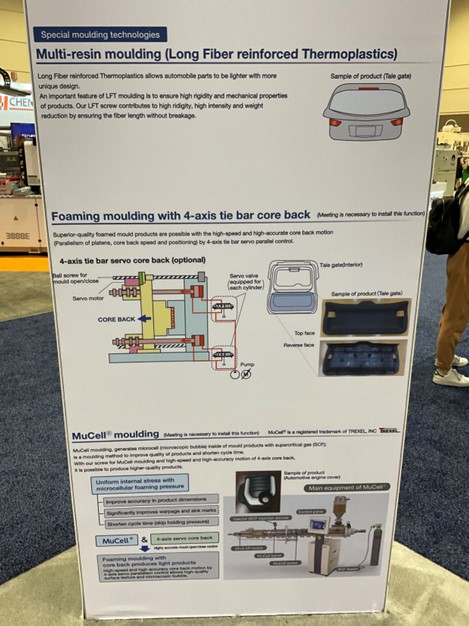
写真33 応用事例の説明パネル
2-10 JSW
キャノンモールドの「シャトルモールド」技術を用いた成形実演を行っていた。その他にはバケツ、カップ(色替えのようすも実演)、ついたての成形を実演していた。
2-10-1 シャトルモールド
「シャトルモールド」は2個の金型を1ショットごとに入れ替えて成形を行う手法で、射出・保圧時と取り出し時は成形機に取付け、それ以外の時間(冷却)は成形機の外に出す。2つの金型は操作側と反操作側にある待機場所で冷却を行いながら待機する。1ショットごとの入れ替えなので、温調配管、ヒーターやセンサーの配線は接続したままで、金型の固定も無人で行われる。
写真34の左は反操作側の待機場所、写真34の右は操作側の待機場所である。
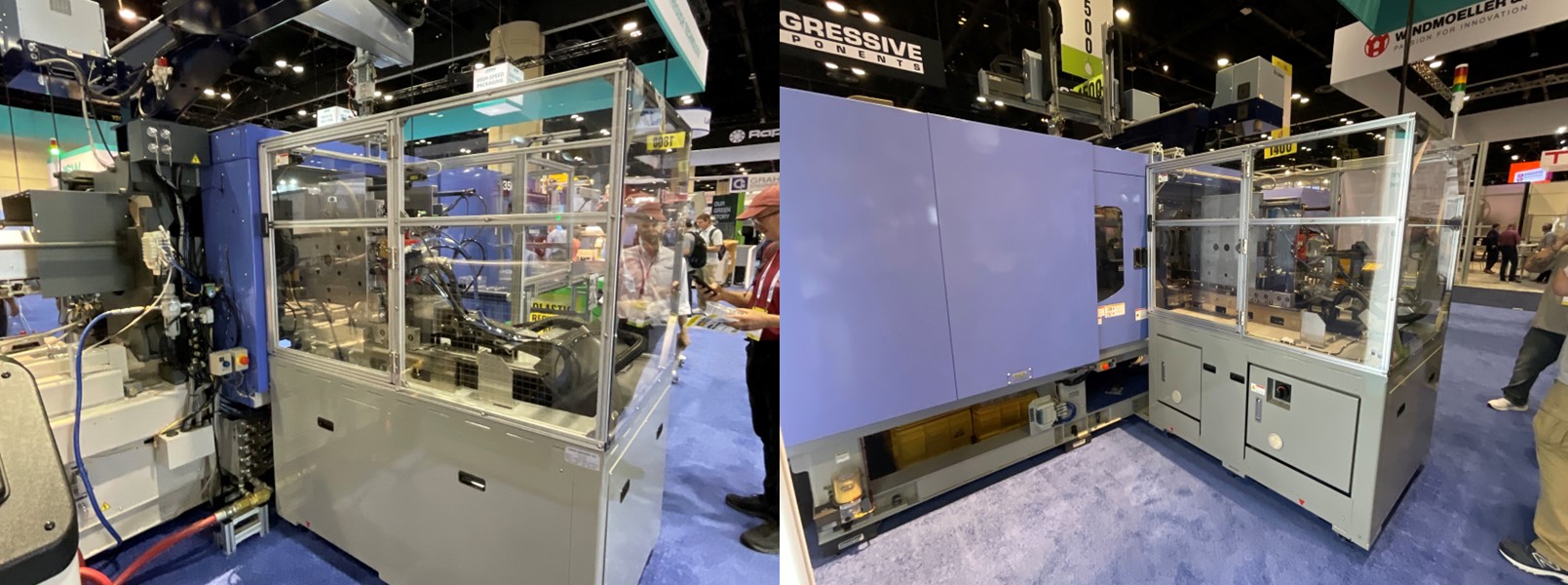
写真34 シャトルモールドの装置
2-11 TOYO
TOYO(東洋機械金属)はマルカアメリカのブースで展示していた。従来マルカアメリカはもっぱらTOYOの成形機を販売していたが、完全電動化に伴い油圧機が欲しい顧客向けに台湾のFCSの成形機を販売している。
TOYOの成形実演は、レンズの成形および成形したレンズをインサートしてルーペを成形していた。ルーペの成形にもちいていた成形機は射出が横型で型締は竪であり、ロータリーテーブルに乗せた金型(上下に開く)のパーティングラインから射出していた。
2-12 NISSEI
3材による成形と金型内組み立て、サンドイッチ成形と化学発泡の組み合わせ、LSRの成形、デザインシボが入った板状製品の成形等を成形実演していた。
2-12-1 3材成形と金型内組み立て
メインの射出ユニット(赤)に加え、後付けの射出ユニットを2本(黄とナチュラル)取付け、金型内で組み立てることで仕切り版と蓋が組み合わさったシール容器を完成させていた(写真35)。写真手前は蓋を外した状態で撮影したものである。
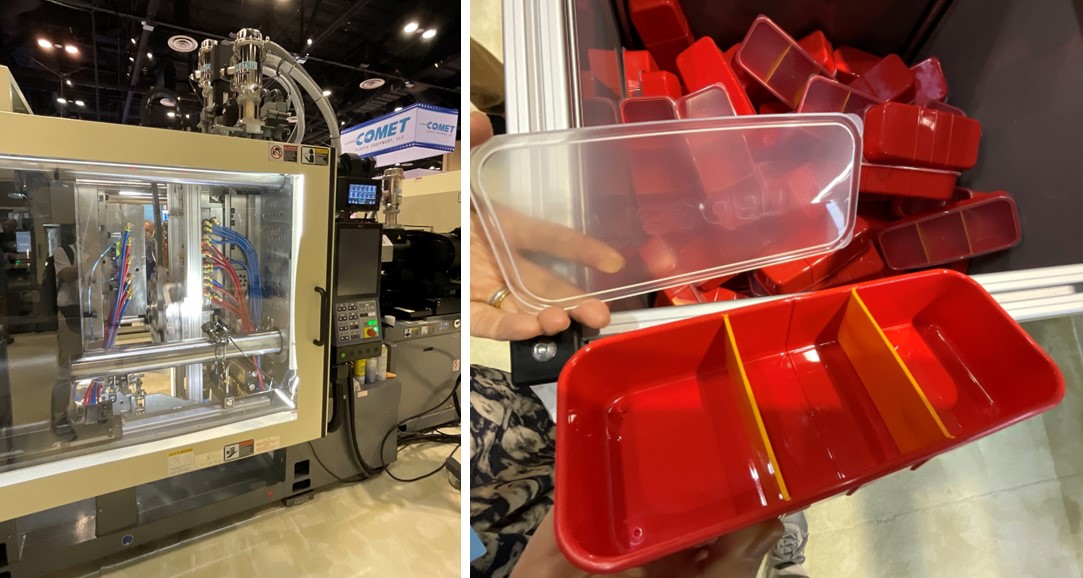
写真35 3材成形と金型内組み立て
左:成形機の外観、右:組み立てられた成形品
2-12-2 サンドイッチ成形と発泡成形の組み合わせ
TPEでリサイクルPP(化学発泡)をサンドイッチした成形を実演していた。写真36左は装置の外観、右上は材料合流の模式図、右下は成形品である。
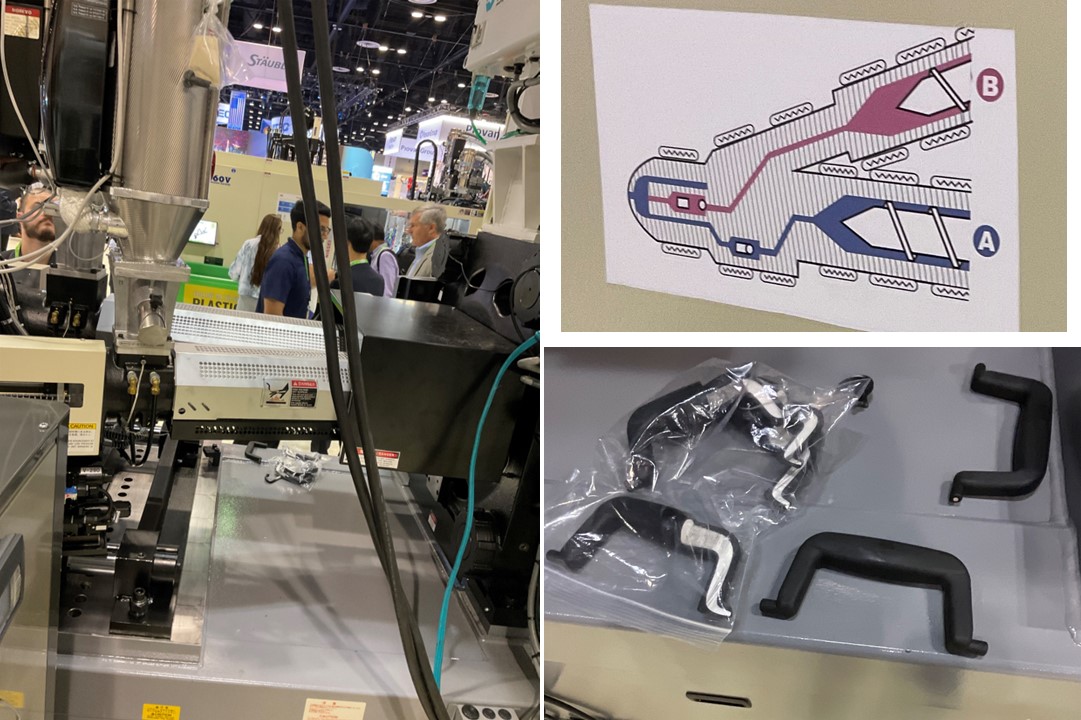
写真36 サンドイッチ成形
2-12-3 LSRの成形
実演していたLSRの成形品(写真37)と装置の外観(写真38)を示す。
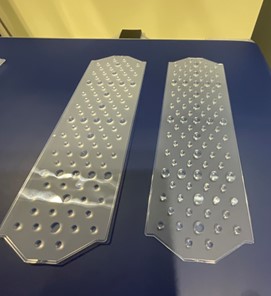
写真37 LSRの成形品
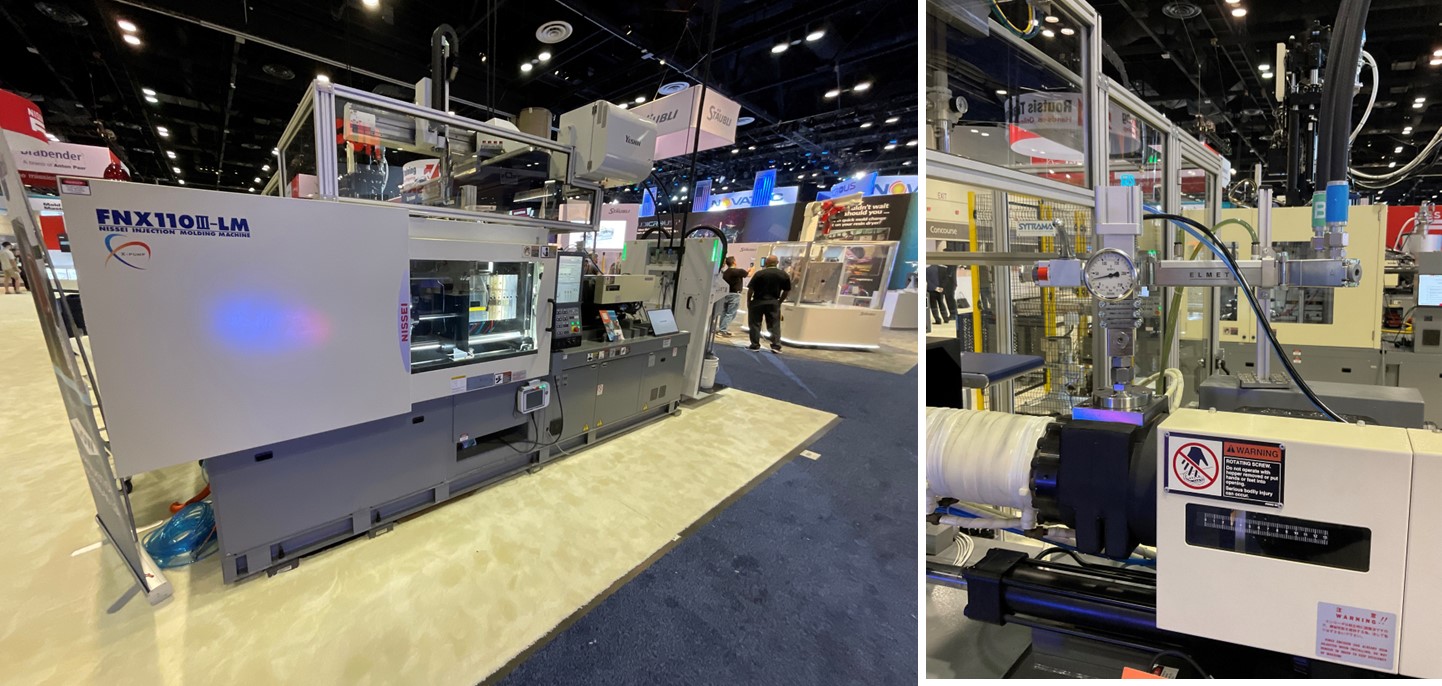
写真38 LSR成形の装置
左装置の外観、右:LSRの注入部分
3.ブロー成形機
3-1 ASB
日精ASBのブースでは射出延伸ブローの成形実演を行っていた。同社の装置はプリフォーム成形から延伸ブローの工程を1台の装置で完結できる(写真39)。今回の実演の中ではカップの成形が行われていた。真空成形では達成できない深さのカップを成形するためにプリフォームの形状を平板にすることや予熱方法に工夫がなされていた(写真40)。
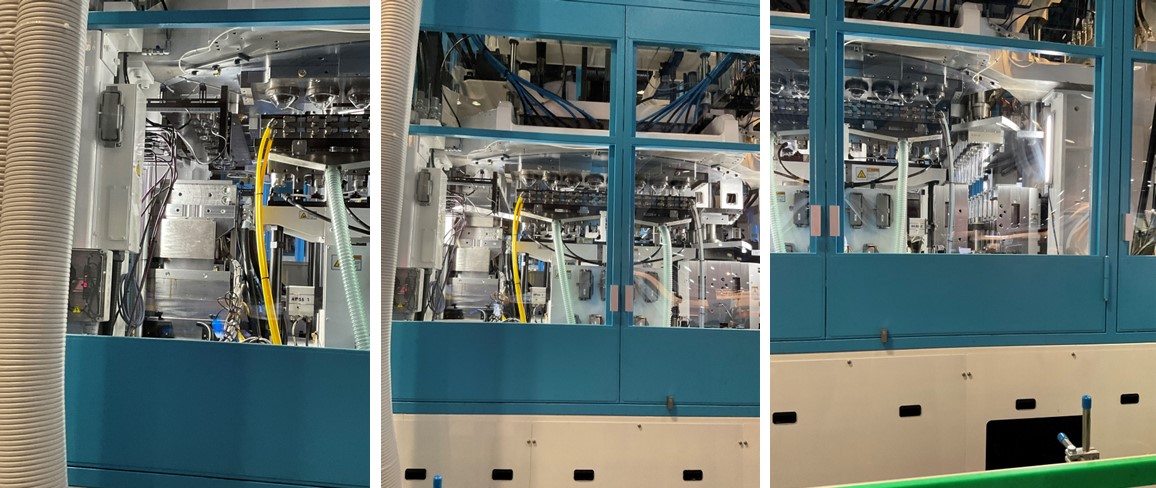
写真39 射出延伸ブローのようす
左:平板プリフォームの成形、中央:加熱と延伸、右:ブロー
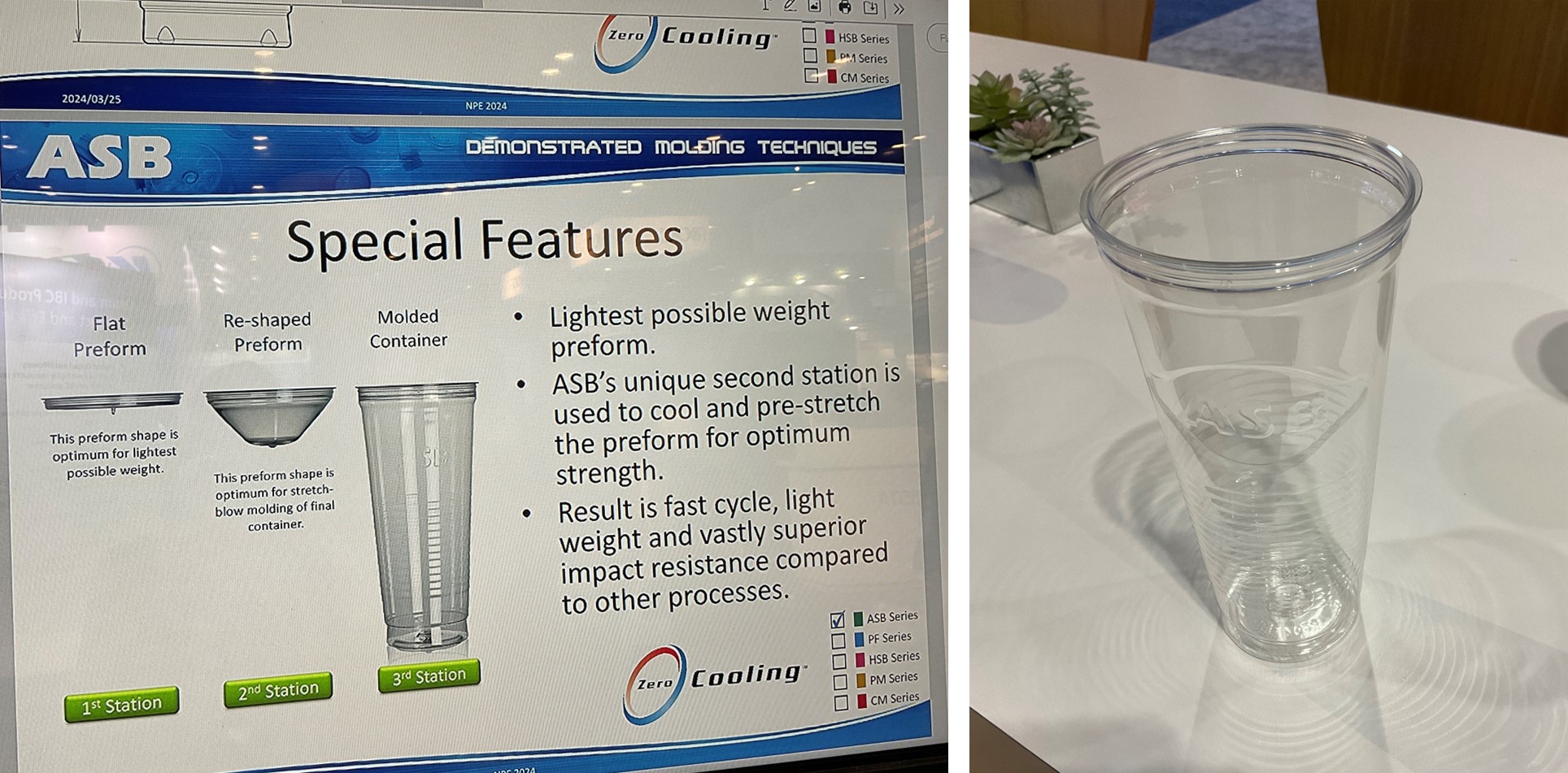
写真40 平板プリフォームを使うことの特徴をしめしたパネル(左)とカップ(右)
4.おわりに
成形機メーカーの展示についてレポートしたが、他にも興味深い展示があったことを付け加えておく。